Why Nuclear Maintenance Equipment Requires a Single-Source Solution
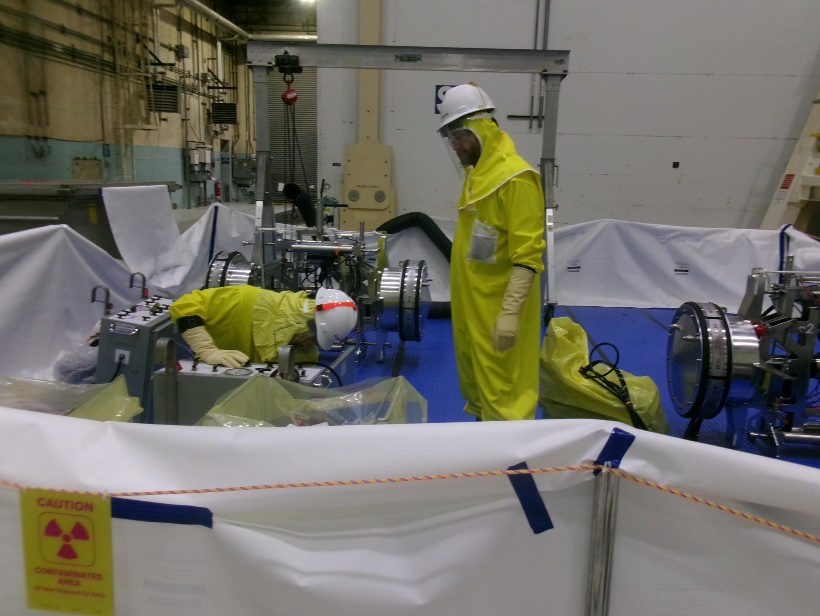
There is no room for missteps, miscommunication, or misunderstandings when it comes to nuclear maintenance. It demands precision, speed, and accountability. The tools and systems used during outages must function flawlessly, because when they don’t, the cost is more than money—it’s exposure, downtime, and slipping maintenance schedules.
Some nuclear plants use a segmented model for purchasing and servicing equipment, where the equipment is sourced from one vendor, engineered by another, and installed or serviced by a third. This divide may seem manageable when everything goes according to plan, but if anything goes wrong, it can be a real mess.
The Risks of Fragmented ResponsibilityWhen the design, manufacturing, and service of a piece of equipment (Figure 1), whether it’s a platform, lifting device, seal system, or shielding assembly, are handled by separate parties, accountability can become unclear. If an issue arises or a field modification is required on short notice, it’s not always obvious who owns the resolution. Project teams can find themselves stuck between vendors, each deferring responsibility to another, while the work halts and outage time extends.
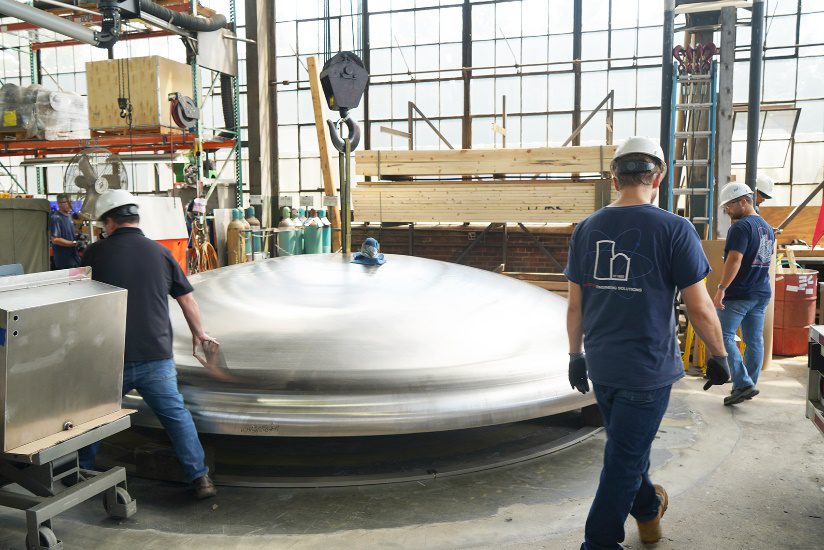
This is particularly problematic in nuclear environments, where delays are more than inconvenient. Fragmented responsibility can lead to:
- Breakdowns between design intent and field realities.
- Longer troubleshooting cycles, as issues must be relayed through multiple layers of communication.
- Inefficient use of plant and contractor resources, as time is spent navigating vendors instead of executing work.
- Limited flexibility for field adjustments, since field teams may not have direct access to the original design team or fabrication specifications.
To reduce these risks, nuclear facilities should shift toward a more integrated approach. Single-source solutions, or vendors who design, build, and support their equipment through its full lifecycle, are an ideal option. It’s not just for convenience; it’s for operational alignment.
When a single provider handles both the engineering and field service, communication is streamlined; adjustments can be made quickly, based on real-time field input; and troubleshooting becomes faster and more accurate. There’s also a clear line of responsibility—if something goes wrong, there’s no ambiguity about who must step in and fix it. This single-source model offers several key benefits for site managers:
- Faster problem resolution thanks to direct access to the subject matter experts.
- Improved design-for-installation outcomes because the manufacturer intimately knows the realities of installing the equipment.
- Simplified project management, which includes one point of contact and one set of documentation.
- Stronger long-term reliability, as onsite lessons learned provide feedback for future designs.
Keep in mind that large vendors may pull in parts from multiple smaller manufacturers behind the scenes. While this is a form of single-source responsibility (one place for you to call), your problem resolution time will be much longer than working with a nimbler single-source manufacturing/service provider. Your large vendor will need to engage with each of their manufacturing partners before coming back with a solution.
Why It MattersIn the highly regulated, high-stakes environment of nuclear power, the margin for error is slim (Figure 2). Every component must not only meet specification, but it must also be field-ready and backed by responsive, knowledgeable support. By consolidating design, manufacturing, and field service in a single-source solution, plants can ensure that the right solution gets installed, maintained, and, when needed, rapidly corrected.
At Preferred Engineering, we’ve seen the pitfalls of fragmented vendor relationships. That’s why we take a unified approach, designing, fabricating, and servicing every piece of nuclear maintenance equipment we provide. From platforms to shielding to plugs and seals, we don’t just ship products, we deploy solutions with full accountability. Whether you’re looking to streamline your outage planning or simplify your maintenance vendor ecosystem, Preferred Engineering offers a better way: one point of contact, complete accountability, and field-proven performance that lets your team stay focused on what matters most—safe, efficient plant operations.
—Steve Mitchell is vice president of Preferred Engineering.
powermag