Three steps the industry can take to create a safer future for BESS
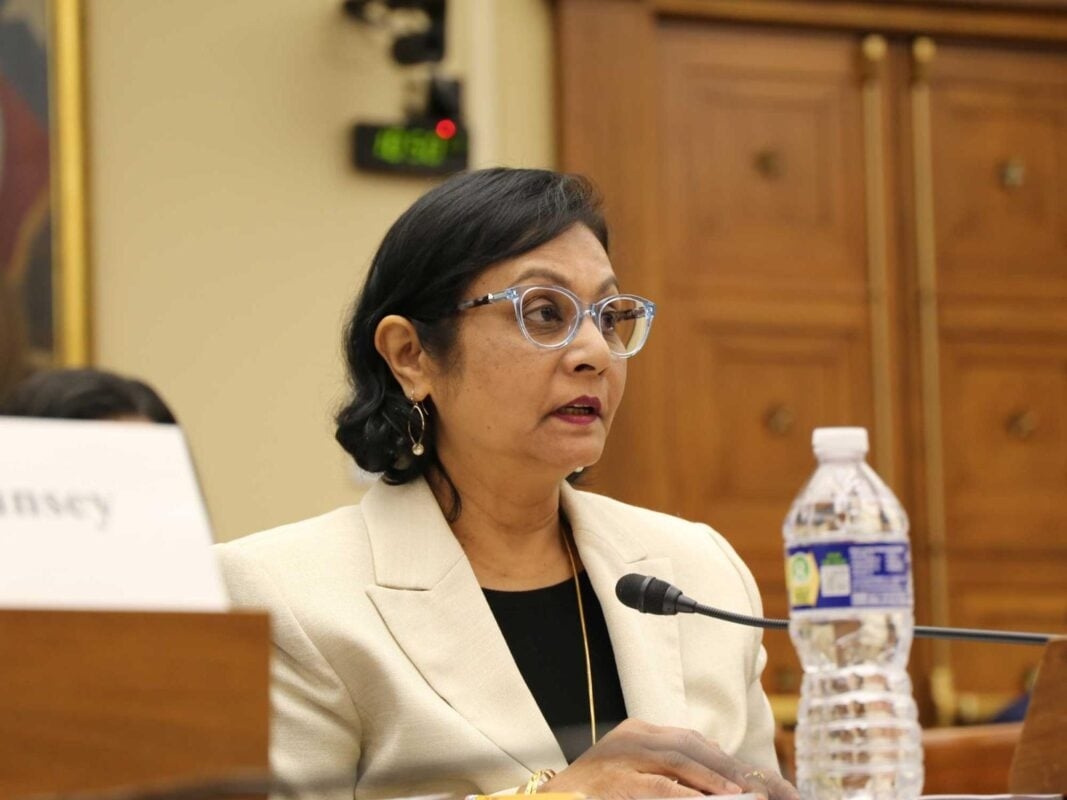
Fire risks have been a central issue with BESS applications that include lithium-ion batteries. While lithium-ion batteries have come to dominate the BESS market—thanks to their high energy density and efficiency—they also can be prone to a phenomenon known as thermal runaway if they are not designed, manufactured, charged, or used correctly.
In thermal runaway, the lithium-ion cell enters an uncontrollable, self-heating state that can result in extremely high temperatures, smoke, or fire, or any combination of these. These events typically result in the ejection of gas, shrapnel and/or particulates.
These risks are real and can emerge in virtually any application that involves lithium-ion batteries. For example, in 2019, reports from South Korea confirmed the occurrence of more than 20 fires with lithium-ion battery BESS installations.[1]
As lithium-ion batteries continue to play an important role in the transition to renewable energy, and as concerns about their safety persist, there is a growing need to improve safety protocols and design standards. Here are three key ways that manufacturers, consumers, and others operating in the lithium-ion BESS technology ecosystem can help reduce risks and advance safety.
To minimise the risk of thermal runaway, fires, and other dangers, it is critical that BESS be engineered with advanced fire prevention, detection, mitigation and suppression systems. BESS design should not only mitigate the propagation of thermal runaway if it were to occur, but it should also provide for a safe venting of gases and smoke to prevent combustion or explosions due to combustible gas accumulation in confined spaces. It also should include a highly effective fire suppression system.
In addition to such safety measures, using high-fidelity thermal models to determine safer design configurations for the environment and application can provide crucial data to enhance safety for high-voltage, high-capacity stationary grid storage systems.
At UL Research Institutes’ Electrochemical Safety Research Institute (ESRI), our battery experts are constantly assessing risks with lithium-ion cells and batteries.
This work has produced detailed insights when it comes to characterising thermal runaway and its gaseous [2] and particulate emissions [3], mitigation of thermal runaway propagation, and efficacy of fire suppressants for lithium-ion fires. It has also given us a unique view into how organisations can get ahead of the risks.
One key step that manufacturers, installers, and operators of BESS should take is to create a detailed failure modes and effects analysis (FMEA) for each product design or installation. Such an analysis proactively considers all possible failure scenarios and then pares those scenarios down to determine credible failures—providing insights that can help inform safer design and deployment.
As part of that proactive approach, BESS manufacturers, installers, and operators also should conduct further testing, analysis, and verification to confirm that they have minimised or eliminated the risks posed by the failures they identified in the FMEA.
Ultimately, a rigorous focus on testing, supported by certifications to established safety standards, can help companies validate BESS solutions and show that they meet operational and safety requirements before they are deployed.
Conduct ongoing monitoring and maintenanceTo detect issues early and ensure the long-term safety of BESS installations, companies should constantly monitor their systems. Enabling real-time data monitoring, along with regular inspections and maintenance, with the ability to recognise and fix off-nominal behaviour, is critical to early detection and resolution of risks.
Manufacturers, installers, and operators should pay special attention to systems that incorporate reconfigured cells, modules, or batteries from electric vehicles (EVs). In the past decade, these EV components have been repurposed for use in stationary grid energy storage applications, but they still require relevant tests to confirm their state of health. Once configured into batteries, they also should undergo the relevant certification tests for grid energy storage installations.
Additionally, the data and results from testing and certification should be reviewed by the relevant authorities having jurisdiction (AHJs) for conformance. Companies should also conduct periodic inspections and audits to confirm that BESS installations operate safely.
By making safety a priority at each step—from design to deployment to operation—and by proactively working to monitor, manage, and mitigate risks, organisations can minimise the risk of fires and other catastrophic events.
Moreover, a more comprehensive approach to regular system inspections, testing, and maintenance can help boost overall confidence in BESS and help accelerate the transition to clean energy.
[1]. Yun-Hwan, Chae. “ESS Units Caught on Fire Due to Bad Management.” Korea JoongAng Daily, 11 June 2019, koreajoongangdaily.joins.com/2019/06/11/economy/ESS-units-caught-on-fire-due-to-bad-management/3064174.html.
[2]. Kwon, B., Schraiber, A., Jeevarajan, J. A., “Evaluating fire and smoke risks with lithium-ion cells, modules and batteries”, ACS Energy Letters, 9, 5319-5328, 2024, doi.10.1021/acsenergylett.4c02480.
[3]. Premnath, V., Parhizi, M., Niemiec, N., Smith, I., Jeevarajan, J., “Characterization of Particulate Emissions from Thermal Runaway of Lithium-ion Cells”, Journal of Electrochemical Energy Conversion and Storage, 2024 [DOI: 10.1115/1.4065938].
Dr. Judy Jeevarajan is the Vice President and Executive Director for the Electrochemical Safety Research Institute (ESRI) at UL Research Institutes (ULRI). With more than 29 years of experience in batteries and a primary focus on the lithium-ion chemistry, she specialises in battery safety research that encompasses various aspects from thermal runaway to fire suppression and recycling.
Dr. Jeevarajan serves in the Technical Working Group for standards organisations such as UL Standards & Engagement (ULSE), Society of Automotive Engineers (SAE), International Civil Aviation Organization (ICAO)/Society of Aerospace Engineers (SAE), International Electrotechnical Commission (IEC), American Institute of Aeronautics and Astronautics (AIAA) and American National Standards Institute (ANSI).
energy-storage