Будущее аммиака как альтернативного моторного топлива
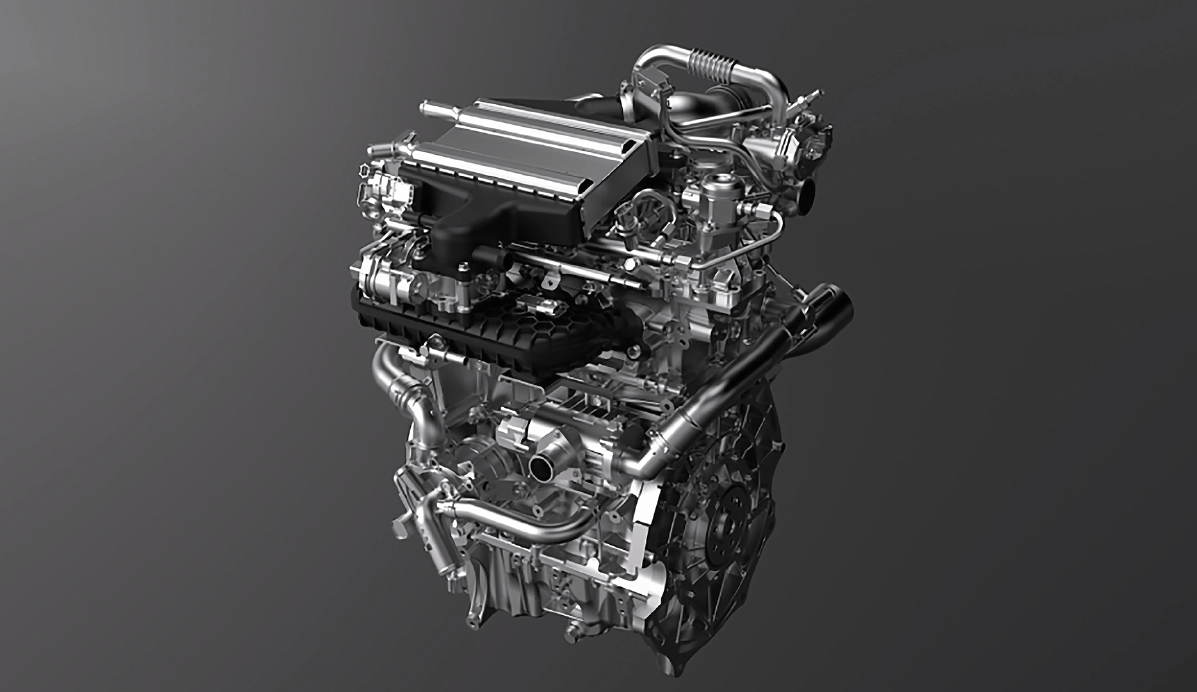
Один из самых великих химических процессов, созданных в XX в. – это синтез аммиака. Движущей силой в разработке этого процесса явилась необходимость обеспечения продовольствием растущего народонаселения на Земле. Единственным источником азотсодержащих минеральных удобрений в начале XX в. являлись запасы аммиачной селитры в Чили. Эти запасы стремительно убывали и, казалось, мог сбыться прогноз английского священника и ученого Томаса Мальтуса, который считал, что научно-технический прогресс не может компенсировать ограниченность природных ресурсов. В начале XX в. основным вызовом для ученых всего мира стала задача химической фиксации азота. Естественным путем решения этой задачи стал вариант связывания атмосферного азота в форме синтетического аммиака. Заслуга в разработке промышленного способа получения аммиака из азота и водорода принадлежит двум немецким ученым – Фрицу Габеру и Карлу Бошу. Ф. Габер впервые разработал способ получения аммиака в лабораторных условиях, а К. Бош создал инженерные основы промышленного процесса. Оба стали лауреатами Нобелевской премии: Ф. Габер – в 2019 г., а К. Бош – в 1931 г. Прошло уже более 100 лет, а все реакторы синтеза аммиака в мире строятся в соответствии с технологическими решениями, разработанными Карлом Бошем. В настоящее время мировое производство аммиака достигает 200 млн т в год. Это позволяет обеспечить азотными удобрениями основных сельхозпроизводителей (Китай, Индия, США, Россия). Ежегодные темпы прироста объема производства аммиака в последние годы не превышают 1,5%. Это указывает на стабильность рынка аммиака. Основным направлением использования аммиака до настоящего времени являлось производство минеральных удобрений и промышленных взрывчатых веществ.В последнее время началось стремительное развитие нового направления использования аммиака в качестве моторного топлива. В аммиаке содержится большая доля водорода, при его сгорании не выделяется углекислый газ, что делает его чистым и экологически безопасным топливом. Аммиак гораздо легче хранить и транспортировать, чем водород. И, наконец, аммиак это энергетически богатое топливо, с теплотворной способностью всего в 3 раза меньше, чем у бензина или дизельного топлива.
Анализ возможности использования аммиака в качестве моторного топлива стоит начать с рассмотрения его энергетических характеристик в сравнении с традиционными видами моторных топлив – бензина, дизельного топлива (ДТ) и природного газа (таблица 1).

Несколько энергетических и термодинамических характеристик аммиака весьма близки к традиционным топливам. Прежде всего, это температура и давление конденсации, что позволяет хранить аммиак и традиционные топлива в жидком состоянии (за исключением природного газа). Близкие значения у всех топлив, включая аммиак, и по максимальной (адиабатической) температуре горения – от 1800 до 2030 °C.Однако некоторые физические характеристики NH3 ограничивают его применение в двигателях. Так, величина объемной плотности энергии у NH3 заметно ниже по сравнению с традиционными углеводородными топливами (таблица 1). Это означает, что объем топлива (или резервуаров для его хранения), необходимый для генерирования того же количества энергии, при использовании NH3 увеличится в 2,5–3 раза. Кроме того, у NH3 гораздо более высокая температура самовоспламенения по сравнению с традиционными топливами. Поэтому для работы дизельного двигателя с аммиаком необходимы намного более высокие значения степени компрессии – как минимум 35:1 – по сравнению со значениями, применяемыми при работе с ДТ (от 14:1 до 22:1) [1]. Это налагает повышенные требования к прочности и коррозионной стойкости материалов, используемых для изготовления двигателей. Меньшая скорость распространения пламени при горении аммиака может приводить к нестабильности процесса горения.
В 2019–2020 гг. крупнейшие производители дизельных двигателей MAN Energy Solutions (Германия) и Wärtsilä (Финляндия) сообщили о начале разработки двух- и четырехтактных дизельных двигателей, работающих на аммиаке [2].Наибольшее внимание использованию аммиака как замены моторному топливу уделяется в секторе морского транспорта. Норвежская компания Yara анонсировала строительство первого в мире «безвыбросного» морского судна на «чистом аммиаке» без привлечения углеводородного топлива (мазута или дизельного топлива). Планируется, что это судно начнёт эксплуатироваться уже с 2026 г. на морских перевозках удобрений по маршруту «Норвегия – Германия».
В настоящее время для решения проблемы недостаточной эффективности сгорания аммиака в дизельных двигателях используют его смешение с небольшим количеством обычного дизельного топлива (т. н. «пилотное топливо»), которое инжектируется в топливную систему и инициирует горение аммиака [1]. Эксперименты, выполненные еще в 1977 г, показали, что из 4 основных топлив – метанола, этанола, метана и аммиака – аммиак меньше всего подходит для работы в дизельном двигателе даже в двухтопливном варианте [3]. Кроме существенных выбросов не полностью окисленного NH3 (до 0,5% об.), его использование приводило к максимальной задержке зажигания, наименьшей выходной мощности и эффективности по сравнению с другими видами топлив (таблица 2).

Тем не менее, после начала компании по снижению выбросов СО2 была показана принципиальная применимость двухтопливой схемы «аммиак + дизельное топливо» для многоцилиндровых дизельных двигателей с турбонаддувом. При этом требовалась только незначительная модификация системы впуска топлива для подвода линии подачи аммиака, в то время как система инжектирования углеводородного топлива оставалась неизменной [4]. Стабильная работа двигателя была возможна при замене до 95% (по энергии) дизельного топлива на NH3, а значимая экономия топлива (наибольшая эффективность работы) получалась при доле аммиака в топливе 40–60%. При содержании NH3 ниже 60% наблюдалось значительное уменьшение выбросов NOx, которое авторы отнесли к снижению температуры пламени. Однако из-за этого снижалась полнота сгорания дизельного топлива, проявлявшаяся через увеличение выбросов углеводородов. Более детальные исследования, выполненные позднее [5], показали, что при содержании аммиака выше 60% возрастала задержка поджига топлива. В то же время, при увеличении доли дизельного топлива выше 60% при работе двигателя на постоянной мощности состав смеси «аммиак – воздух» в двигателе может достичь пределов взрывоопасности, а снижение температуры горения уменьшало эффективность сжигания топлива в целом.Другая немаловажная проблема, которая должна быть решена при использовании аммиака в двухтопливных схемах, связана с системой для его подачи в камеру сгорания. Так, аммиак может впрыскиваться во впускной клапан (при этом получают гомогенные смеси топлива с воздухом) или подаваться непосредственно в цилиндр в жидком виде. Последний вариант более предпочтителен, поскольку позволяет осуществлять дозирование аммиака непосредственно из резервуаров для хранения в жидком виде (при давлении около 17 атм.) без предварительного испарения. При дозировании жидкости можно значительно увеличить давление в камере сгорания. Однако из-за высокого значения давления насыщенных паров и сильной зависимости давления насыщенных паров от температуры, для аммиака характерно мгновенное закипание и испарение при снижении давления. Этот эффект особенно сильно проявляется во впускных форсунках и существенно изменяет закономерности формирования газовоздушных смесей, приводя в отдельных случаях к плохому перемешиванию топлива с воздухом и более глубокому проникновению жидкости в двигатель, вплоть до смачивания ею стенок [6]. Также при жидкостном вводе резкое снижение температуры при испарении аммиака значительно снижает стабильность пламени. Для уменьшения такого негативного эффекта предлагают предварительный подогрев и турбулизацию потока воздуха, подаваемого в камеру сгорания. В целом в данном направлении требуются дополнительные исследования для понимания особенностей процессов формирования смесей аммиака с воздухом и их горения в двигателях внутреннего сгорания, а также разработки оптимальных режимов подачи топлива.
В компании MAN Energy Solutions система для дозирования аммиака создается на основе аналогичных систем, разработанных ранее для сжиженных углеводородных газов и метанола. Было анонсировано, что в случае успешного завершения в 2023 г. пилотных испытаний, первый двухтактный двигатель, работающий на аммиаке, будет установлен на промышленное судно в 2024 г. [7]. Wärtsilä Corporation в конце 2023 г. заявила о выпуске первого промышленного четырехтактного двигателя, работающего на смеси дизеля с аммиаком [8], а в начале 2024 г. – о наличии у нее системы подачи аммиака, работающей как с жидким, так и газообразным сырьем [9]. Предположительно, они будут установлены в 2025 г. на среднеразмерные танкеры-газовозы, специально строящиеся с этой целью на верфях Hyundai Mipo в Южной Корее для компании EXMAR LPG.
Активно исследуется также возможность задействования аммиака в автомобильном транспорте. Эти работы ведутся по 2 направлениям. Во-первых, аммиак применяется как энергоноситель для топливных элементов, питающих электродвигатель автомобиля. Другой вариант использования аммиака – прямая замена им бензина или дизельного топлива в двигателе внутреннего сгорания. Первый такой двигатель уже продемонстрирован в 2023 г. альянсом компаний GAC (Китай) и Toyota (Япония) [10]. Однако основным направлением использования аммиака в автомобильном транспорте являются технологии, основанные на применении аммиачных топливных элементов в качестве источников энергии. Прежде всего, это более эффективный метод извлечения энергии из аммиака, характеризуемый меньшими выбросами NH3 и оксидов азота, а также низким шумом [2]. Собственно топливные элементы занимают значительно меньше пространства, чем двигатели внутреннего сгорания. Наиболее перспективными считаются топливные элементы с протонообменной мембраной (PEMFC), а также твердооксидные топливные элементы (SOFC) [11]. Опытные образцы PEMFC (но без использования аммиака в качестве источника Н2) уже применяют в наземном транспорте. Необходимое для их функционирования вспомогательное оборудование (системы охлаждения, вентиляции, подачи топлива и др.) примерно такое же, что и для обычного двигателя. Основная проблема при переходе на аммиак в топливных элементах PEMFC – чистота Н2 должна быть не ниже > 99,5% при полном отсутствии следов NH3. Топливные элементы SOFC могут использовать аммиак в качестве топлива без предварительного разложения и выделения Н2, что позволяет достигать более высоких значений мощности с единицы веса топлива. Однако для топливных элементов SOFC необходимо использовать систему хранения энергии для компенсации медленных процессов во время переходных режимов и обеспечения их энергией в пусковых режимах.Использование аммиака как энергоносителя не ограничивается только транспортом. Интенсивно проводятся исследования по замене углеводородного топлива на аммиак в газовых турбинах. Для снижения углеродного следа в тепловой энергетике разрабатывается процесс совместимого сжигания каменного угля и аммиака.
Большинство публикаций о топливно-энергетическом использовании аммиака носит преимущественно рекламный характер и сводится, в лучшем случае, к оценке снижения выбросов углекислого газа. Экспериментальные данные по содержанию других соединений в выхлопных газах двигателей внутреннего сгорания, как правило, не приводятся. Однако при сжигании аммиака наряду с экологически безопасным азотом возможно образование различных форм оксидов азота (NO, NO2, N2O):
2NH3 + 3/2O2 = N2+ 3H2O + 634 Кдж/моль (1)2NH3 + 2O2 = N2O + 3H2O + 552 Кдж/моль (2)2NH3 + 5/2O2 = 2NO + 3H2O + 453 Кдж/моль (3)
2NO + O2 = 2NO2–113 Кдж/моль (4)
Их содержание в продуктах горения может достигать 0,28% об. Кроме того, из-за низкой эффективности сгорания аммиака, его остаточная концентрация в выхлопах даже при оптимальных режимах горения составляет 0,1–0,3% об. [12]. Даже при малых концентрациях в воздухе (0,0005–0,005% об.) NH3 вызывает раздражение глаз и дыхательных путей, а при содержании ~1% об. наступает мгновенная смерть. Выбросы оксидов азота способствуют образованию фотохимического смога и «кислотных дождей», разложению озонового слоя. Летальной считается концентрация NO2, образующегося из NO при комнатной температуре, свыше 0,02% об. Увеличения эффективности сгорания NH3 и снижения выбросов NO и NO2 достигают благодаря предварительному подогреву топлива, а также дополнительному подъему давления в камере сгорания (последнее и так выше, чем при работе с ДТ).Хорошей альтернативой небезопасному и дорогостоящему повышению давления или температуры может стать использование промышленной технологии снижения выбросов оксидов азота на основе их селективного каталитического восстановления аммиаком (СКВ NH3) до азота и воды на основе следующих реакций:
6NO + 4NH3 → 5 N2 + 6H2O + 1095 Кдж/моль (5)4NO + 4NH3 + O2 → 4N2 + 6H2O + 1629 Кдж/моль (6)6NO2 + 8NH3 → 7N2 + 12H2O + 2737 Кдж/моль (7)
2NO2 + 4NH3 + O2 → 3 N2 + 6H2O + 1335 Кдж/моль (8)
В последние годы такая каталитическая технология адаптирована для грузового и морского транспортов, где в качестве топлива используются продукты на основе высококипящих нефтяных фракций с относительно высоким содержанием азотсодержащих соединений [13].Высокая коррозионная активность аммиака выдвигает особые требования к материалам для двигателей и систем подачи топлива, а также его чистоте. Так, любые сплавы с медью и никелем при содержании последнего выше 6% не могут быть использованы в топливных системах, сосудах для его хранения, а также линиях его подачи. Для уплотнений/прокладок и изоляции в таких системах годится только тефлон. Из-за ускоренного коррозионного растрескивания стали под напряжением, особенно при повышенных температурах, в присутствии влаги и воздуха их предельное содержание в аммиаке не должно превышать 0,1% вес. и несколько миллионных долей. Соответственно, необходимы специальные технологии, обеспечивающие необходимую чистоту топлива.
Какие проблемы можно выделить на пути перехода транспорта на аммиачное топливо? Это, прежде всего:а) проблемы коррозии при контакте элементов двигателя с аммиаком;б) высокая токсичность аммиака;в) относительно низкая удельная энергоемкость аммиака как топлива;г) образование оксидов азота из аммиака при его сжигании.Стоит обратить внимание на технико-экономические перспективы аммиака как моторного топлива. Меньшая теплотворная способность аммиака по сравнению с ДТ почти компенсируется его низкой стоимостью в России. Значит, аммиак в стоимостном отношении уже конкурентоспособен как топливо. В существующих процессах синтеза аммиака из природного газа неизбежно образуется углекислый газ – примерно 2,5 т СО2 на 1 т аммиака. Утилизация концентрированного СО2 на месте существенно дешевле и технологически проще, чем решение этой задачи для отдельно взятого автомобиля на углеводородном топливе. Таким образом, привлечение аммиака в технологические процессы открывает возможности создания транспорта без углеродного следа.Коммерческое использование аммиака в этом качестве прогнозируется, начиная с 2035–2037 гг. Ожидается, что к 2050 г. морской транспорт будет использовать преимущественно сжиженный природный газ (65–70%) и аммиак (20–25%). Доля малосернистого мазута будет составлять всего 10%. Это приведет к необходимости увеличения к 2050 г. мирового производства аммиака в 2 раза – до 400 млн т/год.
Применение аммиака в морском и автомобильном транспортах неизбежно придаст импульс развитию двигателей внутреннего сгорания. Двигатели на аммиаке могут быть совсем другими, в отличии от бензиновых или дизельных двигателей. Возможно, аммиак не будет монотопливом и потребует введения специальных добавок (по аналогии с октаноповышающими добавками). Необходимость увеличения мощностей производства аммиака стимулирует прогресс в новых технологиях его синтеза. Это вызовет рост научных исследований в области каталитических процессов, связанных с синтезом аммиака, и промышленное освоение результатов этих работ.
Paбoта выполнена при финансовой поддержке Министерства науки и высшего образования РФ в рамках государственного задания Института катализа СО РАН (проект FWUR-2024-37).
energypolicy