Transforming Mission-Critical Utility Operations with Field Service Management Technology
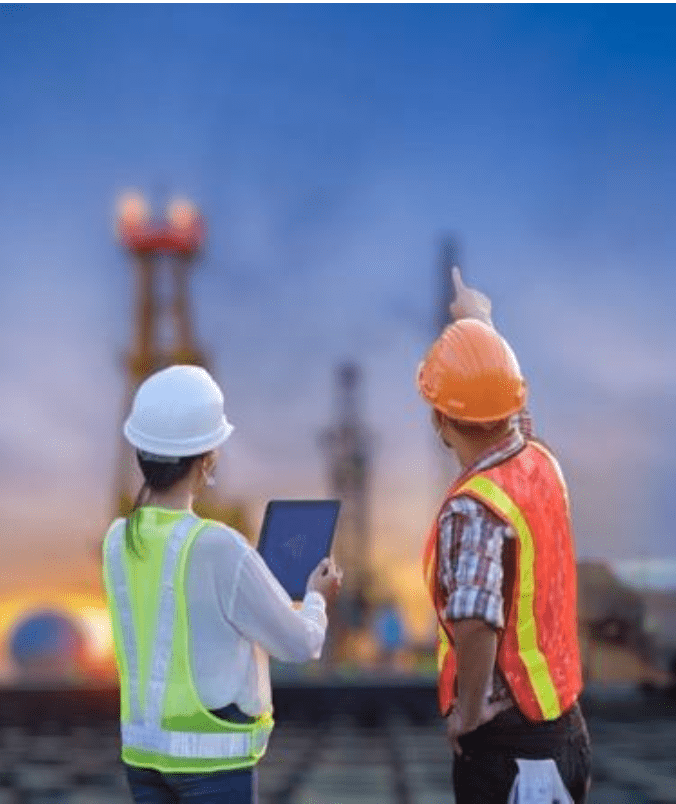
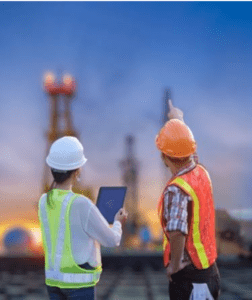
Utilities operate in high-stakes environments where operational resilience, infrastructure reliability, and workforce efficiency are essential for maintaining uninterrupted service. Cutting-edge field service management technology enhances field operations, improves safety, and streamlines emergency response with scalable automation, seamless geographic information system (GIS) integration, and predictive field service intelligence, ensuring efficiency and reliability in even the most complex operating environments. This article dives into the field service management (FSM) platform must-haves that mission-critical industries highlighted in recent surveys.
Utilities operate in tough conditions where efficiency, safety, and compliance are non-negotiable. Unexpected downtime, workforce bottlenecks, and complex asset management can lead to serious financial and operational headaches. To tackle these challenges head-on, utilities need a next-level, tailor-made solution that goes beyond outdated field management tools.
Support Mission-Critical OperationsA modern FSM platform must be purpose-built for mission-critical industries. Designed for scalability and seamless integration, the platform must enhance field operations, workforce collaboration, and real-time geospatial intelligence, enabling organizations to operate more efficiently and safely. The platform must be designed to manage large-scale field operations, supporting thousands of technicians, assets, and workflows simultaneously without performance degradation. Based on our survey of many utilities and energy service companies, the typical utility FSM requirements were identified. Many of the most important requirements are summarized in Figure 1.
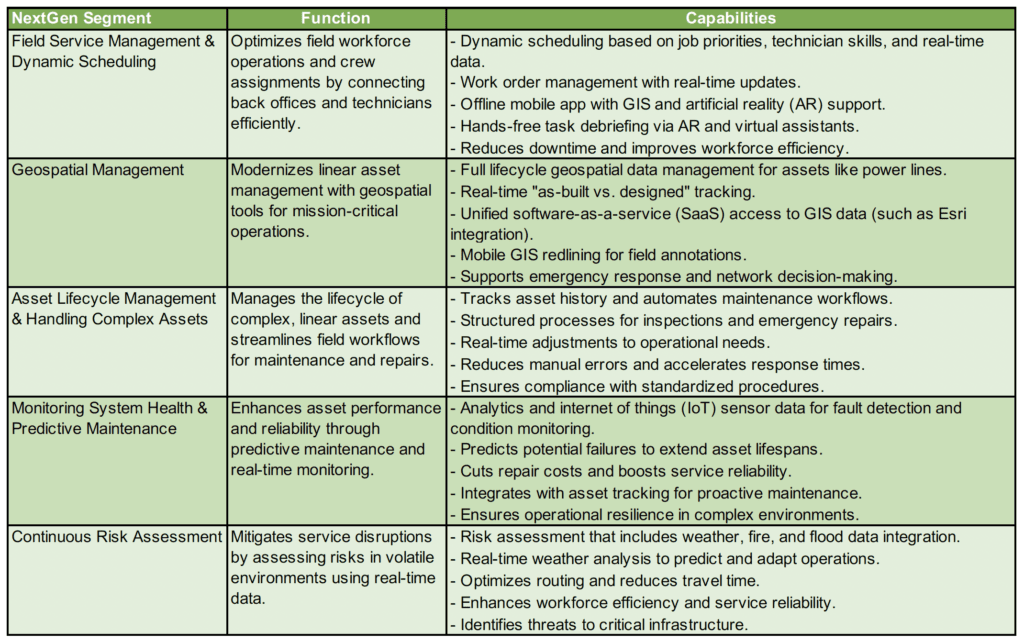
Any modern FSM platform must deliver actionable intelligence and operational precision tailored to the demands of complex field environments. That means the FSM must drive intelligent automation, predictive maintenance, and workforce efficiency. With automated scheduling, the system must ensure field teams are deployed at the right time, with the right skills, to the right location, reducing operational downtime and enhancing service reliability.
However, a mission-critical FSM solution must go well beyond basic scheduling and dispatching functionalities. It must be designed to support high-risk, high-complexity operations that demand real-time situational awareness, seamless integration with existing enterprise systems, and the flexibility to adapt to evolving industry needs, as illustrated in Figure 2.
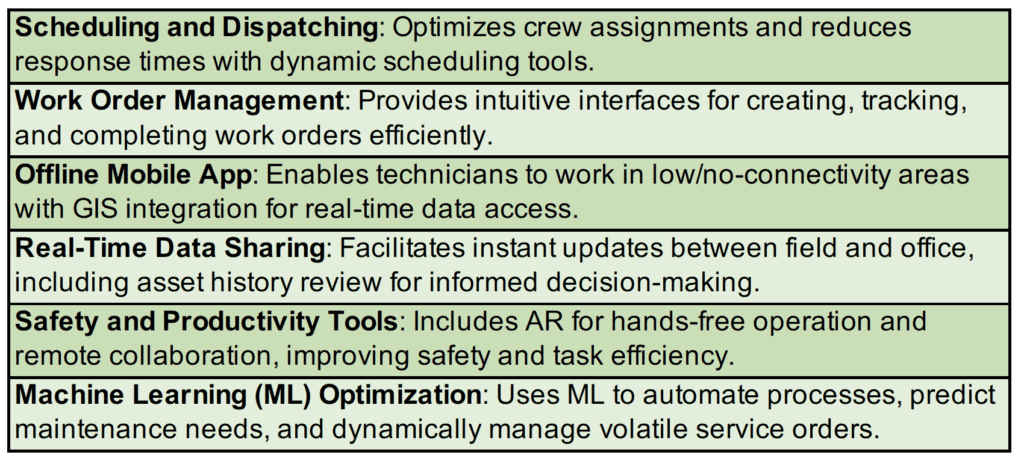
An FSM platform must provide offline capabilities to support field teams working in remote or connectivity-challenged locations while integrating GIS for precise asset tracking and management. In addition, the solution must contend with external disruptions, such as extreme weather events and natural disasters, impacting service continuity and operational stability. Managing these challenges requires a robust, scalable, specialized FSM platform.
The FSM platform must monitor job progress, workforce availability, and external conditions, allowing real-time schedule adjustments that enhance service reliability. An FSM solution must enable organizations to synchronize asset management, dispatching, and compliance tracking within a unified system. Additionally, its offline-ready functionality must allow field technicians to access and update work orders, schematics, and GIS data in areas with limited connectivity, ensuring continuity of operations in remote or hazardous locations.
A unified FSM solution is essential for streamlining operations across work order management, crew scheduling, and IoT sensor data. These functions must be consolidated into one system, reducing manual inefficiencies and ensuring teams can access accurate, up-to-date information. By integrating IoT-driven asset monitoring, the platform allows organizations to predict failures, automate service scheduling, and enhance response times, leading to increased operational efficiency and reduced downtime.
In addition, offline mobile capability ensures that workers can continue accessing job assignments, asset information, and GIS data without requiring an active internet connection. This functionality is particularly valuable for teams working in remote sites, underground infrastructure, and disaster-stricken areas where connectivity is unpredictable.
Further, field crews must never lose access to critical job assignments, asset data, or GIS mapping—even in remote, underground, or disaster-stricken locations. The FSM system should seamlessly sync updates once connectivity is restored, ensuring that no data is lost, and operations remain uninterrupted. In areas with limited connectivity, pre-downloaded high-resolution maps enable technicians to navigate complex asset networks without relying on real-time global positioning system (GPS) data.
Enable Corporation-Wide CommunicationsFSM platforms must transform how field teams work together, enabling real-time communication and expert guidance from anywhere. Achieving complete visibility and control over field operations for mission-critical operations. The platform must provide a real-time, centralized interface where managers can oversee all ongoing tasks, track workforce productivity, and monitor asset conditions in real time. This level of transparency enhances decision-making, ensures regulatory compliance, and enables organizations to optimize resource allocation (Figure 3).
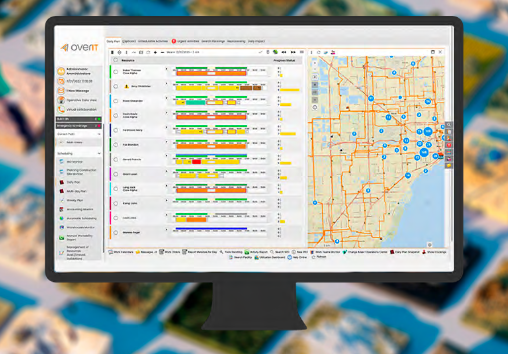
A modern FSM platform should leverage augmented reality (AR) overlays so technicians can receive hands-free, step-by-step visual instructions, improving first-time fix rates and reducing costly errors. AR-enabled safety checklists further support field personnel by guiding them through compliance protocols and mitigating potential hazards. Further, digital twin technology creates virtual representations of physical assets, allowing teams to simulate performance, predict failures, and optimize maintenance strategies.
Real-time geospatial intelligence offers field teams the visibility and precision they need to manage complex asset infrastructures. Integration with Esri, SmallWorld, and other leading GIS platforms enables asset tracking, enhances situational awareness, and improves workforce navigation—even in remote or high-risk locations. Technicians must be able to visualize infrastructure layouts, edit and update asset maps, and annotate changes directly from their mobile devices.
Navigating complex asset infrastructures requires accurate spatial data and intuitive mapping tools. Mobile GIS capabilities provide field teams with high-resolution maps and interactive navigation features that help them efficiently locate and service assets in dense or challenging environments. Whether responding to an emergency repair or performing routine maintenance, technicians should be able to rely on GIS integration to precisely guide them to the correct location, reducing service times and minimizing operational disruptions.
A key feature of any mobile GIS solution is the ability to remotely redline and edit data. This capability allows field technicians to update asset maps directly from their mobile devices. This real-time functionality ensures that infrastructure modifications, such as new installations, repairs, or hazard identifications, are immediately reflected across the organization. By eliminating the delays associated with manual data entry and processing, redlining tools improve data accuracy, streamline workflows, and enhance collaboration between field teams and back-office personnel. As-built drawings should be available in days, not months.
Avoid ERP or CRM BundlesMany organizations mistakenly believe that FSM can be managed as an additional component bundled within more extensive ERP or CRM platforms like SAP and Salesforce. However, FSM add-ons within ERP and CRM systems often struggle with real-time data processing, offline capabilities, and GIS integration. Companies in high-risk, asset-intensive, geographically dispersed industries should focus instead on purpose-built FSM platforms. This focused approach ensures that the FSM platform continuously evolves based on the specific needs of these linear asset-intensive industries. This dedication allows for deeper integration with industry-specific technologies, refined workflows, and innovative advancements tailored to the challenges faced by its customers.
A reliable approach for identifying leadership in the FSM space is to examine those companies recognized by IDC MarketScape in its FSM solutions for utilities vendor assessment or Gartner in its Magic Quadrant for Field Service Management report, two of the most respected authorities in technology evaluation.
Follow the LeaderOverIT has established itself as a leader in FSM and has a proven track record of success. With more than 300 successful implementations across more than 30 countries, the company has demonstrated its ability to deliver effective FSM solutions tailored to the needs of mission-critical industries. By partnering with utilities worldwide, OverIT has helped organizations enhance operational efficiency, improve safety, and streamline field service workflows. This extensive experience reinforces OverIT’s expertise in managing large-scale, complex infrastructure operations, focusing on reliability and long-term performance.
One of OverIT’s strongest endorsements is its track record of no failed implementations and 100% customer retention (see sidebar). OverIT’s commitment to customer-driven enhancements is evident in its update strategy, with 60% of all platform improvements directly influenced by customer recommendations through its customer advisory board. This collaborative approach ensures the platform remains highly relevant, continuously incorporating new features that address real-world operational challenges. By integrating customer insights into its development process, OverIT fosters strong, long-term partnerships with its clients, ensuring that its FSM solution remains the best choice for mission-critical industries worldwide.
Real-world deployments reliably measure the impact of FSM capabilities. The following case studies demonstrate how leading utilities have leveraged OverIT’s NextGen FSM to improve efficiency and service reliability. Enel Global Power Generation operates 1,200 renewable energy plants located in 29 countries. OverIT handles 30,000 work orders and more than 9,000 maintenance notifications annually, optimally handling work shifts with 24/7 coverage. Enel reports a 40% productivity improvement and a 75% reduction in maintenance costs after adopting OverIT’s NextGen FSM solution. Another utility serving 3.7 million customers in the western U.S. chose OverIT to replace its manual planning, scheduling, and work order management processes. OverIT enhanced its back-office efficiency with a robust scheduling optimization engine and appointment booking system. Technicians use a single mobile app to visualize assets and update GIS as needed. Field operations report increased mobile user adoption, improving safety, work quality, and execution accuracy. OverIT also provided a holistic view of assets, resources, and activities that optimized response times and improved customer satisfaction. |
—Paolo Bergamo is CEO of OverIT – Field Service Management, and René Zaldivar is senior vice president of OverIT’s North America operations. Learn more at OverIT.ai or email [email protected].
powermag