Solar and Steel Offer Resilience Against Breakage, Tariffs, Supply Chain Woes
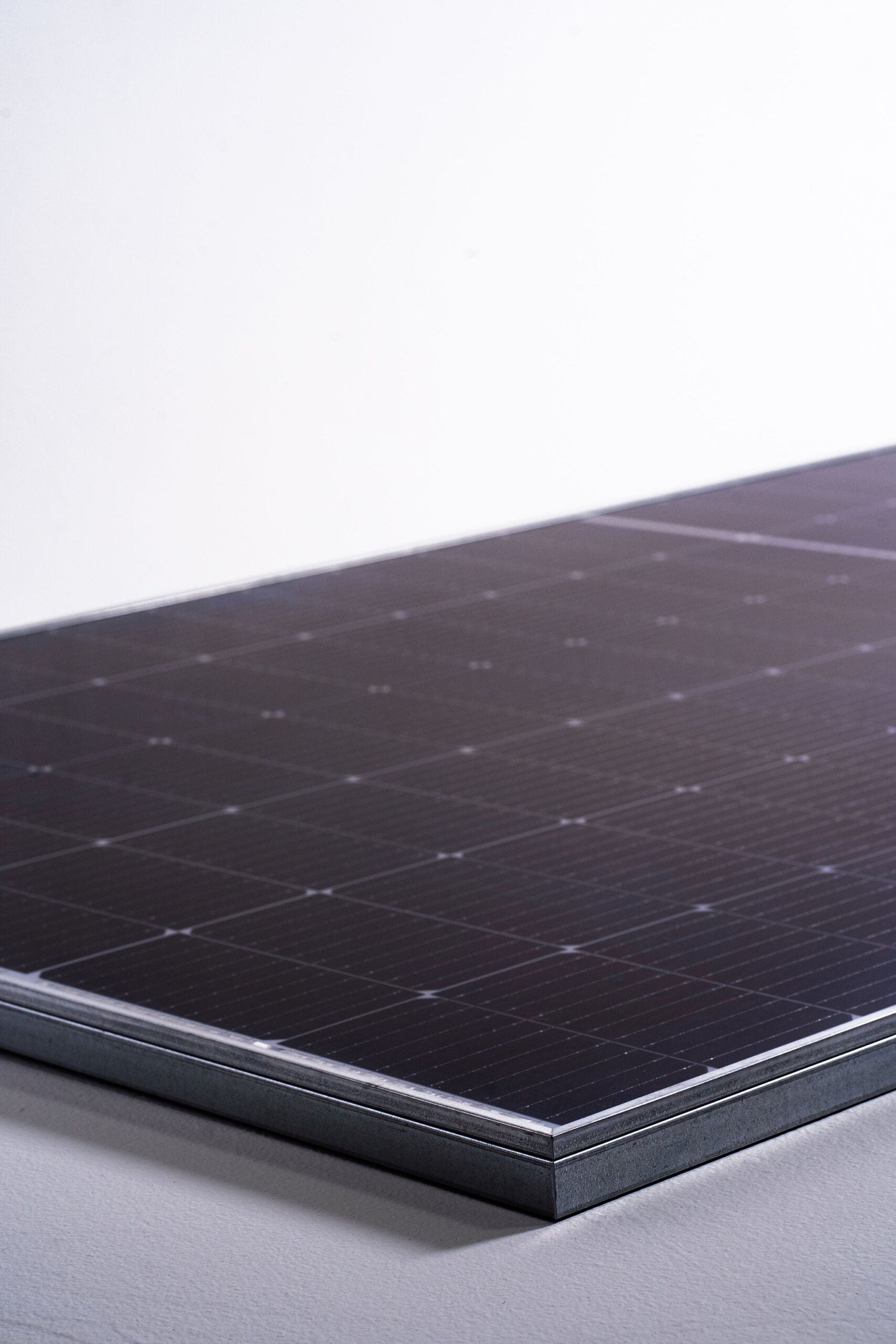
The commercial solar industry, now more than 50 years old, is facing a pivotal moment. Years of rapid growth—driven by exponentially falling costs and rising demand—are running up against global supply chain instability, geopolitical tensions, and structural vulnerabilities in the latest module designs.
Recently imposed tariffs, particularly on Chinese and Southeast Asian imports, have injected new uncertainty into the market. Supply bottlenecks, shipping delays, and increasing costs have only intensified concerns. These disruptions have prompted solar stakeholders to reevaluate every element in the photovoltaic (PV) value chain—including aluminum solar module frames.
COMMENTARY
Frames have come into focus because over the past half-decade or so, solar modules have increased in area while their structural components, such as glass thickness and frame height, have been reduced. This has led to a mechanical weakening of PV modules, as shown in both laboratory testing and in-field failures. Larger panels, often built with thinner glass and less aluminum in the module frame to cut costs, are more prone to breakage during shipping, installation, and extreme weather events. Frames are also a significant cost element in solar modules. Depending on which source is cited, frames account for approximately 15% of solar module costs.
When combined with the other risk factors, the result is an industry in need of better frame material than aluminum. The answer can be found right here at home: steel. The strength of steel mitigates the breakage problem. Its abundance solves the supply problem. And U.S.-based steel production eliminates tariff, duty, and impoundment concerns–while also boosting domestic content value to reduce project costs.
Breakage Is a Growing ProblemAccording to a recent report from the International Energy Agency’s Photovoltaic Power Systems program (IEA PVPS), the high breakage rate of thin glass used in today’s modules is a significant yet under-recognized reliability issue. As the industry shifts toward thinner module glass and reduced frame height and thickness to reduce weight and cost, field data suggests that these weaker materials are more prone to failure. The report cites alarming figures, including instances where up to 50% of modules using 2mm glass suffered breakage within nine months of deployment. Despite this growing concern, current testing and quality assurance programs fall short of addressing the specific vulnerabilities of thin glass in PV applications.
The IEA PVPS report highlights an absence of standardized tests for compressive stress or glass durability tailored to thin-glass PV modules. Compounding the issue is the lack of protocols for evaluating the delivered quality of thin glass, leaving developers and manufacturers exposed to potential reliability and financial underperformance risks. The report suggests that the trend toward larger modules with slimmer frames may be exacerbating the problem by increasing mechanical stress on the glass.
To mitigate these risks, the report calls for urgent development of new testing methodologies and quality control standards specific to thin-glass PV modules.
The National Renewable Energy Laboratory (NREL) reached similar conclusions, which were detailed in a paper assessing the impacts of module design on glass vulnerability, entitled “Tough Break: Many Factors Make Glass Breakage More Likely.” The growing size of modules was seen as an influential factor on breakage; when loaded with wind or snow, a bigger module has to support a greater load. This can be intensified by the nature of the module mounting. With racking structures being cost-optimized, modules are often supported at only a few points close to the center of module frames, causing high stresses through the glass and frames.
Superior Frame Strength Enables Better PV Plant DesignSteel frames represent a critical opportunity for greater innovation and performance in the solar industry. Steel performs significantly better than aluminum, leading to improved module performance specifications and safety margins, especially with the new larger modules. In conjunction with solar tracker mounts (also typically made of steel), the added frame strength boosts wind ratings and can save money on tracker mount costs.
The graphic below shows how solar modules have evolved over the past decade:
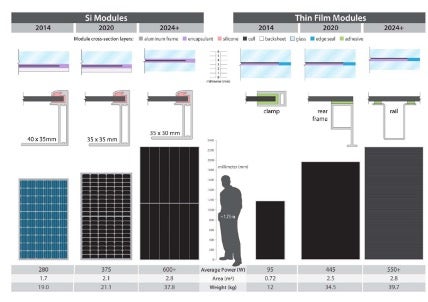
At the same time, industry testing standards have not kept pace with the growth in module sizes (see Figure 2). The result is a higher failure rate in the field both when modules are subjected to extreme weather conditions, such as high wind speeds and snowfall, and even under average daily loading conditions.
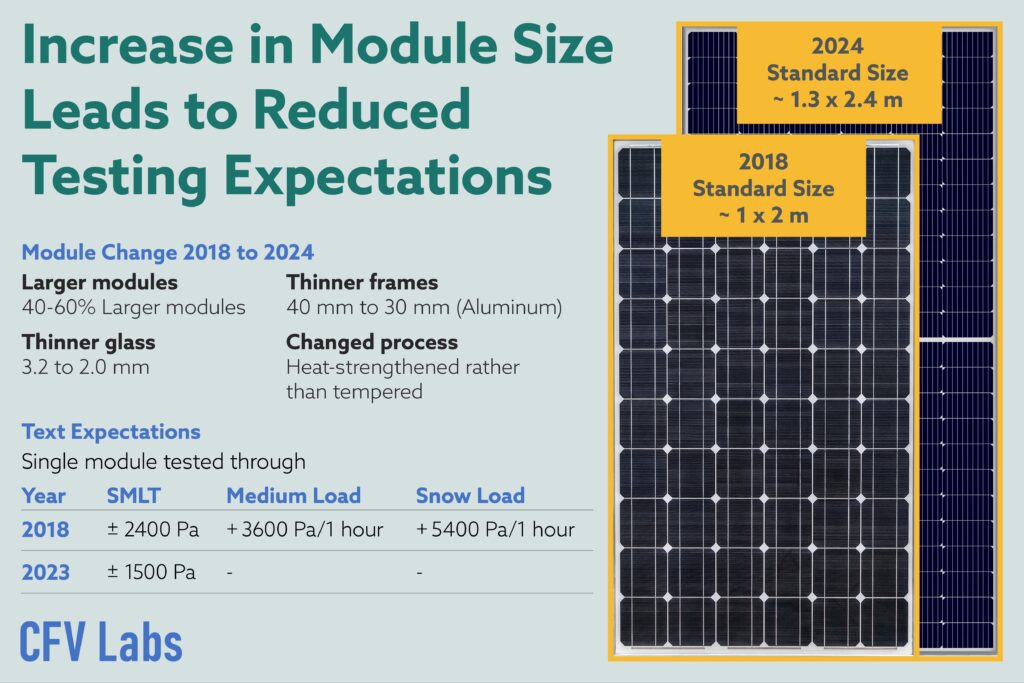
Given the need for improved performance, especially for utility-scale systems, steel frames can meet those expectations with fewer system or PV plant design compromises. Additionally, roll-formed steel frames—an innovation pioneered by Origami Solar and its partners—enable innovative frame profiles that are unachievable with aluminum extrusions. Steel frames also help developers meet new, more stringent building codes and environmental demands.
In addition to greater structural integrity, steel frames offer excellent durability to ensure industry-standard operating life. High-performance corrosion coatings, validated across the construction and automotive industries over the past 25 years, vastly outperform galvanized steel and provide a lifetime of corrosion protection for solar modules and projects.
Stronger, Cheaper, Cleaner, DomesticSteel is not only significantly stronger than aluminum, it’s also cheaper, more abundant, and made in the U.S. Domestic steel is less expensive than U.S.-produced aluminum, which commands a significant price premium due to limited domestic production. Roll-formed steel frames made locally also reduce freight, packaging, shipping times, and inventory holding costs.
From a cost perspective, U.S.-made steel module frames qualify for higher domestic content incentives under the Inflation Reduction Act (IRA). According to the latest Internal Revenue Service safe-harbor guidance, U.S.-made steel frames can increase a project’s domestic content by up to 6.1% for rooftop solar projects and 8.5% for ground-mount projects, enabling solar project developers to qualify for an additional 10% bonus to the Investment Tax Credit.
Steel is also greener. Aluminum has long been the default frame material, but its role is increasingly seen as a liability because it contributes disproportionately to a module’s carbon footprint. Carbon emissions from domestically produced steel module frames are 90% lower than aluminum frames currently imported from Southeast Asia. Shifting from aluminum to domestic steel aligns solar infrastructure with the very climate goals it aims to support.
Tackling TariffsTariffs are the talk of the town these days, and they are impacting every aspect of trade imports and supply chains. Aluminum imports—primarily from China, Vietnam, Southeast Asia, and even Canada (which supplies 79% of the U.S. imported primary aluminum) and Mexico—face continued tariff exposure. With antidumping and countervailing duties affecting modules from Cambodia, Malaysia, Thailand, and Vietnam, the uncertainty and cost pressure will continue, injecting greater risk and uncertainty into project cost models.
Steel frames made here in the U.S. carry zero tariffs—as well as translate to quicker delivery times. A domestic steel frame supply chain based on one-day truck deliveries means module buyers can scale back inventory and still avoid project delays due to product unavailability.
Building a Future-Proof Solar Supply ChainU.S.-based steel frame manufacturing is more than a material substitution—it’s a strategic reconfiguration of the solar industry’s foundation. Steel frames (Figures 3 and 4) are drop-in compatible with existing modules and installations. They’re stronger, greener, and more resilient to both physical and geopolitical shocks.
The transition to steel frames and reshoring of production is already happening and gaining momentum, with local steel manufacturers, roll formers, and fabricators in production. Domestic steel manufacturers already supply the bulk of tracker and racking components for the U.S. solar industry. Frames are another logical step in the same direction. The domestic steel industry has both the capacity and capability to supply a growing U.S. solar market with cost-effective steel frames.
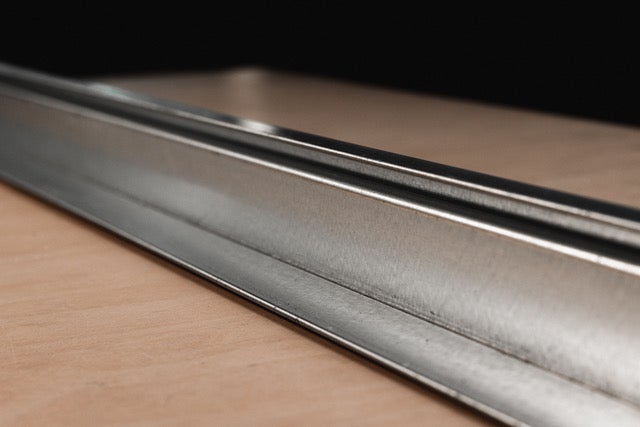
In fact, solar module manufacturing in the U.S. has quintupled since the passage of three key legislative initiatives: the IRA, the Bipartisan Infrastructure Law, and the CHIPS Act. The U.S. is now the third-largest solar module producer in the world, according to the Solar Energy Industries Association (SEIA). As of April 2025, SEIA reports that 84 new solar and storage manufacturing facilities have come online as the result of federal incentives, with 55 additional facilities under active construction. Overall, solar manufacturers have announced $40.6 billion of investments in the U.S. in the last two years, which will create more than 47,000 manufacturing jobs. There are solar manufacturing facilities in 43 states and Puerto Rico—so the ecosystem for domestic production of steel-framed solar modules is fully in place.
Steel is not just a smarter material—it’s a better business decision. It’s stronger, cheaper, cleaner, and available in abundance here at home. Steel frames provide the strength, reliability, and domestic value needed to build a solar future that’s resilient by design. The onshoring of clean energy components is critical to meeting emissions reduction targets, enhancing the security of the solar supply chain, and ultimately delivering a better-quality product.
—Eric Hafter is the founder of Origami Solar and a pioneer in solar product design and commercialization, and international solar project development. He has led large EPC and manufacturing companies.
powermag