Modeling the efficiency of using polymer membranes for CO2 separation from natural gas for pipeline transportation
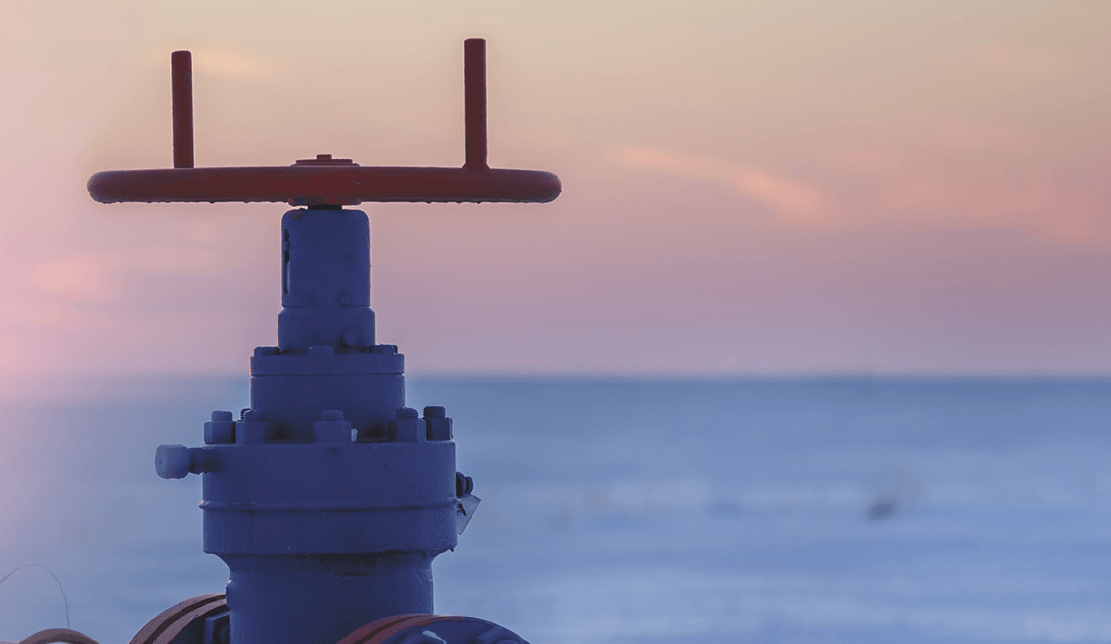
Natural gas enters the pipeline from a variety of sources with varying compositions. Although methane makes up the majority of this mixture (75–90%), natural gas also contains significant concentrations of ethane, propane, butane, and other higher hydrocarbons (1–3%) [1]. Some deposits may contain complex impurities, including CO2, H2S, and CO, which are hazardous to the environment and hinder natural gas processing. Increased demand for pipeline gas in recent years has led to increased interest in processing low-quality raw natural gas. To increase the calorific value of the gas, prevent corrosion of pipelines and process equipment, and avoid crystallization during liquefaction, CO2 emissions must be eliminated [2]. Depending on the source, the amount of CO2 in natural gas can vary from 4 to 50%. Natural gas must be pretreated to meet standard pipeline CO2 content requirements of 2 to 5% before it can be transported [3]. More than 5% of the natural gas produced is carbon dioxide. There are many methods for removing CO2, taking into account environmental considerations, gas characteristics, capital and operating costs. The main procedures are divided into the following categories:Absorption processes (physical and chemical absorption).Solid surface adsorption process.Mixed solution based on physical and chemical solvents.Physical separation (cryogenic and membrane separation).The application of membrane processes in natural gas processing is successful in the market. Differences in the rates of diffusion and/or the degree of adsorption of the components of the mixture in the polymer matrix or the pores of the inorganic membrane allow CO2 to be separated using conventional polymeric or inorganic membranes (such as zeolite, sol-gel silica or carbon molecular sieves). The gas must dissolve on the high-pressure side of the membrane, disperse along the membrane wall and evaporate on the low-pressure side before it can permeate the membrane surface. The idea behind gas separation is that some gases are more soluble in polymer membranes and can pass through them more easily than others. By applying a potential gradient, such as a pressure, temperature, electric current or concentration difference, the membrane, which is a thin layer of semi-permeable material, functions as a selective barrier and separates unwanted particles from the feed solution according to their size or affinity. If one component of the mixture passes through the membrane faster than the other, separation is achieved. The main advantage of membrane technology, which distinguishes it from traditional separation, purification and formulation methods, is that it produces stable products without the use of chemicals, consumes very little energy and has a high potential for environmental impact. Additional advantages include reduced capital and operating costs for membrane technologies, environmental friendliness, modularity and ease of scaling, and a well-organized, compact and simple process concept and operation. Membranes are often classified according to their materials, shape, driving force and average pore size. One of the most important aspects of the initial differentiation of a membrane is its pore size. The environmental impact of natural gas processing cannot be overstated. Although natural gas is often touted as a cleaner alternative to other fossil fuels, the presence of CO2 and other impurities can negate some of its environmental benefits. By efficiently removing CO2, membrane technology not only improves the quality of natural gas, but also helps reduce greenhouse gas emissions. This is in line with global sustainable development goals aimed at mitigating climate change and promoting cleaner energy sources. In addition, membrane processes typically require less energy than traditional methods such as amine scrubbing or cryogenic separation. This reduction in energy consumption results in lower operating costs and reduced carbon emissions, making membrane technology a more sustainable option for natural gas processing. From an economic perspective, implementing membrane technology can result in significant cost savings. Traditional CO2 removal methods often involve high capital equipment costs and ongoing operating costs associated with energy and chemical consumption. In contrast, membrane systems are typically more modular and scalable, making them easier to integrate into existing plants without major modifications. This flexibility can encourage operators to upgrade process capabilities while minimizing disruptions. Additionally, as demand for clean energy sources increases, regulatory pressures are likely to increase, requiring investment in emissions-reducing technologies. Companies that adopt advanced membrane technologies more quickly can gain a competitive advantage by positioning themselves as environmental leaders and meeting new regulatory requirements.
The future of CO2 removal from natural gas using membrane technology looks promising. Current research is focused on developing membranes with increased selectivity for CO2 over methane and other hydrocarbons, as well as improving their durability and resistance to fouling. Innovations in nanotechnology and materials science are paving the way for next-generation membranes that could revolutionize gas separation processes. In addition, integrating membrane technology with other processes, such as carbon capture and storage or renewable energy conversion, can create synergies that further improve overall system efficiency. For example, combining membrane separation with renewable energy-based processes could provide a sustainable solution for CO2 removal while utilizing excess energy generated from renewable sources.
We have developed a mathematical model that predicts how well polymer membranes will perform for separating CO2 from CH4 at high pressures. The model is based on solution diffusion theory, which describes how gases move through membranes. According to solution-diffusion theory, there are 2 main processes involved in the movement of a gas through a polymer membrane: Solution: The polymer matrix is where the gas molecules initially dissolve. The solubility of the gas in the polymer and the way the gas molecules interact with the polymer chains influence this step. Diffusion: Once dissolved, the gas molecules move from the polymer matrix with high concentration to the polymer matrix with low concentration. Fick’s diffusion rules, which explain how particles move from areas of higher concentration to areas of lower concentration, govern this process. Solution-diffusion theory provides a comprehensive framework for understanding how gases interact with polymer membranes during separation. Researchers and engineers can create more efficient systems for a variety of industrial applications by optimizing membrane materials and their operating conditions using this theory, which will ultimately improve the efficiency of gas separation technologies. The properties of polymers play a critical role in determining their solubility and diffusivity, which are necessary for applications such as gas separation using polymer membranes. The chemical structure, including the types of monomers and functional groups, significantly affects these properties. For example, polymers with polar functional groups tend to have higher solubility in polar gases due to increased interactions. In addition, the physical properties of polymers, such as free volume, density, and crystallinity, directly affect how easily gases can diffuse through them. Polymers with higher free volumes tend to have higher diffusion rates, facilitating efficient gas transport. In addition, the glass transition temperature (Tg) affects chain mobility; as Tg is exceeded, polymers become more flexible, further increasing gas permeability.
Among the most important equations is the flow equation (1):
Ji = Pi ⋅ (Pifeed material – Pipermeate), (1)
where Ji is the permeation flux of the component, mol/m2 s; Pi is the permeation coefficient of the component, barrer; Pifeed is the partial pressure of the component in the feed, bar; Pipermeate is the partial pressure of component i in the permeate, bar.A binary gas mixture (CO2 and CH4) was used in the model. We introduced parameters that made the permeation independent of pressure and temperature within the operating range and guaranteed that no mixing would occur on either side of the membrane.The following parameters must be taken into account:Membrane selectivity: S = .Feed conditions: pressure, temperature, and CO2 concentration.Membrane properties: thickness, area, and material characteristics.
Using Fick's law for diffusion, the overall mass transfer can be described as (2):
J = k ⋅ (PCO2 – PCH4), (2)
where k is a constant that combines permeability and membrane area. The parameters used in the model are listed in Table 1. The MATLAB model includes additional code for sensitivity analysis that varies the feed pressure and calculates the corresponding CO2 flux, so it is possible to see how the flux changes at high pressure.
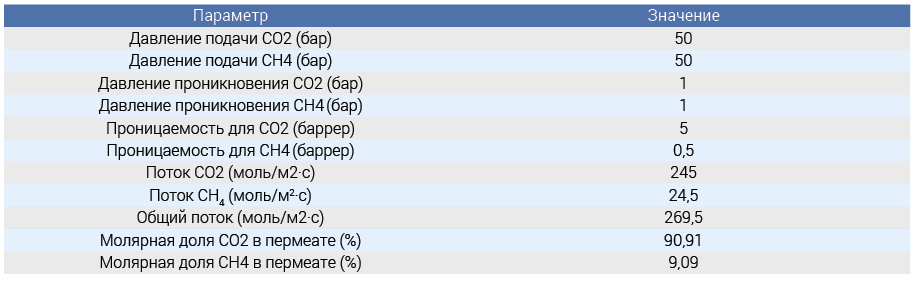
To test the accuracy, we compared the model predictions with published experimental data. This required the use of previously published data on CO2 permeability and separation coefficient under comparable circumstances. Our model was compared with a previously published study on sea gas from 2008. The study investigated the performance of Pebax®/PEG blend thin film composite membranes for the separation of CO2 from gas mixtures containing H2, N2 and CH4. The membranes were tested under various conditions and the dependence of the gas flux and selectivity on temperature and pressure was studied. Before testing the membranes, one of the listed gases (CO2, H2, N2 and CH4) was used in the gas mixture. The tests were carried out at a temperature of 293 °K and a high pressure of up to 20 bar. These conditions were chosen for comparison with the gas mixture measurements. The results are displayed on the console along with the fluxes and permeate composition. This composition is often formed as a result of gas purification or separation procedures where methane is a by-product and CO2 is the main target for capture. High amounts of CO₂ indicate efficient separation methods, which are required for processes such as carbon capture and storage and biogas upgrading. The modeling results demonstrate the possibility of obtaining high purity CO2 for industrial applications (Figure 1). When the CO₂ content in the permeate is 90.91% and CH₄ (methane) is 9.09%, this indicates that the analyzed or processed gas mixture contains a high concentration of carbon dioxide compared to methane.
A graph of the CO2 flow versus supply pressure is also displayed (Fig. 1).
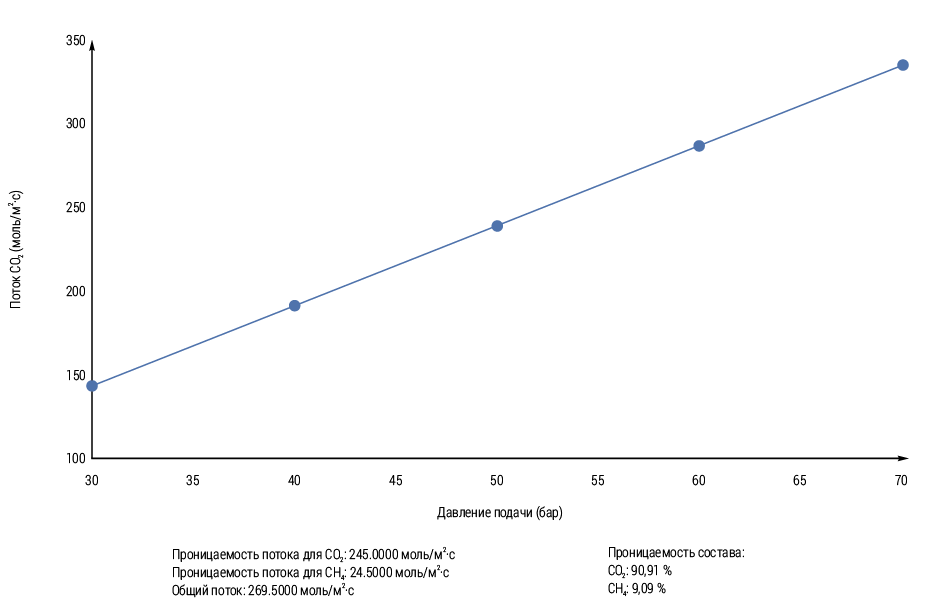
Figure 2 shows the CO2 flux as a function of the feed pressure. For all samples (Pebax® membranes and Pebax®/PEG blend membranes) the CO2 flux increased with increasing feed pressure (fugacity) from 5 to 20 bar. In rubbery polymers, the solubility coefficient is decisive, which strongly depends on the condensability of the gas, especially in the presence of strong interaction between the penetrant and the polymer [4].
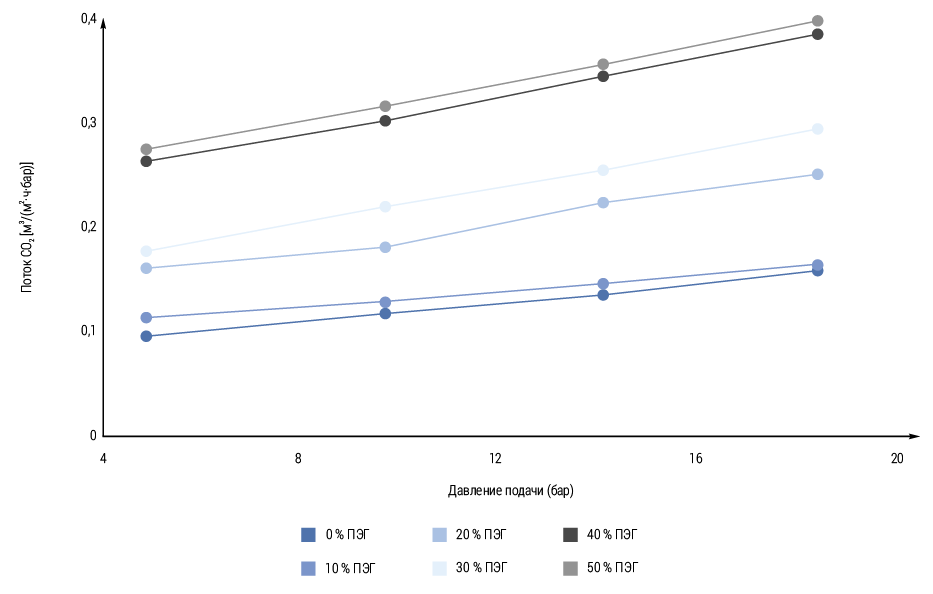
As can be seen from Fig. 2, the slope of the line shifts to higher values with increasing PEG content. PEG is polyethylene glycol (PEG), an ethylene oxide-based polymer, is a good membrane former due to its hydrophilic properties and also because it is chemically stable and can withstand very high temperatures and pressures. Therefore, samples with higher PEG content show a stronger pressure dependence due to plasticization. CO2 sorption levels are strongly dependent on segment packing, and plasticization is related to the mobility of the segments. Thus, the CO2 flux at higher operating pressure and high PEG content always increases. Moreover, in the obtained model, the CO2 flux is higher at higher pressure. In both our model and experimental data, we observed a consistent trend: the CO2 flux increased with increasing pressure. This correlation suggests that higher pressure conditions promote greater CO2 transport. The obtained results are consistent with the established gas permeation theories, which confirms the validity of our model. The increase in CO₂ flow rate with increasing pressure indicates that pressure variations affect the rate of carbon dioxide emission or absorption by the system. Pressure gradients affect the flow of gases, including CO₂. Diffusion of CO₂ from areas of higher concentration to areas of lower concentration can be enhanced by increasing the pressure, resulting in increased flow. The efficiency of separating CO2 from methane or other gases can be improved by selectively increasing the pressure. Operators can maximize the CO2 removal rate by adjusting the pressure inside membranes or absorption systems [5]. In addition, this behavior highlights the importance of pressure as a critical parameter for optimizing CO2 separation processes. Overall, the results confirm the effectiveness of our approach in accounting for the dynamics of CO2 flow with pressure changes. This experiment validates the model. The results highlight the importance of developing sophisticated methods for estimating CO2 emissions and improving separation technology. The simulation model results are consistent with experiment and real-world conditions.
It also highlights the need for high-quality data to accurately assess regional and global CO2 fluxes. The results could help address the ongoing challenge of greenhouse gas emissions and improve both monitoring and management tactics.
In our study, we developed a mathematical model to predict the performance of polymeric membranes for separating carbon dioxide (CO2) from methane (CH4) under high pressure conditions. The model was validated by comparing its predictions with published experimental data, with a particular focus on the performance of thin-film composite membranes such as Pebax®/PEG blends in separating CO2 from gas mixtures containing hydrogen (H2), nitrogen (N2) and CH4. The validation was supported by data from a 2008 study that investigated the performance of these membranes under controlled conditions. The experiments were conducted at 293°K and pressures up to 20 bar, which are typical operating scenarios in gas separation processes. Our model successfully predicted the flow rates and selectivity coefficients observed in these experiments, demonstrating its robustness and accuracy.
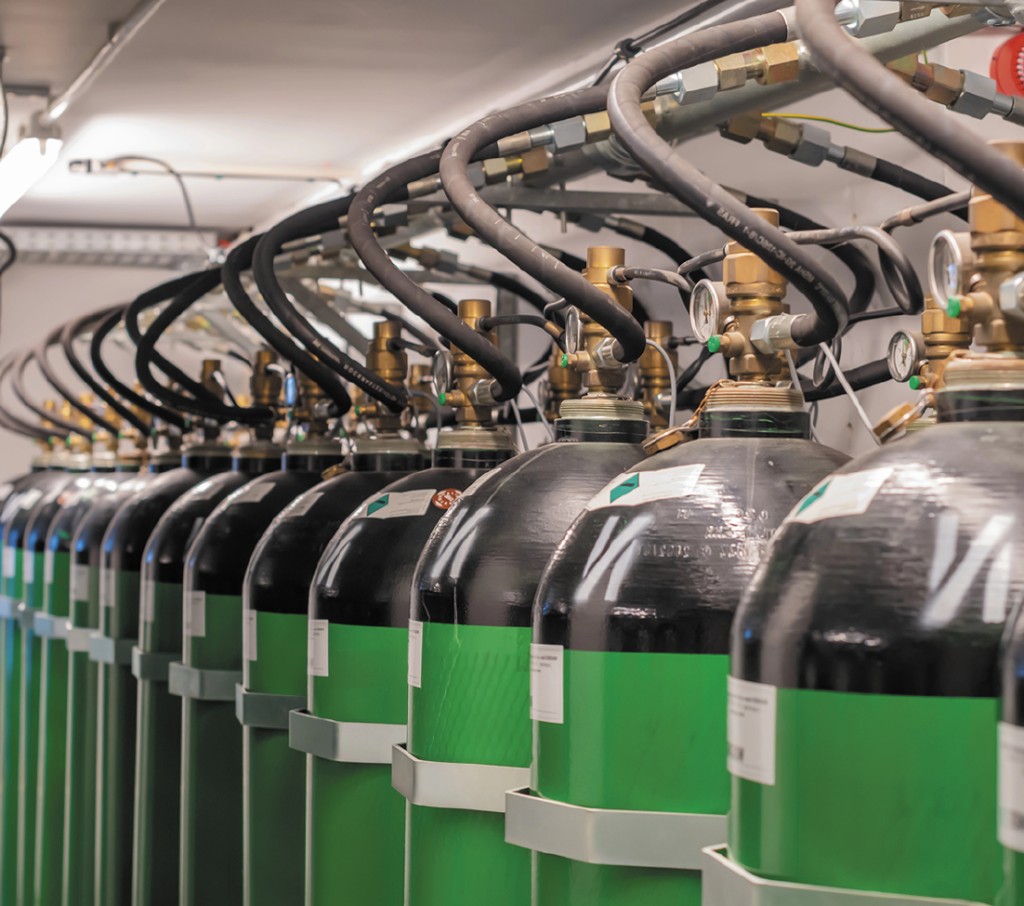
One of the important results of our modeling is a strong correlation between the supply pressure and the flow of CO2. CO2 can reach approximately 90.91%, and methane - 9.09%indicates the high efficiency of the separation process. The content of polyethylene glycol (PEG) has increased permeability for CO2 due to increased plasticization with increased pressure. This discovery suggests that the optimization of membrane materials can significantly increase the efficiency of separation by adaptation of their chemical and physical properties. On the drawings included in our analysis, the relationship between the CO2 stream and the supply pressure, which illustrates how the changes in the transfer of the gas transfer, showed that with an increase in the pressure, the CO2 transmission speed through the membrane system emphasizes the importance of the importance. Information as a critical parameter for optimizing the processes of gas separation. In addition, we noted that the slope of the CO2 flux currency changes when the PEG concentration changes, which indicates a more pronounced effect of pressure on the membrane with a high PEG content. Our studies go beyond the theoretical check. Understanding how various working parameters affect the effectiveness of the separation of CO2, operators can optimize their processes for maximizing the extraction of CO2 with minimizing methane losses. In addition, our studies emphasize the need for constant improvement of membrane technologies. Tim that the study of alternative polymer compositions or hybrid materials can lead to a membrane with an even higher selectivity and permeability for CH4 than CH4, and the study of the advanced methods of modeling or machine learning can improve our understanding of complex gas transfers in polymer membranes. In real time with our forecasting model, the dynamic adjustment of the working parameters depending on the fluctuations of the composition of the raw materials or changes in pressure, which further optimizes the separation processes.
Thus, our study provides a reliable mathematical basis for predicting the effectiveness of the separation of CO2/CH4 using polymer membranes in conditions of high pressure. Efforts aimed at developing sustainable technologies for capturing and utilization of carbon.
energypolicy