A Clear Path to a Sustainable Facility
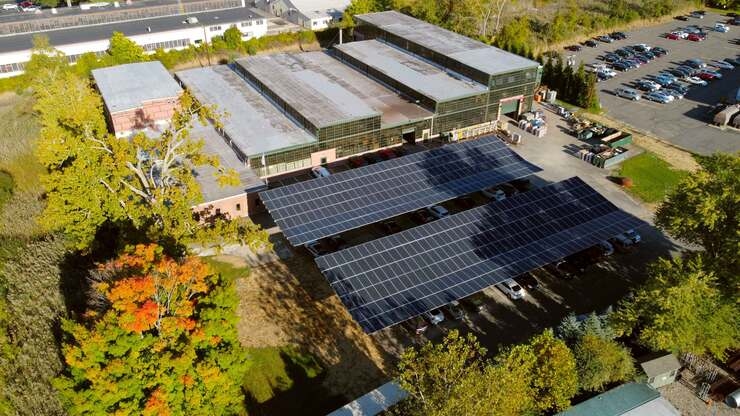
Since the industrial revolution, manufacturers and other large industrial operations have often been labeled as environmental polluters. However, this traditional viewpoint is rapidly transforming thanks to the push toward sustainability. Today, there is an undeniable shift. Manufacturers and large facilities alike are seeking to significantly reduce their carbon emissions to align with global and national sustainability goals.
Internationally, treaties such as the Paris Agreement have set ambitious targets for carbon reduction, aiming to limit global warming. These global commitments are often mirrored by national strategies and regulations designed to reduce greenhouse gas emissions and transition toward renewable energy sources. This kind of external pressure may put up hurdles, but it is also a catalyst for innovation, driving industries to take a closer look at their operations.
A Sustainability ShiftAt the forefront of the sustainability shift is engineering innovation, which is moving toward a greener, cleaner, and more sustainable future for manufacturing. In addition to lean operational processes that eliminate waste and material advancements that reduce energy use, manufacturers are also rethinking energy sources. The transition from fossil fuels to renewable energy sources like solar, wind, and bioenergy is a critical component of decarbonization strategies.
As more companies make this shift, the benefits of decarbonization are becoming clearer, such as enhanced operational efficiency, reduced operational costs, and increased competitiveness. Advanced energy management systems, for instance, not only reduce energy consumption but also optimize the production processes. Sustainable practices reduce waste and lower maintenance costs, since renewable resources and energy-efficient equipment tend to be more durable and less resource-intensive. Additionally, renewable energy has both lower and more stable prices compared to the volatile fossil fuel market.
Sustainable practices also offer businesses a competitive angle. There is growing preference for products manufactured in an environmentally friendly way. Companies that can demonstrate a commitment to sustainability often have a stronger brand reputation, increased customer loyalty, and access to new markets, particularly in areas where environmental sustainability is highly valued.
A Path to DecarbonizationThis article aims to provide a path to decarbonization for manufacturers and other large industrial organizations. We explore the decarbonization journey of a manufacturing facility as a case study for how others can successfully navigate that path. This manufacturer’s journey from traditional energy reliance to a diverse energy portfolio—including the conversion of their boiler room to Bio-Residual Oil (BRO 500) and the installation of 209-kW solar panels—illustrates the practical realities and challenges of this type of transition. Additionally, their choice to maintain operational flexibility by retaining the ability to fire natural gas and fuel oil, highlights the reality that no single energy source is the perfect answer to any large facility’s needs.
Any decarbonization journey is complex. It requires strategic planning, technological advancement, and a commitment to move forward. We will examine the preparation, planning, and implementation phases of this transformation, highlighting the challenges encountered and the innovative solutions applied. The story is not just about the adoption of green technologies; it shows the critical role of engineering decisions, economic considerations, existing infrastructure, and local regulations in shaping a sustainable future.
It is important to note that the path to decarbonization is unique for each facility. This article aims to offer insights and inspiration for other manufacturing and industrial facilities that are motivated to undertake their own journey toward sustainability.
Case studyThis case study explores the sustainability journey of an over 100-year-old manufacturing organization with a rich history. Their facility, located in an urban industrial center, spans 150,000 square feet and employs approximately 120 people. This manufacturer produces advanced industrial equipment, with a focus on sustainability and lowering emissions.
Before embarking on its sustainability journey, the facility relied heavily on conventional energy sources to power and heat its operations—with two 125-hp unit steam generators. Originally, the facility was heated using No. 6 fuel oil, which needs to be heated with multiple heating devices for burning and handling. This less sustainable fuel oil was discontinued in the early 2000s and replaced by No. 2 oil. The company was able to keep most of its existing equipment at that time, simply bypassing the heaters for better efficiency.
Catalyst for ChangeEvery organization needs a catalyst for change—whether that’s a shift in regulations, a company culture shift, or economic reasons. The catalyst for this organization stemmed from a mismatch between its outdated infrastructure on one side, and its sustainability-focused solutions and products on the other. The company is a recognized authority on progressive environmental regulations and needed its facility to align with the company’s environmental advocacy.
Additionally, the organization wanted to attract a younger, more environmentally conscious workforce, and it had become clear that its facility wasn’t truly resonating with either their recruits or their increasingly environmentally conscious clientele.
The journey started out with several expectations, including:
- To substantially reduce the facility’s carbon footprint, contributing to global efforts against climate change.
- To reduce reliance on fossil fuels to lower energy costs in the long run, despite initial investment in renewable technologies.
- To attract innovative partnerships, new client segments, and talented employees who are drawn to companies with a strong environmental ethos.
The shift toward sustainability in manufacturing facilities can be perceived as daunting due to the planning and preparation required, but managed in phases, and with the right team of leaders, it can become much more manageable.
Choosing the Team. In the case study, the organization looked to its “Strategic Initiatives Team” to guide this extensive project. This is a group of employees from various parts of the organization who seek out and plan long-term initiatives. This planning team focused on long-term benefits, rather than short-term cost-savings, with a keen eye toward energy efficiency.
Preparation. The Strategic Initiatives Team made several pre-emptive updates to the facility in the lead up to their sustainable energy transition. For example, all steam piping was insulated to minimize heat loss, and lighting systems were upgraded to LED (light-emitting diode) technology (Figure 1) to reduce electricity consumption. These steps not only enhanced the operational efficiency of the facility but also aligned with the broader goals of energy conservation and sustainability. Additionally, this group led an office refresh that included energy efficiency at all steps of the planning, including design elements and workflow improvements.
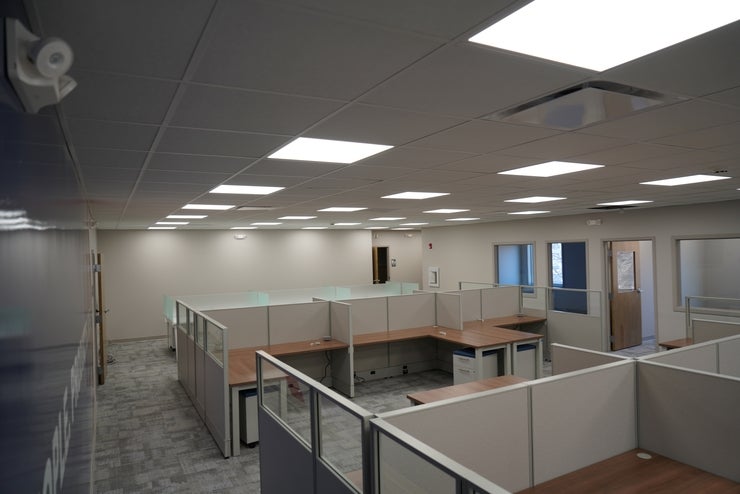
Initial Decisions. A major business strategy of the case study organization is to promote the use of non-fossil liquid fuels. So, one of its first decisions was to put these fuels at the forefront. It made sense for the company not only for environmental and cost efficiency reasons, but also as proof of concept for their own products.
The company also made a key decision to retain the ability to use natural gas and fuel oil, allowing operational flexibility and reliability. It is vital that energy solutions be versatile and allow a combination of fuel sources and options to be the most stable and efficient in the long term. No single energy source can meet all the needs of a large facility that must be able to handle urgent energy needs, fluctuating market conditions, or supply chain issues. A balanced and flexible approach to the company’s energy strategy was the best decision overall.
Finally, solar energy was identified as a critical component of this facility’s sustainable energy strategy. This decision was partly financial, as it would save on energy costs, but it also helped the community with grid support. Solar plays an important role in overall grid support because the highest energy consumption occurs on hot days in the afternoon as power customers run their air conditioners.
Unfortunately, during the initial planning phase, the organization discovered that its roof was not capable of supporting the solar panel load, so the decision was made to install solar carports. While this decision added upfront costs, as we’ll discuss later, there were additional benefits to this approach.
Proper preparation, planning, and decision-making is essential to a successful sustainability journey. But it doesn’t need to be exhaustive. Once you have the major decisions out of the way, it’s time to move into the implementation phase.
Implementation PhaseHere’s where the rubber meets the road in this sustainability journey case study. This phase of the project demonstrates the practical challenges and innovative solutions that often accompany the transition to renewable energy sources.
Bio-Residual Oil Transition. In 2018, the company partnered with an international manufacturer of lower-carbon fuels to test its Bio-Residual Oil (BRO) in a large facility. This oil is produced from recycled fats and oils such as used cooking oil, distillers corn oil, animal fat, and other vegetable oils. It burns cleanly and produces less particulates than other fuel sources. BRO provides about a 90% reduction on particulate matter emissions compared to No. 6 or No. 5 fuel oil. This is similar to that of No. 2 fuel oil, making facility conversions from light fuel oil to BRO extremely accessible and sustainable. In addition, pricing of BRO is very low compared to No. 2.
Like No. 6 oil, BRO needs to be maintained at elevated temperatures for storage, handling, and burning. The organization was able to reinstall all the existing heaters previously used for No. 6 oil, and the existing pump set. The controls used for the trial were the BurnerMate Universal parallel position controller with an O2 analyzer for the Advanced Performance Inject-Aire (API) low-NOx burner, and a FlexFit Linkageless controller on the BHE rotary cup burner—a legacy product that is still supported in many boiler rooms, even where the rotary cup burner is over 70 years old.
The temperature maintained by the pump set heaters for BRO was 100F with 50 psig discharge pressure. The hot water heater installed on the boiler raised the temperature to 150F, and the electric trim heater mounted on the burners were set to raise the temperature up to 170F.
The initial delivery of 5,000 gallons of BRO was successfully implemented (Figure 2). The combustion and fuel handling of the BRO fuel was similar to that of No. 6 fuel oil. The ignition of BRO was also relatively simple and similar to that of light oil with some minor adjustments, which are typical when switching fuels. NOx levels on the BRO were lower than that of No. 6 fuel oil.
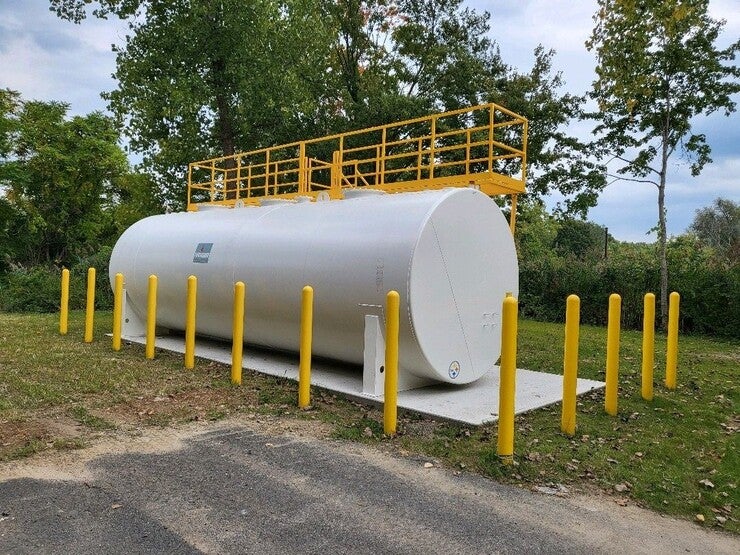
Challenges in Switching to BRO. Like No. 6 or No. 4 fuel oils, the use of BRO requires scheduled routine maintenance on the fuel-handling equipment, especially equipment at the farthest end of the delivery on the burner side. To prevent oil gun sprayer tips from getting clogged in the API burner, a 100-mesh strainer was installed. However, because of the small orifice on the oil gun, it had to be cleaned weekly to remove any potential deposits of solids that might have found their way through the strainer. Due to this consistent maintenance, to reduce downtime it was necessary to acquire a secondary oil gun to use when the first oil gun was being serviced.
The rotary cup (RC) burner does not use an atomized air oil gun. However, like the API, the RC burner needs to have scheduled maintenance to clean out any solids that might have made their way into the RC integral pump. This is no different than the typical maintenance on heavy oils such as No. 6 and No. 4.
Results. Upon the successful test-run implementation of BRO fuel in the facility, the company continued to use BRO as their main fuel. This change (Figure 3) saved the organization an average of $20,000/year while also reducing fossil fuel carbon emissions.
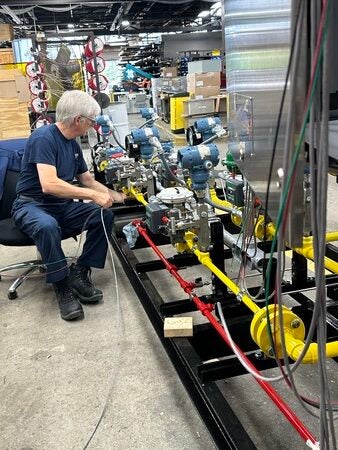
Let’s take a closer look at the steps and hurdles encountered during the solar panel installation:
Ground Preparation and Infrastructure Setup. The process began with land survey crews marking the ground to outline where concrete pillars would be installed. Precision was crucial to ensure the stability and alignment of the solar panel structures. Once the markings were complete, underground electrical runs were laid out for connecting the solar panels to the facility’s power grid efficiently and safely.
Following the electrical groundwork, concrete was poured to form the foundation for the metal frames that would support the solar panels. After those foundations had set, metal frames were erected on the pillars to support the solar panels and orient them toward the sun for maximum energy capture. The installation and wiring of the panels followed to integrate them seamlessly into the existing power infrastructure.
Challenges to the Installation. Two challenges came out of this installation process. One, due to the nature of construction using an existing parking area, the facility needed to arrange temporary offsite parking for employees. This was a minor inconvenience that was easily remedied.
The second challenge unexpectedly arose during the winter following installation. Previously, the snowplows would remove snow and the little leftover would melt and evaporate with sun exposure. However, after the build, accumulated snow on the solar panels would melt, flowing into the gutters, only to refreeze on the shaded pavement below the panels, creating hazardous icy conditions.
To resolve this, the facility had to install a comprehensive drainage system that channeled the melted snow from the gutters under the pavement to a specially constructed drainage trench. This solution not only alleviated the refreezing issue but also demonstrated the company’s commitment to safety and efficiency.
Results. The solar carport ended up providing multiple benefits (Figure 4). Electricity from the solar panels powers the offices and factory while any excess electricity is funneled back to the city to support the community’s energy needs. It also provides employees with year-round covered parking, enhancing the workplace environment. It has generated approximately 564,000 kWh of energy to date.
The decarbonization journey of this manufacturing facility serves as a compelling case study for other industrial organizations aiming to embark on their own sustainability initiatives. The challenges faced and solutions implemented provide valuable insight into the complexities and rewards of transitioning to renewable energy sources.
This case study highlights the importance of strategic planning, innovative engineering solutions, and a commitment to sustainability. The facility’s success in reducing carbon emissions, lowering energy costs, and enhancing operational efficiency illustrates the potential benefits of decarbonization.
Manufacturers and industrial facilities are encouraged to consider the holistic approach taken by this case study facility. By integrating renewable energy sources, maintaining operational flexibility, and prioritizing long-term benefits, other facilities can achieve similar success in their sustainability journeys.
—Gustavo Sanclemente is the combustion engineering/research and development (R&D) manager for Preferred Utilities, specializing in projects using renewable fuels.
powermag