AI-Driven Predictive Maintenance: The Future of Reliability in Power Plants
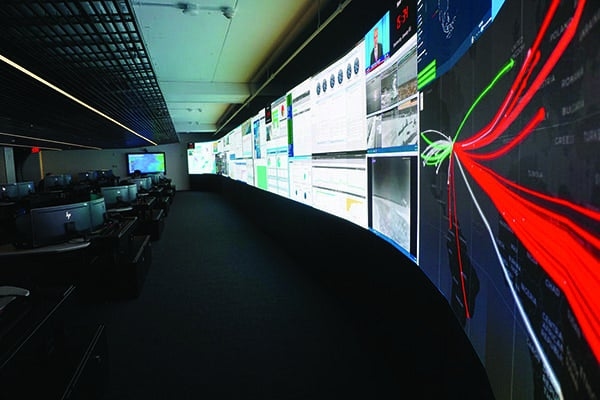
Artificial intelligence (AI) is transforming the energy sector, helping power plant operators optimize efficiency, reduce emissions, and prevent costly equipment failures. By analyzing vast amounts of real-time data, AI models can identify anomalies in equipment behavior, optimize fuel consumption, and enhance overall plant performance. According to industry estimates, AI-driven analytics can reduce maintenance costs by up to 30% and increase equipment availability by as much as 20%, significantly improving power plant economics and reliability.
The Traditional Approach to Predictive MaintenancePredictive maintenance is a proactive approach to equipment management to detect early signs of wear and failure. Traditional maintenance strategies have always relied on periodic inspections during planned outages or reactive repairs based on incidents. With the increase of availability in sensor data for monitoring equipment operations, this was accompanied with the automatic monitoring of equipment health by comparing key sensor values to predefined thresholds of expected values. But this traditional approach tends to create more noise for the control room operator, by catching sensor issues and faults often and raising more alarms than necessary.
AI-Enabled Predictive Maintenance and Underlying Model TypesAI-powered predictive maintenance addresses this issue, by allowing to build anomaly detection models that are trained on historical stable behavior of the equipment and can help identify anomalous behavior using the sensor data as input. By implementing AI-enabled predictive maintenance, power plants can extend asset lifespan, minimize unplanned outages, and improve safety while optimizing operational costs. And it also addresses the downsides of raising a large number of unnecessary alarms, ensuring that the control room operators can focus on the key concerns when operating a unit.
In terms of the modeling approaches used for predictive maintenance, the models fall into three primary categories, each offering unique advantages over traditional threshold-based anomaly detection methods. The choices include:
- Multi-Variate Anomaly Detection Models Using Longitudinal Data. This approach involves using machine learning (ML) models such as isolation forests or neural network–based models like LSTMs (long-short-term-memory) and RNNs (recurrent neural networks), similar to building a digital twin for the equipment. The models are generally built for each failure mode or equipment failure type and are used to auto-detect anomalies. These models enable detecting subtle deviations from normal behavior, and when connected with explainability modules like SHAP (SHapley Additive exPlanations), can also help identify the key drivers or root causes in the equipment that are causing the anomaly.
- Probability of Failure and Aggregate Anomaly Signal Models. This method is also referred to as the model-of-models approach. It involves building a predictive model for every key variable or parameter associated with a piece of equipment, by using the remaining variables of the equipment as inputs. Once all the models are trained, an aggregate model is built that calculates the error in prediction at any point in time from each of the individual models and uses all of them to create an aggregate error signal. If the aggregate error signal shows a spike, that is used to identify an anomaly. The theoretical concept of this approach is that all the parameters or variables tied to a piece of equipment should show high correlation at any point of stable running, and if they don’t, that tends to indicate an anomaly.
- Federated and Transfer Learning Models. One of the biggest challenges in predictive maintenance is the lack of sufficient failure data for newly installed or rarely failing equipment. Federated learning and transfer learning address this issue by training AI models on similar equipment from different units or plants. Federated learning enables knowledge sharing across multiple power plants without transferring sensitive operational data. By training a predictive model like a neural network on similar equipment from a different power plant, the biases and weights learned by the model can be used to identify anomalies for a piece of equipment with insufficient data. This approach ensures that plants with limited historical failure data can still benefit from advanced predictive capabilities of these AI models.
AI-driven predictive maintenance is reshaping power plant operations, enabling early detection of equipment failures, reducing downtime, and improving overall efficiency. One notable case is the work done by a large utility based in the southern U.S. It developed and deployed AI-powered models for a variety of use-cases, from improving heat rate (efficiency) by 1% to 3%, to deploying more than 400 AI models to reduce forced outages across 67 generation units—both coal and gas. This work resulted in about $60 million in savings annually and reduced carbon emissions by about 1.6 million tons—the equivalent of removing 300,000 cars from the road. These results highlight the transformative potential of AI in predictive maintenance and optimizing overall power plant operations.
As AI technology continues to evolve, its role in ensuring grid reliability, reducing costs, and supporting the transition to a more sustainable energy future will only grow.
—Nimit Patel is an AI/ML leader at QuantumBlack (AI by McKinsey & Company), leading the development and deployment of AI-driven solutions for utilities across the U.S., Asia, and Australia. His work is one of the first in industry to show successful fleetwide scaling and adoption of AI solutions, helping power companies achieve groundbreaking improvements in equipment uptime, increased efficiency, and emissions reductions.
powermag