The Future of Ammonia as an Alternative Motor Fuel
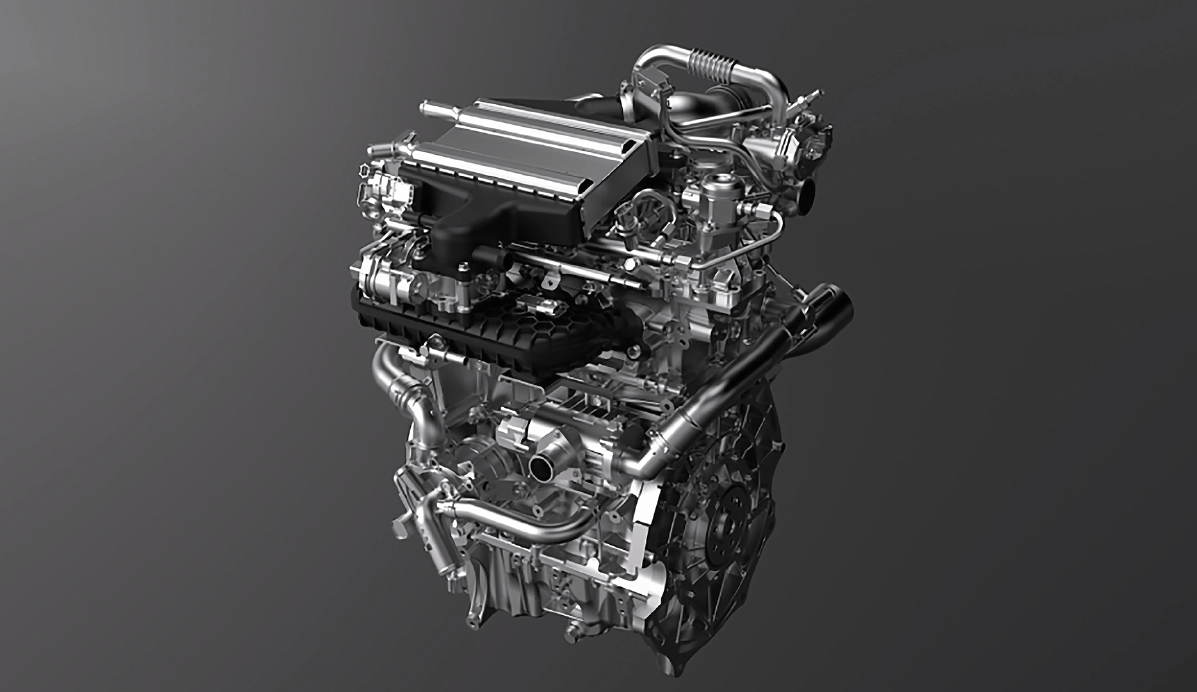
One of the greatest chemical processes created in the 20th century was the synthesis of ammonia. The driving force behind the development of this process was the need to provide food for the growing population of the Earth. The only source of nitrogen-containing mineral fertilizers at the beginning of the 20th century were the reserves of ammonium nitrate in Chile. These reserves were rapidly depleting and it seemed that the forecast of the English priest and scientist Thomas Malthus, who believed that scientific and technological progress could not compensate for the limited natural resources, might come true. At the beginning of the 20th century, the main challenge for scientists around the world was the problem of chemical fixation of nitrogen. A natural way to solve this problem was to bind atmospheric nitrogen in the form of synthetic ammonia. The credit for developing an industrial method for obtaining ammonia from nitrogen and hydrogen goes to two German scientists - Fritz Haber and Carl Bosch. F. Haber was the first to develop a method for obtaining ammonia in laboratory conditions, and K. Bosch created the engineering foundations of the industrial process. Both became Nobel Prize laureates: F. Haber in 2019, and K. Bosch in 1931. More than 100 years have passed, and all ammonia synthesis reactors in the world are built in accordance with the technological solutions developed by Carl Bosch. Currently, global ammonia production reaches 200 million tons per year. This allows providing nitrogen fertilizers to major agricultural producers (China, India, USA, Russia). The annual growth rate of ammonia production in recent years has not exceeded 1.5%. This indicates the stability of the ammonia market. Until now, the main use of ammonia has been the production of mineral fertilizers and industrial explosives. Recently, a new direction of using ammonia as a motor fuel has begun to develop rapidly. Ammonia contains a large proportion of hydrogen, and does not release carbon dioxide when burned, making it a clean and environmentally friendly fuel. Ammonia is much easier to store and transport than hydrogen. Finally, ammonia is an energy-rich fuel, with a calorific value only 3 times lower than that of gasoline or diesel fuel.
An analysis of the possibility of using ammonia as a motor fuel should begin with an examination of its energy characteristics in comparison with traditional types of motor fuels – gasoline, diesel fuel (DF) and natural gas (Table 1).

Several energy and thermodynamic characteristics of ammonia are very close to traditional fuels. First of all, this is the temperature and pressure of condensation, which allows storing ammonia and traditional fuels in a liquid state (except for natural gas). All fuels, including ammonia, also have close values for the maximum (adiabatic) combustion temperature - from 1800 to 2030 °C. However, some physical characteristics of NH3 limit its use in engines. Thus, the value of the volumetric energy density of NH3 is significantly lower compared to traditional hydrocarbon fuels (Table 1). This means that the volume of fuel (or storage tanks) required to generate the same amount of energy will increase by 2.5-3 times when using NH3. In addition, NH3 has a much higher autoignition temperature compared to traditional fuels. Therefore, for a diesel engine to operate with ammonia, much higher compression ratios are required – at least 35:1 – compared to the values used for diesel fuel (from 14:1 to 22:1) [1]. This places increased demands on the strength and corrosion resistance of the materials used to manufacture the engines. The lower flame propagation speed during ammonia combustion can lead to instability of the combustion process.
In 2019–2020, the largest diesel engine manufacturers MAN Energy Solutions (Germany) and Wärtsilä (Finland) announced the start of development of two- and four-stroke diesel engines running on ammonia [2]. The greatest attention to the use of ammonia as a replacement for motor fuel is paid to the maritime transport sector. The Norwegian company Yara announced the construction of the world's first "emission-free" marine vessel running on "pure ammonia" without the use of hydrocarbon fuel (fuel oil or diesel fuel). It is planned that this vessel will begin to be used as early as 2026 for sea transportation of fertilizers on the Norway–Germany route.
Currently, the problem of insufficient combustion efficiency of ammonia in diesel engines is solved by mixing it with a small amount of regular diesel fuel (the so-called "pilot fuel"), which is injected into the fuel system and initiates the combustion of ammonia [1]. Experiments conducted back in 1977 showed that of the four main fuels - methanol, ethanol, methane and ammonia - ammonia is the least suitable for operation in a diesel engine, even in a dual-fuel version [3]. In addition to significant emissions of incompletely oxidized NH3 (up to 0.5% vol.), its use led to the maximum ignition delay, the lowest output power and efficiency compared to other types of fuel (Table 2).

However, after the start of the CO2 emission reduction campaign, the fundamental applicability of the ammonia + diesel dual-fuel scheme for multi-cylinder turbocharged diesel engines was demonstrated. This required only a minor modification of the fuel intake system to supply an ammonia feed line, while the hydrocarbon fuel injection system remained unchanged [4]. Stable engine operation was possible with up to 95% (by energy) of diesel fuel replaced by NH3, and significant fuel savings (the highest operating efficiency) were achieved with an ammonia content of 40–60%. At NH3 content below 60%, a significant decrease in NOx emissions was observed, which the authors attributed to a decrease in flame temperature. However, this reduced the completeness of combustion of diesel fuel, which was manifested through an increase in hydrocarbon emissions. More detailed studies carried out later [5] showed that at ammonia content above 60%, the fuel ignition delay increased. At the same time, with an increase in the proportion of diesel fuel above 60% with the engine running at a constant power, the composition of the ammonia-air mixture in the engine can reach the explosive limits, and a decrease in the combustion temperature reduces the efficiency of fuel combustion as a whole. Another important problem that must be solved when using ammonia in dual-fuel schemes is associated with the system for feeding it to the combustion chamber. Thus, ammonia can be injected into the intake valve (in this case, homogeneous mixtures of fuel with air are obtained) or fed directly into the cylinder in liquid form. The latter option is preferable, since it allows dosing ammonia directly from storage tanks in liquid form (at a pressure of about 17 atm.) without preliminary evaporation. When dosing liquid, the pressure in the combustion chamber can be significantly increased. However, due to the high value of saturated vapor pressure and the strong dependence of saturated vapor pressure on temperature, ammonia is characterized by instantaneous boiling and evaporation when the pressure decreases. This effect is especially pronounced in the inlet nozzles and significantly changes the patterns of formation of gas-air mixtures, leading in some cases to poor mixing of fuel with air and deeper penetration of liquid into the engine, up to wetting the walls [6]. Also, with liquid injection, a sharp decrease in temperature during evaporation of ammonia significantly reduces the stability of the flame. To reduce this negative effect, preliminary heating and turbulence of the air flow supplied to the combustion chamber are proposed. In general, additional research is required in this area to understand the features of the processes of formation of ammonia-air mixtures and their combustion in internal combustion engines, as well as the development of optimal fuel supply modes.
At MAN Energy Solutions, the ammonia dosing system is based on similar systems previously developed for liquefied petroleum gases and methanol. It was announced that, if pilot tests are successfully completed in 2023, the first two-stroke engine running on ammonia will be installed on an industrial vessel in 2024 [7]. Wärtsilä Corporation announced the production of the first industrial four-stroke engine running on a mixture of diesel and ammonia in late 2023 [8], and in early 2024, the availability of an ammonia supply system that works with both liquid and gaseous feedstock [9]. They are expected to be installed in 2025 on mid-size LNG carriers, which are being specially built for this purpose at the Hyundai Mipo shipyards in South Korea for EXMAR LPG.
The possibility of using ammonia in motor transport is also being actively studied. This work is being carried out in two directions. Firstly, ammonia is used as an energy carrier for fuel cells that power the car's electric motor. Another option for using ammonia is to directly replace gasoline or diesel fuel in an internal combustion engine. The first such engine has already been demonstrated in 2023 by the alliance of GAC (China) and Toyota (Japan) [10]. However, the main direction for using ammonia in motor transport is technologies based on the use of ammonia fuel cells as energy sources. First of all, this is a more efficient method of extracting energy from ammonia, characterized by lower emissions of NH3 and nitrogen oxides, as well as low noise [2]. Fuel cells themselves take up significantly less space than internal combustion engines. Proton exchange membrane fuel cells (PEMFC) and solid oxide fuel cells (SOFC) are considered the most promising [11]. PEMFC prototypes (but without using ammonia as a source of H2) are already used in ground transport. The auxiliary equipment required for their operation (cooling, ventilation, fuel supply systems, etc.) is approximately the same as for a conventional engine. The main problem with the transition to ammonia in PEMFC fuel cells is that the purity of H2 must be no lower than > 99.5% with a complete absence of NH3 traces. SOFC fuel cells can use ammonia as a fuel without preliminary decomposition and release of H2, which allows achieving higher power values per unit weight of fuel. However, SOFC fuel cells must use an energy storage system to compensate for slow processes during transient modes and provide them with energy in starting modes. The use of ammonia as an energy carrier is not limited to transport. Research is being intensively conducted on replacing hydrocarbon fuel with ammonia in gas turbines. To reduce the carbon footprint in thermal power engineering, a process for the compatible combustion of coal and ammonia is being developed.
Most publications on the fuel and energy use of ammonia are primarily advertising in nature and are limited, at best, to assessing the reduction in carbon dioxide emissions. Experimental data on the content of other compounds in the exhaust gases of internal combustion engines are generally not provided. However, when burning ammonia, along with environmentally friendly nitrogen, various forms of nitrogen oxides (NO, NO2, N2O) may form:
2NH3 + 3/2O2 = N2+ 3H2O + 634 kJ/mol (1)2NH3 + 2O2 = N2O + 3H2O + 552 kJ/mol (2)2NH3 + 5/2O2 = 2NO + 3H2O + 453 kJ/mol (3)
2NO + O2 = 2NO2–113 kJ/mol (4)
Their content in combustion products can reach 0.28% vol. In addition, due to the low efficiency of ammonia combustion, its residual concentration in exhaust gases even under optimal combustion conditions is 0.1–0.3% vol. [12]. Even at low concentrations in the air (0.0005–0.005% vol.), NH3 irritates the eyes and respiratory tract, and at a content of ~1% vol., instant death occurs. Emissions of nitrogen oxides contribute to the formation of photochemical smog and "acid rain", and the decomposition of the ozone layer. A concentration of NO2, formed from NO at room temperature, over 0.02% vol. is considered lethal. Increased efficiency of NH3 combustion and reduction of NO and NO2 emissions are achieved by preheating the fuel, as well as by additionally increasing the pressure in the combustion chamber (the latter is already higher than when working with diesel fuel). A good alternative to unsafe and expensive increases in pressure or temperature can be the use of industrial technology for reducing nitrogen oxide emissions based on their selective catalytic reduction with ammonia (SCR NH3) to nitrogen and water based on the following reactions:
6NO + 4NH3 → 5 N2 + 6H2O + 1095 kJ/mol (5)4NO + 4NH3 + O2 → 4N2 + 6H2O + 1629 kJ/mol (6)6NO2 + 8NH3 → 7N2 + 12H2O + 2737 kJ/mol (7)
2NO2 + 4NH3 + O2 → 3 N2 + 6H2O + 1335 kJ/mol (8)
In recent years, such catalytic technology has been adapted for cargo and marine transport, where products based on high-boiling petroleum fractions with a relatively high content of nitrogen-containing compounds are used as fuel [13]. The high corrosive activity of ammonia places special demands on materials for engines and fuel supply systems, as well as its purity. Thus, any alloys with copper and nickel with a content of the latter above 6% cannot be used in fuel systems, vessels for its storage, as well as its supply lines. Only Teflon is suitable for seals/gaskets and insulation in such systems. Due to accelerated stress corrosion cracking of steel, especially at elevated temperatures, in the presence of moisture and air, their maximum content in ammonia should not exceed 0.1% by weight and several millionths. Accordingly, special technologies are needed to ensure the required fuel purity.
What problems can be identified in the transition of transport to ammonia fuel? These are, first of all: a) corrosion problems when engine components come into contact with ammonia; b) high toxicity of ammonia; c) relatively low specific energy capacity of ammonia as a fuel; d) formation of nitrogen oxides from ammonia during its combustion. It is worth paying attention to the technical and economic prospects of ammonia as a motor fuel. The lower calorific value of ammonia compared to diesel fuel is almost compensated by its low cost in Russia. This means that ammonia is already competitive as a fuel in terms of cost. In the existing processes of ammonia synthesis from natural gas, carbon dioxide is inevitably formed - approximately 2.5 tons of CO2 per 1 ton of ammonia. Utilization of concentrated CO2 on site is significantly cheaper and technologically simpler than solving this problem for an individual car on hydrocarbon fuel. Thus, the use of ammonia in technological processes opens up opportunities for creating transport without a carbon footprint. Commercial use of ammonia in this capacity is predicted to begin in 2035–2037. It is expected that by 2050, marine transport will use predominantly liquefied natural gas (65–70%) and ammonia (20–25%). The share of low-sulfur fuel oil will be only 10%. This will lead to the need to double global ammonia production by 2050 – to 400 million tons/year.
The use of ammonia in marine and automobile transport will inevitably give impetus to the development of internal combustion engines. Ammonia engines may be completely different from gasoline or diesel engines. Perhaps ammonia will not be a mono-fuel and will require the introduction of special additives (similar to octane-boosting additives). The need to increase ammonia production capacity stimulates progress in new technologies for its synthesis. This will cause an increase in scientific research in the field of catalytic processes associated with the synthesis of ammonia, and the industrial development of the results of this work.
The work was carried out with the financial support of the Ministry of Science and Higher Education of the Russian Federation within the framework of the state assignment of the Institute of Catalysis SB RAS (project FWUR-2024-37).
energypolicy