This is how a plastic bottle is reborn after the recycling cycle
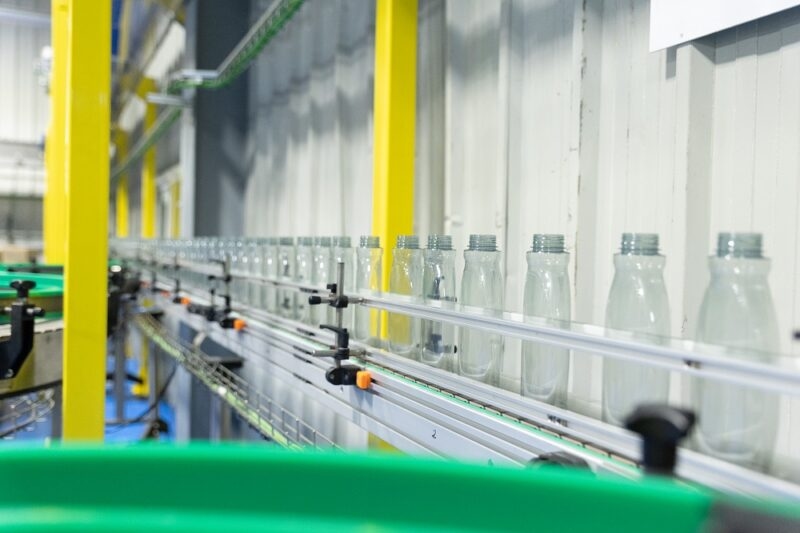
Karina Godoy
Madrid (EFEverde).- In Spain, nearly 1.5 million tons of household waste will be recycled in 2024, of which 589,000 tons are plastic containers, according to Ecoembes. Private sector initiatives, such as Plastipak Iberia, are implementing production systems to give the material a second life. To understand the process of how one bottle is transformed into another, the company opened the doors of its processing and recycling plant.
"It's important that plastic be used sensibly, and that when it's discarded, it's deposited in the appropriate place for proper reuse," emphasizes Antonio Molina, technical director of Plastipak Iberia, as he begins the tour of the PET preform and packaging factory located in Casarrubios del Monte, Toledo.
Throughout 2024, each citizen deposited 20.1 kg of paper and cardboard packaging in blue containers and 21.3 kg of waste in yellow containers, which contain plastic, metal, cartons, and wood, according to the Ecoembes report. Meanwhile, 33.4% of this waste was not packaging and, therefore, should not have ended up in that container.
SegregationThe material used to make a new bottle comes primarily from containers deposited in yellow containers, which are separated and sorted before being compacted into what is known as a post-consumer "baled."
The containers are then shredded and disinfected. The resulting material is called post-consumer PET flake, which enters Plastipak's recycling line for processing into rPET. The raw material is purchased from various suppliers.
TransformationAt the Plastipak Iberia factory, the production process begins with the received flakes. They are again sorted and decontaminated, which is repeated in several subsequent processes. Once processed in the machine, the product appears in the form of spaghetti, which is then cut and shaped into pellets.

The product then moves on to the injection process, where the PET granules are compressed and heated for melting.
The molten material is forced into the cavities of the closed mold by hydraulic pressure. According to technicians, the molds are typically highly complex hot-runner molds; they are designed to contain a cold water cooling system for cooling, ensuring solidification, demolding, and the glassy appearance characteristic of PET.
There is a dedicated cooling zone for cooling the molds on each injection line. When the mold is opened, a robotic arm extracts all the preforms at once and transfers them onto a "hedgehog" or a conveyor belt, where they finish cooling before being inserted into the boxes.
The molds have a variable number of cavities, depending on the case, so that in one injection, multiple preforms are obtained, which are like small bottles with the closure or thread area already finished.

The final stage is the stretch-blow process, which involves the introduction of high-pressure air until the final container shapes are obtained. In most cases, the preforms are delivered to customers, which facilitates transport, and finally, the blow molding is performed directly at their respective facilities.
The plant's recycling capacity, according to technicians, is 20,000 tons per year.
This is Plastipak's fifth recycling facility, which has other plants in the US, France, Luxembourg, and the UK.
In total, the annual production capacity is more than 150,000 tons, explains Vicente Montojo, Regional Director for Iberia and Morocco.
During the visit to the plant, Luis Cediel, director of the Spanish Association of Plastics Manufacturers (ANAIP), called for more balanced regulations regarding the Tax on Non-Reusable Plastic Packaging, which has been levied at €0.45/kg of non-recycled virgin plastic in non-reusable packaging since 2023.
Cediel indicated that there are competitive disadvantages compared to other European countries that do not apply the tax. Spain is the only country in the European Union that does.
He noted that, in the two years since the tax was introduced, imports have grown by €1.5 billion and that unfair competition exists due to a lack of market surveillance and enforcement.
Among ANAIP initiatives, he cited the “Spanish and Sustainable Plastics Industry Brand” on evidence of compliance with criteria and parameters.
Also, the MORE platform for the annual recording of the amount of recycled material used in processes. Standardization and Certification, in addition to the Operation Clean Sweep program, an initiative to prevent the release of plastic particles into the environment.
And if you haven't received it yet, you can join our mailing list here.
efeverde