Przyszłość amoniaku jako alternatywnego paliwa silnikowego
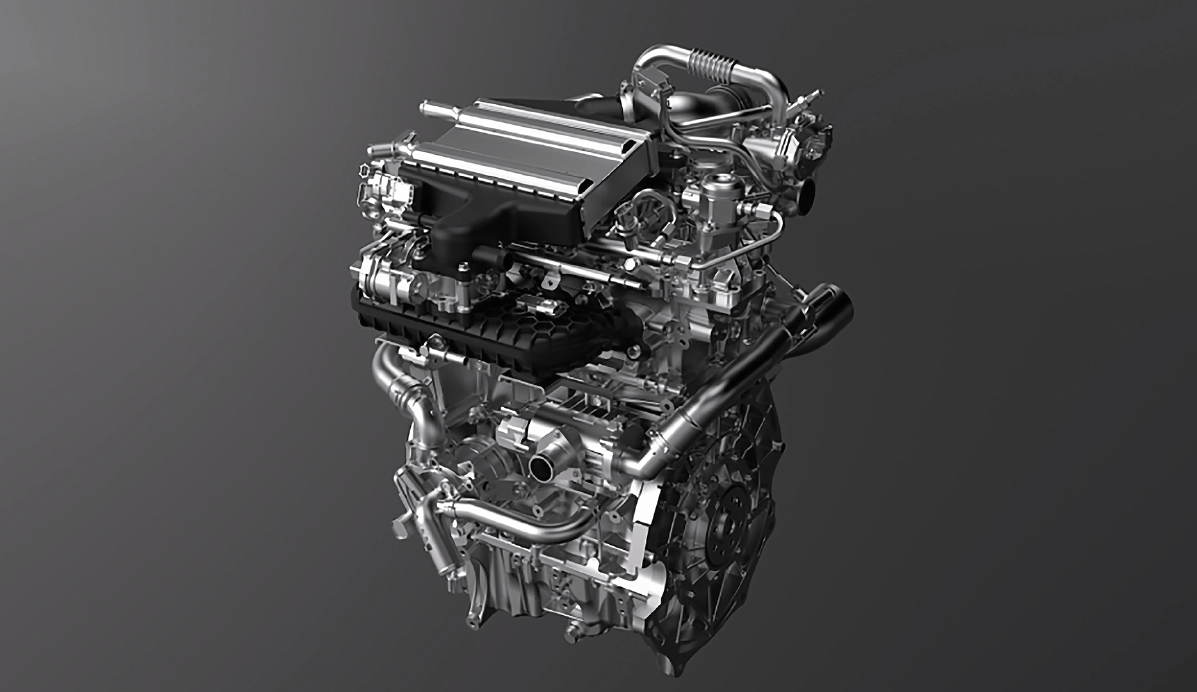
Jeden z największych procesów chemicznych stworzonych w XX wieku. - to jest synteza amoniaku. Siłą napędową rozwoju tego procesu była potrzeba zapewnienia pożywienia rosnącej populacji Ziemi. Jedyne źródło nawozów mineralnych zawierających azot na początku XX wieku. znajdowały się rezerwy saletry amonowej w Chile. Rezerwy te szybko się kurczyły i wydawało się, że prognoza angielskiego księdza i naukowca Thomasa Malthusa, który uważał, że postęp naukowy i techniczny nie zrekompensuje ograniczonych zasobów naturalnych, może się spełnić. Na początku XX wieku. Największym wyzwaniem dla naukowców na całym świecie stało się rozwiązanie problemu chemicznego wiązania azotu. Naturalnym sposobem rozwiązania tego problemu było związanie atmosferycznego azotu w postaci syntetycznego amoniaku. Za opracowanie przemysłowej metody produkcji amoniaku z azotu i wodoru należy uznać zasługę dwóch niemieckich naukowców – Fritza Habera i Carla Boscha. F. Haber jako pierwszy opracował metodę produkcji amoniaku w warunkach laboratoryjnych, a K. Bosch stworzył podstawy inżynieryjne procesu przemysłowego. Obaj zostali laureatami Nagrody Nobla: F. Haber w 2019 r., a K. Bosch w 1931 r. Minęło ponad 100 lat, a wszystkie reaktory syntezy amoniaku na świecie są zbudowane zgodnie z rozwiązaniami technologicznymi opracowanymi przez Carla Boscha. Obecnie światowa produkcja amoniaku sięga 200 milionów ton rocznie. Dzięki temu możliwe jest zaopatrzenie w nawozy azotowe głównych producentów rolnych (Chiny, Indie, USA, Rosja). Roczna stopa wzrostu produkcji amoniaku w ostatnich latach nie przekroczyła 1,5%. Świadczy to o stabilizacji rynku amoniaku. Głównym obszarem wykorzystania amoniaku była dotychczas produkcja nawozów mineralnych i materiałów wybuchowych przemysłowych. W ostatnim czasie zaczął się dynamicznie rozwijać nowy obszar wykorzystania amoniaku jako paliwa silnikowego. Amoniak zawiera dużą ilość wodoru i podczas spalania nie wydziela dwutlenku węgla, dzięki czemu jest paliwem czystym i przyjaznym dla środowiska. Amoniak jest znacznie łatwiejszy w przechowywaniu i transporcie niż wodór. Wreszcie amoniak jest paliwem bogatym w energię, o wartości kalorycznej tylko 3 razy niższej niż benzyna czy olej napędowy.
Analizę możliwości wykorzystania amoniaku jako paliwa silnikowego należy rozpocząć od zbadania jego charakterystyk energetycznych w porównaniu z tradycyjnymi rodzajami paliw silnikowych – benzyną, olejem napędowym (DF) i gazem ziemnym (tab. 1).

Pod względem właściwości energetycznych i termodynamicznych amoniaku jest on bardzo zbliżony do paliw tradycyjnych. Przede wszystkim jest to temperatura i ciśnienie skraplania, które umożliwiają przechowywanie amoniaku i tradycyjnych paliw w stanie ciekłym (za wyjątkiem gazu ziemnego). Wszystkie paliwa, łącznie z amoniakiem, mają podobne wartości maksymalnej (adiabatycznej) temperatury spalania – od 1800 do 2030 °C. Jednak niektóre właściwości fizyczne NH3 ograniczają jego zastosowanie w silnikach. Zatem wartość gęstości objętościowej energii NH3 jest znacznie niższa w porównaniu do tradycyjnych paliw węglowodorowych (Tabela 1). Oznacza to, że objętość paliwa (lub zbiorników magazynowych) niezbędna do wytworzenia tej samej ilości energii przy użyciu NH3 wzrośnie 2,5–3 razy. Ponadto NH3 ma znacznie wyższą temperaturę samozapłonu w porównaniu do paliw tradycyjnych. Dlatego też, aby silnik Diesla mógł pracować na amoniaku, konieczne są znacznie wyższe stopnie sprężania – co najmniej 35:1 – w porównaniu do wartości stosowanych przy pracy na oleju napędowym (od 14:1 do 22:1) [1]. Stawia to większe wymagania odnośnie wytrzymałości i odporności na korozję materiałów wykorzystywanych do produkcji silników. Niższa prędkość rozprzestrzeniania się płomienia podczas spalania amoniaku może prowadzić do niestabilności procesu spalania.
W latach 2019–2020 najwięksi producenci silników Diesla MAN Energy Solutions (Niemcy) i Wärtsilä (Finlandia) ogłosili rozpoczęcie prac rozwojowych nad dwu- i czterosuwowymi silnikami Diesla zasilanymi amoniakiem [2]. Największą uwagę zagadnieniu wykorzystania amoniaku jako zamiennika paliwa silnikowego poświęca się w sektorze transportu morskiego. Norweska firma Yara poinformowała o budowie pierwszego na świecie statku morskiego o „zerowej emisji”, który będzie napędzany „czystym amoniakiem” bez użycia paliw węglowodorowych (oleju opałowego lub oleju napędowego). Planuje się, że statek ten zacznie być wykorzystywany już w 2026 roku do transportu morskiego nawozów na trasie Norwegia-Niemcy.
Obecnie, aby rozwiązać problem niedostatecznej efektywności spalania amoniaku w silnikach Diesla, miesza się go z niewielką ilością zwykłego oleju napędowego (tzw. „paliwa pilotażowego”), które jest wtryskiwane do układu paliwowego i inicjuje spalanie amoniaku [1]. Eksperymenty przeprowadzone już w 1977 roku wykazały, że spośród czterech głównych paliw – metanolu, etanolu, metanu i amoniaku – amoniak jest najmniej odpowiedni do pracy w silniku Diesla, nawet w wersji dwupaliwowej [3]. Oprócz znacznej emisji niecałkowicie utlenionego NH3 (do 0,5% obj.), jego stosowanie skutkowało najdłuższym opóźnieniem zapłonu, najniższą mocą wyjściową i wydajnością w porównaniu z innymi paliwami (Tabela 2).

Jednak po rozpoczęciu kampanii na rzecz redukcji emisji CO2 wykazano zasadniczą przydatność schematu zasilania dwupaliwowego amoniakiem i olejem napędowym w przypadku wielocylindrowych turbodoładowanych silników wysokoprężnych. Wymagało to jedynie niewielkich modyfikacji układu dolotowego paliwa, aby dostosować go do przewodu doprowadzającego amoniak, podczas gdy układ wtrysku paliwa węglowodorowego pozostał niezmieniony [4]. Stabilną pracę silnika udało się uzyskać dzięki zastąpieniu aż 95% (energetycznie) oleju napędowego NH3, a znaczące oszczędności paliwa (najwyższą sprawność roboczą) uzyskano przy zawartości amoniaku w paliwie na poziomie 40–60%. Przy zawartości NH3 poniżej 60% zaobserwowano znaczącą redukcję emisji NOx, co autorzy przypisali obniżeniu temperatury płomienia. Spowodowało to jednak zmniejszenie stopnia spalania oleju napędowego, co objawiało się wzrostem emisji węglowodorów. Bardziej szczegółowe badania przeprowadzone później [5] wykazały, że gdy zawartość amoniaku przekraczała 60%, opóźnienie zapłonu paliwa ulegało wydłużeniu. Jednocześnie, gdy udział oleju napędowego wzrasta powyżej 60% przy silniku pracującym ze stałą mocą, skład mieszanki amoniaku i powietrza w silniku może osiągnąć granice wybuchowości, a obniżenie temperatury spalania zmniejsza efektywność spalania paliwa jako całości. Innym ważnym problemem, który należy rozwiązać przy stosowaniu amoniaku w układach dwupaliwowych, jest system jego doprowadzania do komory spalania. Dzięki temu amoniak można wtryskiwać do zaworu dolotowego (co pozwala na uzyskanie jednorodnej mieszanki paliwa i powietrza) lub podawać go bezpośrednio do cylindra w postaci ciekłej. Drugie rozwiązanie jest korzystniejsze, gdyż pozwala na dozowanie amoniaku bezpośrednio ze zbiorników magazynowych w postaci ciekłej (pod ciśnieniem około 17 atm.) bez wcześniejszego odparowywania. Dozując ciecz można znacznie zwiększyć ciśnienie w komorze spalania. Jednakże ze względu na wysoką wartość ciśnienia pary nasyconej i silną zależność ciśnienia pary nasyconej od temperatury, amoniak charakteryzuje się natychmiastowym wrzeniem i parowaniem, gdy ciśnienie spada. Efekt ten jest szczególnie wyraźny w dyszach dolotowych i znacząco zmienia schematy tworzenia się mieszanek gazowo-powietrznych, prowadząc w niektórych przypadkach do gorszego wymieszania paliwa z powietrzem i głębszej penetracji cieczy do silnika, aż do zamoczenia ścianek [6]. Ponadto przy wtrysku cieczy, gwałtowny spadek temperatury podczas odparowywania amoniaku znacznie obniża stabilność płomienia. Aby ograniczyć ten negatywny efekt, proponuje się wstępne podgrzewanie i zawirowanie strumienia powietrza dostarczanego do komory spalania. Ogólnie rzecz biorąc, w tej dziedzinie konieczne są dalsze badania mające na celu zrozumienie specyfiki procesów powstawania mieszanek amoniaku z powietrzem oraz ich spalania w silnikach spalinowych, a także opracowanie optymalnych trybów zasilania paliwem.
W firmie MAN Energy Solutions system dozowania amoniaku bazuje na podobnych systemach opracowanych wcześniej dla skroplonych gazów ropopochodnych i metanolu. Ogłoszono, że jeśli w 2023 roku testy pilotażowe zakończą się sukcesem, pierwszy dwusuwowy silnik zasilany amoniakiem zostanie zamontowany na statku przemysłowym w 2024 roku [7]. Pod koniec 2023 r. firma Wärtsilä Corporation ogłosiła, że wprowadziła na rynek pierwszy przemysłowy czterosuwowy silnik zasilany mieszanką oleju napędowego i amoniaku [8], a na początku 2024 r., że posiada system zasilania amoniakiem, który może pracować zarówno przy użyciu surowca ciekłego, jak i gazowego [9]. Oczekuje się, że zostaną one zamontowane w 2025 r. na średniej wielkości gazowcach LNG budowanych specjalnie w tym celu w stoczniach Hyundai Mipo w Korei Południowej dla EXMAR LPG.
Trwają również intensywne badania nad możliwością wykorzystania amoniaku w transporcie samochodowym. Prace te prowadzone są w dwóch kierunkach. Po pierwsze, amoniak jest wykorzystywany jako nośnik energii w ogniwach paliwowych zasilających silniki elektryczne samochodów. Amoniak może być również stosowany jako bezpośredni zamiennik benzyny lub oleju napędowego w silnikach spalinowych. Pierwszy taki silnik został już zaprezentowany w 2023 roku przez alians GAC (Chiny) i Toyoty (Japonia) [10]. Jednakże głównym obszarem zastosowania amoniaku w transporcie samochodowym są technologie bazujące na wykorzystaniu ogniw paliwowych zasilanych amoniakiem jako źródła energii. Przede wszystkim jest to bardziej efektywna metoda pozyskiwania energii z amoniaku, charakteryzująca się niższą emisją NH3 i tlenków azotu, a także niskim poziomem hałasu [2]. Same ogniwa paliwowe zajmują znacznie mniej miejsca niż silniki spalinowe. Najbardziej obiecujące są ogniwa paliwowe z membraną wymiany protonów (PEMFC) i ogniwa paliwowe ze stałym tlenkiem (SOFC) [11]. Prototypy PEMFC (jednak bez wykorzystania amoniaku jako źródła H2) są już wykorzystywane w transporcie naziemnym. Urządzenia pomocnicze niezbędne do ich działania (układy chłodzenia, wentylacji, zasilania paliwem itp.) są w przybliżeniu takie same jak w przypadku silnika konwencjonalnego. Głównym problemem przy przechodzeniu na amoniak w ogniwach paliwowych PEMFC jest to, że czystość H2 nie może być niższa niż > 99,5% przy całkowitym braku śladów NH3. Ogniwa paliwowe SOFC mogą wykorzystywać amoniak jako paliwo bez wcześniejszego rozkładu i emisji H2, co pozwala na osiągnięcie wyższych wartości mocy w przeliczeniu na jednostkę masy paliwa. Jednakże ogniwa paliwowe SOFC wymagają układu magazynowania energii, który będzie w stanie kompensować wolne procesy w warunkach przejściowych i dostarczać energię w warunkach rozruchu. Zastosowanie amoniaku jako nośnika energii nie ogranicza się wyłącznie do transportu. Prowadzone są intensywne badania nad zastąpieniem paliw węglowodorowych amoniakiem w turbinach gazowych. Aby zmniejszyć ślad węglowy w energetyce cieplnej, opracowywany jest proces umożliwiający spalanie węgla i amoniaku.
Większość publikacji na temat wykorzystania amoniaku jako paliwa i energii ma przede wszystkim charakter promocyjny i w najlepszym razie ograniczają się do oceny redukcji emisji dwutlenku węgla. Dane eksperymentalne dotyczące zawartości innych związków w spalinach silników spalinowych nie są na ogół dostępne. Jednak podczas spalania amoniaku wraz z przyjaznym dla środowiska azotem mogą powstawać różne formy tlenków azotu (NO, NO2, N2O):
2NH3 + 3/2O2 = N2+ 3H2O + 634 kJ/mol (1)2NH3 + 2O2 = N2O + 3H2O + 552 kJ/mol (2)2NH3 + 5/2O2 = 2NO + 3H2O + 453 kJ/mol (3)
2NO + O2 = 2NO2–113 kJ/mol (4)
Ich zawartość w produktach spalania może sięgać 0,28% obj. Ponadto, ze względu na niską efektywność spalania amoniaku, jego stężenie resztkowe w spalinach, nawet w optymalnych warunkach spalania, wynosi 0,1–0,3% obj. [12]. Nawet w niskich stężeniach w powietrzu (0,0005–0,005% obj.) NH3 powoduje podrażnienie oczu i dróg oddechowych, a przy stężeniu ~1% obj. następuje natychmiastowa śmierć. Emisje tlenków azotu przyczyniają się do powstawania smogu fotochemicznego i kwaśnych deszczów oraz rozkładu warstwy ozonowej. Stężenie NO2 powstającego z NO w temperaturze pokojowej większe niż 0,02% obj. jest uważany za śmiertelny. Zwiększenie efektywności spalania NH3 oraz obniżenie emisji NO i NO2 uzyskuje się poprzez wstępne podgrzanie paliwa, a także dodatkowe zwiększenie ciśnienia w komorze spalania (to drugie jest już wyższe niż przy pracy na oleju napędowym). Dobrą alternatywą dla niebezpiecznego i kosztownego zwiększania ciśnienia lub temperatury może być wykorzystanie technologii przemysłowej do redukcji emisji tlenków azotu, opartej na ich selektywnej redukcji katalitycznej amoniakiem (SCR NH3) do azotu i wody, w oparciu o następujące reakcje:
6NO + 4NH3 → 5 N2 + 6H2O + 1095 kJ/mol (5)4NO + 4NH3 + O2 → 4N2 + 6H2O + 1629 kJ/mol (6)6NO2 + 8NH3 → 7N2 + 12H2O + 2737 kJ/mol (7)
2NO2 + 4NH3 + O2 → 3N2 + 6H2O + 1335 kJ/mol (8)
W ostatnich latach tę technologię katalityczną zaadaptowano do transportu ładunków i transportu morskiego, gdzie jako paliwo stosuje się produkty na bazie wysokowrzących frakcji ropy naftowej o stosunkowo wysokiej zawartości związków zawierających azot [13]. Wysoka aktywność korozyjna amoniaku stawia szczególne wymagania materiałom silników i układów paliwowych, a także jego czystości. W związku z tym stopy miedzi i niklu, w których zawartość miedzi i niklu przekracza 6%, nie mogą być stosowane w układach paliwowych, zbiornikach do ich przechowywania, jak również w przewodach doprowadzających paliwo. Tylko teflon nadaje się na uszczelki i izolacje w tego typu systemach. Ze względu na przyspieszone pękanie korozyjne stali, zwłaszcza w podwyższonych temperaturach, w obecności wilgoci i powietrza, maksymalna zawartość amoniaku nie powinna przekraczać 0,1% wag. i kilka milionowych. W związku z tym, aby zapewnić wymaganą czystość paliwa, konieczne jest stosowanie specjalnych technologii.
Jakie problemy można zidentyfikować przy przechodzeniu transportu na paliwo amoniakalne? Należą do nich przede wszystkim: a) problemy korozji, gdy elementy silnika mają kontakt z amoniakiem; b) wysoka toksyczność amoniaku; c) stosunkowo niska właściwa pojemność energetyczna amoniaku jako paliwa; d) powstawanie tlenków azotu z amoniaku podczas jego spalania. Warto zwrócić uwagę na perspektywy techniczne i ekonomiczne wykorzystania amoniaku jako paliwa silnikowego. Niższa wartość kaloryczna amoniaku w porównaniu z olejem napędowym jest w Rosji rekompensowana jego niskimi kosztami. Oznacza to, że amoniak jest już paliwem konkurencyjnym cenowo. W obecnych procesach syntezy amoniaku z gazu ziemnego nieuchronnie powstaje dwutlenek węgla – około 2,5 tony CO2 na 1 tonę amoniaku. Utylizacja skoncentrowanego CO2 na miejscu jest znacznie tańsza i technologicznie prostsza niż rozwiązanie tego problemu w przypadku pojazdu zasilanego pojedynczym paliwem węglowodorowym. Zastosowanie amoniaku w procesach technologicznych otwiera zatem możliwości stworzenia transportu bez śladu węglowego. Przewiduje się, że komercyjne wykorzystanie amoniaku w tym celu rozpocznie się w latach 2035–2037. Przewiduje się, że do 2050 roku w transporcie morskim będzie wykorzystywany przede wszystkim skroplony gaz ziemny (65–70%) i amoniak (20–25%). Udział oleju opałowego o niskiej zawartości siarki wyniesie zaledwie 10%. Doprowadzi to do konieczności podwojenia światowej produkcji amoniaku do 2050 r. – do 400 milionów ton rocznie.
Zastosowanie amoniaku w transporcie morskim i samochodowym nieuchronnie da impuls do rozwoju silników spalinowych. Silniki amoniakowe mogą znacząco różnić się od silników benzynowych lub wysokoprężnych. Być może amoniak nie będzie paliwem jednoskładnikowym i będzie wymagał wprowadzenia specjalnych dodatków (podobnych do dodatków zwiększających liczbę oktanową). Konieczność zwiększenia zdolności produkcyjnych amoniaku stymuluje postęp w zakresie nowych technologii jego syntezy. Doprowadzi to do zwiększenia badań naukowych w dziedzinie procesów katalitycznych związanych z syntezą amoniaku i przemysłowego zagospodarowywania wyników tych prac.
Praca została zrealizowana przy wsparciu finansowym Ministerstwa Nauki i Szkolnictwa Wyższego Federacji Rosyjskiej w ramach zadania państwowego Instytutu Katalizy SB RAN (projekt FWUR-2024-37).
energypolicy