L'avenir de l'ammoniac comme carburant alternatif
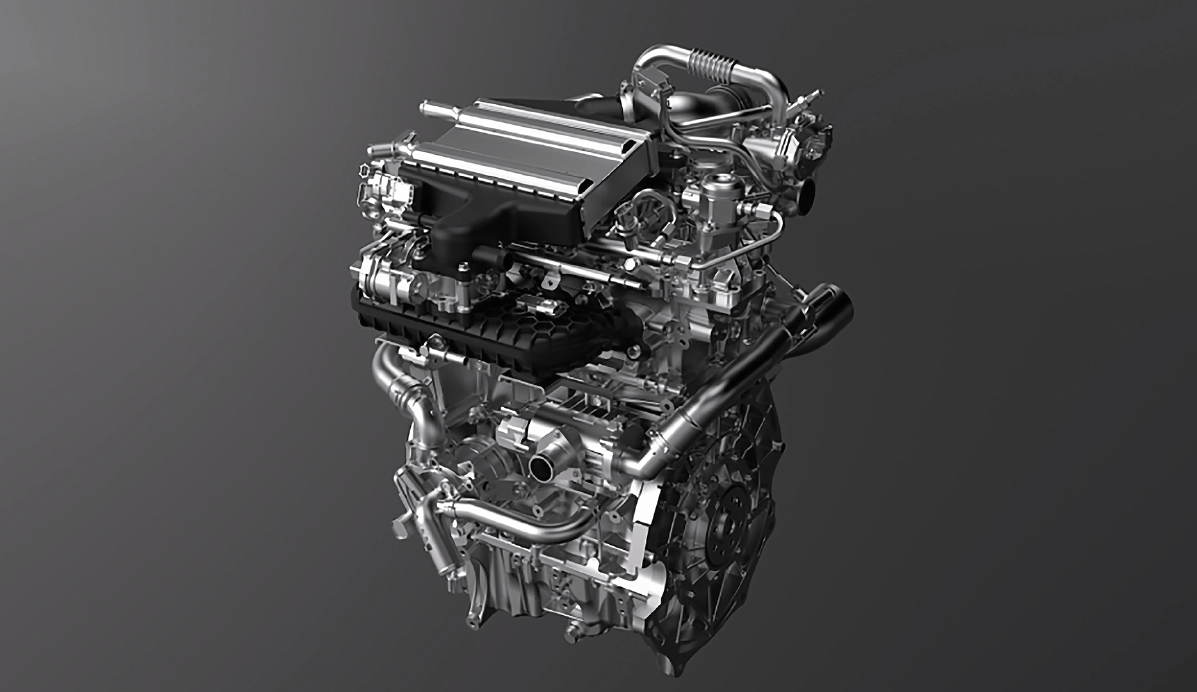
L’un des plus grands procédés chimiques créés au 20e siècle. - c'est la synthèse de l'ammoniac. La force motrice derrière le développement de ce processus était la nécessité de fournir de la nourriture à la population croissante de la Terre. La seule source d'engrais minéraux contenant de l'azote au début du 20e siècle. quelles étaient les réserves de nitrate d'ammonium au Chili. Ces réserves s’épuisaient rapidement et il semblait que la prédiction du prêtre et scientifique anglais Thomas Malthus, qui croyait que le progrès scientifique et technologique ne pourrait pas compenser les ressources naturelles limitées, pourrait se réaliser. Au début du 20e siècle. Le principal défi pour les scientifiques du monde entier est devenu le problème de la fixation chimique de l’azote. Une façon naturelle de résoudre ce problème était de lier l’azote atmosphérique sous forme d’ammoniac synthétique. Le mérite du développement d’une méthode industrielle de production d’ammoniac à partir d’azote et d’hydrogène revient à deux scientifiques allemands : Fritz Haber et Carl Bosch. F. Haber a été le premier à développer une méthode de production d'ammoniac dans des conditions de laboratoire, et K. Bosch a créé les bases techniques du processus industriel. Tous deux sont devenus lauréats du prix Nobel : F. Haber en 2019 et K. Bosch en 1931. Plus de 100 ans se sont écoulés et tous les réacteurs de synthèse d'ammoniac dans le monde sont construits conformément aux solutions technologiques développées par Carl Bosch. Actuellement, la production mondiale d’ammoniac atteint 200 millions de tonnes par an. Cela permet de fournir des engrais azotés aux principaux producteurs agricoles (Chine, Inde, USA, Russie). Le taux de croissance annuel de la production d’ammoniac au cours des dernières années n’a pas dépassé 1,5 %. Cela indique une stabilité sur le marché de l’ammoniac. Jusqu’à présent, le principal domaine d’utilisation de l’ammoniac était la production d’engrais minéraux et d’explosifs industriels. Récemment, un nouveau domaine d’utilisation de l’ammoniac comme carburant a commencé à se développer rapidement. L'ammoniac contient une grande proportion d'hydrogène et ne libère pas de dioxyde de carbone lors de sa combustion, ce qui en fait un carburant propre et respectueux de l'environnement. L’ammoniac est beaucoup plus facile à stocker et à transporter que l’hydrogène. Enfin, l’ammoniac est un carburant riche en énergie, avec un pouvoir calorifique seulement 3 fois inférieur à celui de l’essence ou du diesel.
L’analyse de la possibilité d’utiliser l’ammoniac comme carburant devrait commencer par un examen de ses caractéristiques énergétiques en comparaison avec les types traditionnels de carburants – essence, carburant diesel (DF) et gaz naturel (tableau 1).

Plusieurs caractéristiques énergétiques et thermodynamiques de l’ammoniac sont très proches de celles des carburants traditionnels. Tout d'abord, c'est la température et la pression de condensation qui permettent de stocker l'ammoniac et les carburants traditionnels à l'état liquide (sauf le gaz naturel). Tous les combustibles, y compris l'ammoniac, ont des valeurs similaires pour la température de combustion maximale (adiabatique) – de 1800 à 2030 °C. Cependant, certaines caractéristiques physiques du NH3 limitent son utilisation dans les moteurs. Ainsi, la valeur de la densité énergétique volumétrique du NH3 est significativement inférieure à celle des carburants hydrocarbonés traditionnels (tableau 1). Cela signifie que le volume de carburant (ou de réservoirs de stockage) nécessaire pour générer la même quantité d’énergie en utilisant du NH3 augmentera de 2,5 à 3 fois. De plus, le NH3 a une température d’auto-inflammation beaucoup plus élevée que les carburants traditionnels. Par conséquent, pour qu'un moteur diesel fonctionne avec de l'ammoniac, des taux de compression beaucoup plus élevés sont nécessaires - au moins 35:1 - par rapport aux valeurs utilisées lors du fonctionnement avec du carburant diesel (de 14:1 à 22:1) [1]. Cela impose des exigences accrues en matière de résistance et de résistance à la corrosion des matériaux utilisés pour fabriquer les moteurs. La vitesse de propagation de la flamme plus faible lors de la combustion de l'ammoniac peut entraîner une instabilité du processus de combustion.
En 2019-2020, les plus grands fabricants de moteurs diesel MAN Energy Solutions (Allemagne) et Wärtsilä (Finlande) ont annoncé le début du développement de moteurs diesel à deux et quatre temps fonctionnant à l'ammoniac [2]. La plus grande attention est accordée à l’utilisation de l’ammoniac comme substitut au carburant automobile dans le secteur du transport maritime. L'entreprise norvégienne Yara a annoncé la construction du premier navire marin « zéro émission » au monde fonctionnant à l'« ammoniac pur » sans utilisation de carburants hydrocarbonés (fioul ou diesel). Il est prévu que ce navire commencera à être utilisé dès 2026 pour le transport maritime d'engrais sur la route Norvège-Allemagne.
Actuellement, pour résoudre le problème de l’efficacité insuffisante de la combustion de l’ammoniac dans les moteurs diesel, celui-ci est mélangé à une petite quantité de carburant diesel ordinaire (appelé « carburant pilote »), qui est injecté dans le système de carburant et déclenche la combustion de l’ammoniac [1]. Des expériences menées en 1977 ont montré que parmi les quatre principaux carburants – méthanol, éthanol, méthane et ammoniac – l’ammoniac est le moins adapté au fonctionnement d’un moteur diesel, même dans une version bicarburant [3]. Outre des émissions importantes de NH3 incomplètement oxydé (jusqu'à 0,5 % vol.), son utilisation a entraîné le délai d'allumage le plus long, la puissance de sortie et l'efficacité les plus faibles par rapport aux autres carburants (tableau 2).

Cependant, après le début de la campagne de réduction des émissions de CO2, l'applicabilité fondamentale du schéma bicarburant ammoniac + diesel pour les moteurs diesel turbocompressés multicylindres a été démontrée. Cela n'a nécessité qu'une modification mineure du système d'admission de carburant pour accueillir la conduite d'alimentation en ammoniac, tandis que le système d'injection de carburant hydrocarboné est resté inchangé [4]. Un fonctionnement stable du moteur a été possible avec jusqu'à 95 % (en termes d'énergie) du carburant diesel remplacé par du NH3, et des économies de carburant importantes (efficacité de fonctionnement la plus élevée) ont été réalisées avec une teneur en ammoniac de 40 à 60 % dans le carburant. À des teneurs en NH3 inférieures à 60 %, une réduction significative des émissions de NOx a été observée, que les auteurs ont attribuée à une réduction de la température de la flamme. Cependant, cela a entraîné une réduction de l’exhaustivité de la combustion du carburant diesel, qui s’est manifestée par une augmentation des émissions d’hydrocarbures. Des études plus détaillées menées ultérieurement [5] ont montré que lorsque la teneur en ammoniac était supérieure à 60 %, le délai d’allumage du carburant augmentait. Dans le même temps, lorsque la proportion de carburant diesel augmente au-dessus de 60 % lorsque le moteur fonctionne à puissance constante, la composition du mélange ammoniac-air dans le moteur peut atteindre les limites explosives, et une diminution de la température de combustion réduit l'efficacité de la combustion du carburant dans son ensemble. Un autre problème important qui doit être résolu lors de l’utilisation de l’ammoniac dans les systèmes à double combustible est lié au système d’alimentation de la chambre de combustion. Ainsi, l'ammoniac peut être injecté dans la soupape d'admission (ce qui produit des mélanges homogènes de carburant et d'air) ou introduit directement dans le cylindre sous forme liquide. Cette dernière option est préférable, car elle permet de doser l'ammoniac directement à partir des réservoirs de stockage sous forme liquide (à une pression d'environ 17 atm.) sans évaporation préalable. En dosant le liquide, la pression dans la chambre de combustion peut être considérablement augmentée. Cependant, en raison de la valeur élevée de la pression de vapeur saturée et de la forte dépendance de la pression de vapeur saturée à la température, l'ammoniac se caractérise par une ébullition et une évaporation instantanées lorsque la pression diminue. Cet effet est particulièrement prononcé dans les tuyères d'admission et modifie considérablement les schémas de formation des mélanges gaz-air, conduisant dans certains cas à un mauvais mélange du carburant avec l'air et à une pénétration plus profonde du liquide dans le moteur, jusqu'à mouiller les parois [6]. De plus, avec l’injection de liquide, une forte diminution de la température lors de l’évaporation de l’ammoniac réduit considérablement la stabilité de la flamme. Pour réduire cet effet négatif, un préchauffage et une turbulence du flux d’air fourni à la chambre de combustion sont proposés. En général, des recherches supplémentaires sont nécessaires dans ce domaine pour comprendre les spécificités des processus de formation des mélanges ammoniac-air et leur combustion dans les moteurs à combustion interne, ainsi que le développement de modes d'alimentation en carburant optimaux.
Chez MAN Energy Solutions, le système de dosage d'ammoniac est basé sur des systèmes similaires développés précédemment pour les gaz de pétrole liquéfiés et le méthanol. Il a été annoncé que si les tests pilotes sont réalisés avec succès en 2023, le premier moteur à deux temps fonctionnant à l'ammoniac sera installé sur un navire industriel en 2024 [7]. Wärtsilä Corporation a annoncé fin 2023 qu'elle avait lancé le premier moteur industriel à quatre temps fonctionnant avec un mélange de diesel et d'ammoniac [8], et début 2024 qu'elle disposait d'un système d'alimentation en ammoniac pouvant fonctionner avec des matières premières liquides et gazeuses [9]. Ils devraient être installés en 2025 sur des méthaniers de taille moyenne spécialement construits à cet effet dans les chantiers navals Hyundai Mipo en Corée du Sud pour EXMAR LPG.
La possibilité d’utiliser l’ammoniac dans le transport motorisé est également activement étudiée. Ces travaux sont réalisés dans deux directions. Tout d’abord, l’ammoniac est utilisé comme vecteur énergétique pour les piles à combustible qui alimentent le moteur électrique d’une voiture. L’ammoniac peut également être utilisé comme substitut direct de l’essence ou du diesel dans un moteur à combustion interne. Le premier moteur de ce type a déjà été démontré en 2023 par l’alliance de GAC (Chine) et Toyota (Japon) [10]. Cependant, le principal domaine d’utilisation de l’ammoniac dans le transport motorisé est celui des technologies basées sur l’utilisation de piles à combustible à ammoniac comme sources d’énergie. Tout d’abord, il s’agit d’une méthode plus efficace d’extraction d’énergie à partir de l’ammoniac, caractérisée par des émissions plus faibles de NH3 et d’oxydes d’azote, ainsi que par un faible bruit [2]. Les piles à combustible elles-mêmes occupent beaucoup moins d’espace que les moteurs à combustion interne. Les piles à combustible à membrane échangeuse de protons (PEMFC) et les piles à combustible à oxyde solide (SOFC) sont les plus prometteuses [11]. Des prototypes de PEMFC (mais sans utiliser d’ammoniac comme source de H2) sont déjà utilisés dans les transports terrestres. Les équipements auxiliaires nécessaires à leur fonctionnement (systèmes de refroidissement, ventilation, alimentation en carburant, etc.) sont à peu près les mêmes que pour un moteur conventionnel. Le principal problème lors du passage à l’ammoniac dans les piles à combustible PEMFC est que la pureté de H2 ne doit pas être inférieure à > 99,5 % avec une absence totale de traces de NH3. Les piles à combustible SOFC peuvent utiliser l'ammoniac comme combustible sans décomposition préalable ni émission de H2, ce qui permet d'atteindre des valeurs de puissance plus élevées par unité de poids de combustible. Cependant, les piles à combustible SOFC nécessitent un système de stockage d’énergie pour compenser les processus lents pendant les conditions transitoires et leur fournir de l’énergie pendant les conditions de démarrage. L’utilisation de l’ammoniac comme vecteur énergétique ne se limite pas au transport. Des recherches intensives sont menées pour remplacer les carburants hydrocarbonés par de l’ammoniac dans les turbines à gaz. Afin de réduire l’empreinte carbone dans l’ingénierie thermique, un procédé de combustion compatible du charbon et de l’ammoniac est en cours de développement.
La plupart des publications sur l’utilisation de l’ammoniac comme combustible et comme énergie sont principalement de nature promotionnelle et se limitent, au mieux, à évaluer la réduction des émissions de dioxyde de carbone. Les données expérimentales sur la teneur d’autres composés dans les gaz d’échappement des moteurs à combustion interne ne sont généralement pas fournies. Cependant, lors de la combustion d'ammoniac, en même temps que d'azote respectueux de l'environnement, diverses formes d'oxydes d'azote (NO, NO2, N2O) peuvent se former :
2NH3 + 3/2O2 = N2+ 3H2O + 634 kJ/mol (1)2NH3 + 2O2 = N2O + 3H2O + 552 kJ/mol (2)2NH3 + 5/2O2 = 2NO + 3H2O + 453 kJ/mol (3)
2NO + O2 = 2NO2–113 kJ/mol (4)
Leur teneur dans les produits de combustion peut atteindre 0,28% vol. De plus, en raison de la faible efficacité de combustion de l'ammoniac, sa concentration résiduelle dans les gaz d'échappement, même dans des conditions de combustion optimales, est de 0,1 à 0,3 % vol. [12]. Même à de faibles concentrations dans l'air (0,0005–0,005 % vol.), le NH3 provoque une irritation des yeux et des voies respiratoires, et à une teneur d'environ 1 % vol. la mort survient instantanément. Les émissions d’oxydes d’azote contribuent à la formation de smog photochimique et de pluies acides, ainsi qu’à la décomposition de la couche d’ozone. Une concentration de NO2, formée à partir de NO à température ambiante, supérieure à 0,02 % vol. est considéré comme mortel. L'augmentation de l'efficacité de la combustion du NH3 et la réduction des émissions de NO et NO2 sont obtenues en préchauffant le carburant, ainsi qu'en augmentant en plus la pression dans la chambre de combustion (cette dernière est déjà plus élevée que lors du travail avec du carburant diesel). Une bonne alternative aux augmentations de pression ou de température dangereuses et coûteuses peut être l'utilisation d'une technologie industrielle pour réduire les émissions d'oxydes d'azote en fonction de leur réduction catalytique sélective avec de l'ammoniac (SCR NH3) en azote et en eau sur la base des réactions suivantes :
6NO + 4NH3 → 5 N2 + 6H2O + 1095 kJ/mol (5)4NO + 4NH3 + O2 → 4N2 + 6H2O + 1629 kJ/mol (6)6NO2 + 8NH3 → 7N2 + 12H2O + 2737 kJ/mol (7)
2NO2 + 4NH3 + O2 → 3 N2 + 6H2O + 1335 kJ/mol (8)
Ces dernières années, cette technologie catalytique a été adaptée au transport de marchandises et au transport maritime, où des produits à base de fractions pétrolières à point d'ébullition élevé avec une teneur relativement élevée en composés contenant de l'azote sont utilisés comme carburant [13]. L'activité corrosive élevée de l'ammoniac impose des exigences particulières aux matériaux des moteurs et des systèmes d'alimentation en carburant, ainsi qu'à sa pureté. Ainsi, tout alliage contenant du cuivre et du nickel dont la teneur en ce dernier est supérieure à 6 % ne peut être utilisé dans les systèmes de carburant, les récipients destinés à son stockage ainsi que dans ses conduites d'alimentation. Seul le Téflon convient pour les joints et l’isolation dans de tels systèmes. En raison de la fissuration accélérée par corrosion sous contrainte de l'acier, en particulier à des températures élevées, en présence d'humidité et d'air, leur teneur maximale en ammoniac ne doit pas dépasser 0,1 % en poids. et plusieurs millionièmes. Des technologies spéciales sont donc nécessaires pour garantir la pureté requise du carburant.
Quels problèmes peuvent être identifiés dans la transition des transports vers le carburant à l’ammoniac ? Il s’agit tout d’abord : a) de problèmes de corrosion lorsque les éléments du moteur entrent en contact avec l’ammoniac ; b) forte toxicité de l’ammoniac ; c) la capacité énergétique spécifique relativement faible de l’ammoniac en tant que combustible ; d) formation d'oxydes d'azote à partir de l'ammoniac lors de sa combustion. Il convient de prêter attention aux perspectives techniques et économiques de l’ammoniac en tant que carburant. Le pouvoir calorifique inférieur de l’ammoniac par rapport au carburant diesel est presque compensé par son faible coût en Russie. Cela signifie que l’ammoniac est déjà un carburant compétitif en termes de coûts. Dans les procédés existants de synthèse d’ammoniac à partir de gaz naturel, du dioxyde de carbone se forme inévitablement – environ 2,5 tonnes de CO2 pour 1 tonne d’ammoniac. L’élimination sur site du CO2 concentré est nettement moins coûteuse et technologiquement plus simple que la résolution de ce problème pour un seul véhicule à carburant hydrocarboné. Ainsi, l’utilisation de l’ammoniac dans les processus technologiques ouvre des possibilités de création de transports sans empreinte carbone. L’utilisation commerciale de l’ammoniac à cette fin devrait commencer entre 2035 et 2037. D’ici 2050, le transport maritime devrait utiliser principalement du gaz naturel liquéfié (65 à 70 %) et de l’ammoniac (20 à 25 %). La part du fioul à faible teneur en soufre ne sera que de 10 %. Cela nécessitera de doubler la production mondiale d’ammoniac d’ici 2050, pour atteindre 400 millions de tonnes par an.
L’utilisation de l’ammoniac dans le transport maritime et automobile donnera inévitablement une impulsion au développement des moteurs à combustion interne. Les moteurs à ammoniac peuvent être très différents des moteurs à essence ou diesel. Il est possible que l’ammoniac ne soit pas un monocarburant et qu’il nécessite l’introduction d’additifs spéciaux (similaires aux additifs augmentant l’indice d’octane). La nécessité d’augmenter la capacité de production d’ammoniac stimule les progrès dans les nouvelles technologies pour sa synthèse. Cela conduira à une augmentation de la recherche scientifique dans le domaine des procédés catalytiques associés à la synthèse de l'ammoniac et au développement industriel des résultats de ces travaux.
Les travaux ont été réalisés avec le soutien financier du Ministère des Sciences et de l'Enseignement Supérieur de la Fédération de Russie dans le cadre de la mission d'État de l'Institut de Catalyse SB RAS (projet FWUR-2024-37).
energypolicy