Alternatif Motor Yakıtı Olarak Amonyağın Geleceği
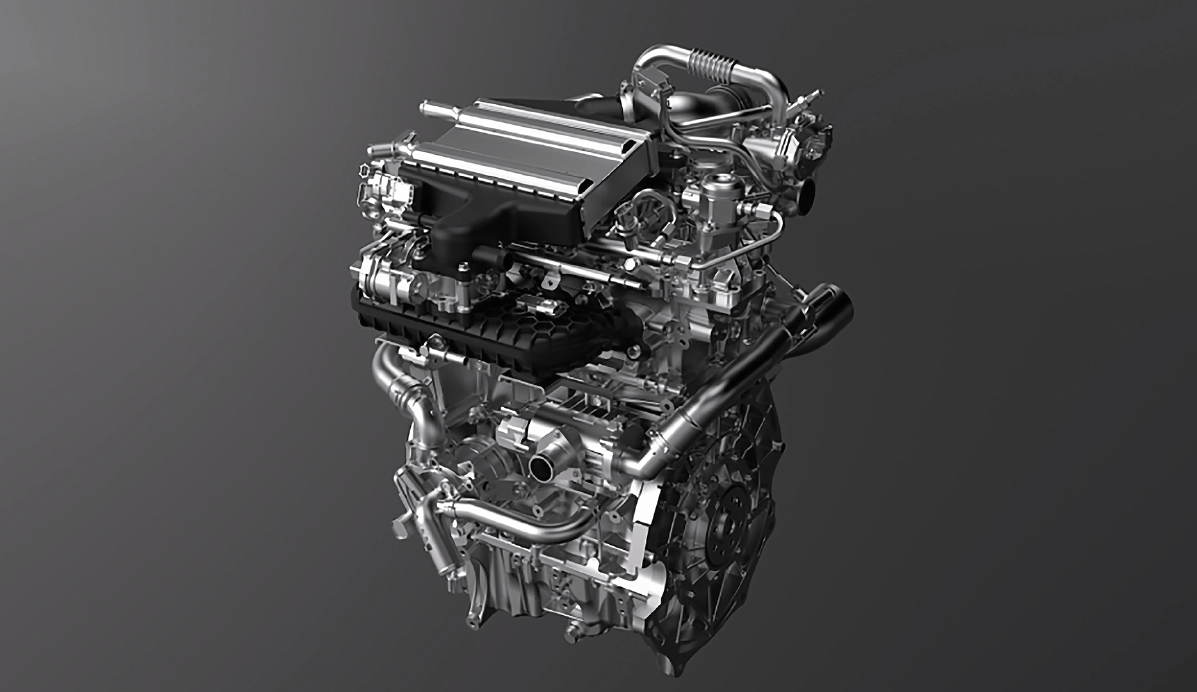
20. yüzyılın en büyük kimyasal işlemlerinden biri. - Bu amonyağın sentezidir. Bu sürecin gelişmesinin ardındaki itici güç, Dünya'daki artan nüfusa yiyecek sağlama ihtiyacıydı. 20. yüzyılın başlarında azot içerikli mineral gübrelerin tek kaynağı. Şili'deki amonyum nitrat rezervleri hangileridir? Bu rezervler hızla tükeniyordu ve bilimsel ve teknolojik ilerlemenin sınırlı doğal kaynakları telafi edemeyeceğine inanan İngiliz rahip ve bilim adamı Thomas Malthus'un kehanetinin gerçekleşeceği görülüyordu. 20. yüzyılın başlarında. Dünya çapında bilim insanlarının karşılaştığı en büyük zorluk kimyasal azot fiksasyonu sorunu olmuştur. Bu sorunu çözmenin doğal bir yolu, havadaki azotu sentetik amonyak formunda bağlamaktı. Azot ve hidrojenden amonyak üretmeye yönelik endüstriyel bir yöntemi geliştiren iki Alman bilim insanı Fritz Haber ve Carl Bosch'tur. F. Haber laboratuvar koşullarında amonyak üretme yöntemini ilk geliştiren kişi oldu ve K. Bosch endüstriyel sürecin mühendislik temellerini oluşturdu. İkisi de Nobel Ödülü sahibi oldu: F. Haber 2019'da, K. Bosch ise 1931'de. 100 yıldan fazla zaman geçti ve dünyadaki tüm amonyak sentez reaktörleri Carl Bosch'un geliştirdiği teknolojik çözümlere uygun olarak inşa ediliyor. Günümüzde dünya çapında amonyak üretimi yıllık 200 milyon tonu bulmaktadır. Bu sayede büyük tarım üreticilerine (Çin, Hindistan, ABD, Rusya) azotlu gübre temini mümkün olmaktadır. Son yıllarda amonyak üretiminin yıllık büyüme hızı %1,5'i geçmemiştir. Bu durum amonyak piyasasında istikrarın sağlandığını gösteriyor. Amonyak kullanımının bugüne kadarki başlıca alanı mineral gübre ve endüstriyel patlayıcı üretimi olmuştur. Son zamanlarda amonyağın motor yakıtı olarak kullanımına ilişkin yeni bir alan hızla gelişmeye başlamıştır. Amonyak, yüksek oranda hidrojen içerir ve yakıldığında karbondioksit salınımı yapmaz, bu da onu temiz ve çevre dostu bir yakıt haline getirir. Amonyağın depolanması ve taşınması hidrojene göre çok daha kolaydır. Son olarak amonyak, kalorifik değeri benzin veya dizel yakıtından sadece 3 kat daha düşük olan enerji açısından zengin bir yakıttır.
Amonyağın motor yakıtı olarak kullanılma olasılığının analizi, enerji özelliklerinin geleneksel motor yakıt türleriyle (benzin, dizel yakıtı (DF) ve doğal gaz) karşılaştırılmasıyla başlamalıdır (Tablo 1).

Amonyağın birçok enerji ve termodinamik özelliği geleneksel yakıtlara çok yakındır. Öncelikle amonyağın ve geleneksel yakıtların (doğal gaz hariç) sıvı halde depolanmasını sağlayan, yoğunlaşma sıcaklığı ve basıncıdır. Amonyak da dahil olmak üzere tüm yakıtların maksimum (adiabatik) yanma sıcaklığı değerleri benzerdir - 1800 ila 2030 °C. Ancak NH3'ün bazı fiziksel özellikleri motorlarda kullanımını sınırlamaktadır. Bu nedenle NH3’ün hacimsel enerji yoğunluğu değeri geleneksel hidrokarbon yakıtlara kıyasla önemli ölçüde düşüktür (Tablo 1). Bu, aynı miktarda enerjiyi NH3 kullanarak üretmek için gereken yakıt hacminin (veya depolama tanklarının) 2,5-3 kat artacağı anlamına geliyor. Ayrıca NH3'ün geleneksel yakıtlara kıyasla çok daha yüksek bir kendiliğinden tutuşma sıcaklığı vardır. Bu nedenle, bir dizel motorunun amonyakla çalışabilmesi için, dizel yakıtla çalışırken kullanılan değerlere (14:1 ila 22:1) kıyasla çok daha yüksek sıkıştırma oranlarına (en az 35:1) ihtiyaç duyulmaktadır [1]. Bu durum, motor üretiminde kullanılan malzemelerin dayanıklılığı ve korozyon direncine yönelik talepleri artırıyor. Amonyağın yanması sırasında alev yayılma hızının düşük olması yanma sürecinin kararsızlığına yol açabilir.
2019-2020'de Dizel motorların en büyük üreticileri MAN Energy Solutions (Almanya) ve Wärtsilä (Finlandiya), amonyakla çalışan iki ve dört zamanlı dizel motorların geliştirilmesine başladıklarını duyurdular [2]. Amonyağın motor yakıtı yerine kullanılmasına en fazla dikkat deniz taşımacılığı sektöründe verilmektedir. Norveçli Yara şirketi, hidrokarbon yakıtlar (fuel oil veya dizel yakıt) kullanmadan "saf amonyakla" çalışan dünyanın ilk "sıfır emisyonlu" deniz aracının inşasını duyurdu. Bu geminin 2026 yılı başından itibaren Norveç-Almanya güzergahında gübrelerin deniz yoluyla taşınmasında kullanılmaya başlanması planlanıyor.
Günümüzde dizel motorlarda amonyağın yetersiz yanma verimi sorununu çözmek için, amonyak az miktarda normal dizel yakıtı (sözde “pilot yakıt”) ile karıştırılarak yakıt sistemine enjekte edilmekte ve amonyağın yanması başlatılmaktadır [1]. 1977 yılında yapılan deneyler, dört ana yakıttan (metanol, etanol, metan ve amonyak) amonyağın, çift yakıtlı versiyonda bile dizel motorda çalışmaya en az uygun olanı olduğunu göstermiştir [3]. Eksik oksitlenmiş NH3'ün (hacimce %0,5'e kadar) önemli emisyonlarına ek olarak, kullanımı diğer yakıtlara kıyasla en uzun tutuşma gecikmesi, en düşük güç çıkışı ve verimlilikle sonuçlandı (Tablo 2).

Ancak CO2 emisyonlarının azaltılması kampanyasının başlamasının ardından, amonyak + dizel çift yakıt şemasının çok silindirli turboşarjlı dizel motorlar için temel uygulanabilirliği kanıtlandı. Bu, amonyak besleme hattını yerleştirmek için yakıt giriş sisteminde yalnızca küçük bir değişiklik gerektirdi, hidrokarbon yakıt enjeksiyon sistemi ise değişmeden kaldı [4]. Dizel yakıtının %95'e kadar (enerji açısından) NH3 ile değiştirilmesiyle motorun kararlı çalışması mümkün olmuş ve yakıttaki %40-60'lık amonyak oranıyla önemli yakıt tasarrufları (en yüksek çalışma verimliliği) sağlanmıştır. NH3 içeriğinin %60'ın altına düşmesi durumunda, NOx emisyonlarında önemli bir azalma gözlemlendi; yazarlar bunu alev sıcaklığındaki azalmaya bağladılar. Ancak bu durum dizel yakıtının yanmasının tamlığında azalmaya yol açtı ve bu durum hidrokarbon emisyonlarının artmasıyla kendini gösterdi. Daha sonra yapılan daha detaylı çalışmalar [5], amonyak içeriği %60'ın üzerinde olduğunda yakıt tutuşmasındaki gecikmenin arttığını göstermiştir. Aynı zamanda, motor sabit güçte çalışırken dizel yakıt oranı %60'ın üzerine çıktığında, motordaki amonyak-hava karışımının bileşimi patlayıcı sınırlara ulaşabilmekte ve yanma sıcaklığının düşmesi yakıtın genel yanma verimini düşürmektedir. Çift yakıtlı sistemlerde amonyağın kullanımında çözülmesi gereken bir diğer önemli problem ise amonyağın yanma odasına beslenme sistemiyle ilgilidir. Böylece amonyak emme supabına enjekte edilebilir (bu, yakıt ve havanın homojen bir şekilde karışmasını sağlar) veya doğrudan sıvı halde silindire beslenebilir. İkinci seçenek tercih edilir, çünkü amonyağın doğrudan depolama tanklarından sıvı formda (yaklaşık 17 atm basınçta) ön buharlaştırmaya gerek kalmadan dozajlanmasına olanak tanır. Sıvının dozlanmasıyla yanma odasındaki basınç önemli ölçüde artırılabilir. Ancak doymuş buhar basıncının yüksek değerde olması ve doymuş buhar basıncının sıcaklığa güçlü bağımlılığı nedeniyle amonyak, basınç azaldığında ani kaynama ve buharlaşma özelliği gösterir. Bu etki özellikle emme nozullarında belirgindir ve gaz-hava karışımlarının oluşum modellerini önemli ölçüde değiştirir, bazı durumlarda yakıtın hava ile kötü karışmasına ve sıvının motora daha derin nüfuz etmesine, hatta duvarların ıslanmasına yol açar [6]. Ayrıca sıvı enjeksiyonunda amonyağın buharlaşması sırasında sıcaklığın ani düşmesi alev kararlılığını önemli ölçüde azaltmaktadır. Bu olumsuz etkiyi azaltmak için yanma odasına verilen hava akışının ön ısıtılması ve türbülanslanması önerilmektedir. Genel olarak, içten yanmalı motorlarda amonyak-hava karışımlarının oluşumu ve yanma süreçlerinin özelliklerini anlamak ve optimum yakıt besleme modlarının geliştirilmesi için bu alanda ilave araştırmalara ihtiyaç duyulmaktadır.
MAN Energy Solutions'da amonyak dozajlama sistemi, daha önce sıvılaştırılmış petrol gazları ve metanol için geliştirilen benzer sistemlere dayanmaktadır. 2023 yılında pilot testlerin başarıyla tamamlanması halinde, 2024 yılında ilk iki zamanlı amonyakla çalışan motorun bir endüstriyel gemiye yerleştirileceği duyuruldu [7]. Wärtsilä Corporation, 2023'ün sonlarında dizel ve amonyak karışımıyla çalışan ilk endüstriyel dört zamanlı motoru piyasaya sürdüğünü duyurdu [8] ve 2024'ün başlarında hem sıvı hem de gaz hammaddeleriyle çalışabilen bir amonyak tedarik sistemine sahip olduğunu duyurdu [9]. Güney Kore'deki Hyundai Mipo tersanelerinde EXMAR LPG için özel olarak bu amaçla inşa edilen orta büyüklükteki LNG gemilerine 2025 yılında takılması bekleniyor.
Amonyağın motorlu taşıtlarda da kullanılma imkânı aktif olarak araştırılıyor. Bu çalışmalar iki yönlü yürütülmektedir. Öncelikle amonyak, bir aracın elektrik motorunu çalıştıran yakıt hücrelerinde enerji taşıyıcısı olarak kullanılır. Amonyağın bir diğer kullanım alanı ise içten yanmalı motorlarda benzin veya dizel yakıtının doğrudan yerine kullanılmasıdır. Bu tür motorların ilki 2023 yılında GAC (Çin) ve Toyota (Japonya) ittifakı tarafından gösterildi [10]. Ancak amonyağın motorlu taşıtlarda asıl kullanım alanı, amonyak yakıt hücrelerinin enerji kaynağı olarak kullanılmasına dayalı teknolojilerdir. Öncelikle, daha düşük NH3 ve azot oksit emisyonları ve düşük gürültü ile karakterize edilen, amonyaktan enerji elde etmenin daha verimli bir yöntemidir [2]. Yakıt hücreleri içten yanmalı motorlara göre çok daha az yer kaplar. En umut verici olanlar proton değişim membranlı yakıt hücreleri (PEMFC) ve katı oksit yakıt hücreleridir (SOFC) [11]. PEMFC'nin prototipleri (ancak H2 kaynağı olarak amonyak kullanılmadan) halihazırda kara taşımacılığında kullanılıyor. Çalışmaları için ihtiyaç duyulan yardımcı ekipmanlar (soğutma sistemleri, havalandırma, yakıt temini vb.) konvansiyonel bir motordakilerle hemen hemen aynıdır. PEMFC yakıt hücrelerinde amonyağa geçişte karşılaşılan temel sorun, H2 saflığının %99,5'in altında olmaması ve NH3 izlerinin tamamen yok olmasıdır. SOFC yakıt hücreleri, amonyağı önceden ayrıştırılmadan ve H2 emisyonu olmadan yakıt olarak kullanabildiğinden, birim yakıt ağırlığı başına daha yüksek güç değerlerinin elde edilmesine olanak sağlamaktadır. Ancak, SOFC yakıt hücrelerinin, geçici koşullar sırasında yavaş süreçleri telafi etmek ve başlatma koşulları sırasında onlara enerji sağlamak için bir enerji depolama sistemine ihtiyacı vardır. Amonyağın enerji taşıyıcısı olarak kullanımı sadece taşımacılıkla sınırlı değildir. Gaz türbinlerinde hidrokarbon yakıtların amonyak ile değiştirilmesi konusunda yoğun araştırmalar yürütülüyor. Termik santrallerde karbon ayak izini azaltmak amacıyla kömür ve amonyağın uyumlu yanması için bir proses geliştiriliyor.
Amonyağın yakıt ve enerji kullanımına ilişkin yayınların çoğu esas olarak tanıtım amaçlıdır ve en iyi ihtimalle karbondioksit emisyonlarındaki azalmanın değerlendirilmesiyle sınırlıdır. İçten yanmalı motorların egzoz gazlarındaki diğer bileşiklerin içeriğine ilişkin deneysel veriler genellikle sunulmamaktadır. Ancak amonyağın çevre dostu azotla birlikte yakılması durumunda çeşitli azot oksit formları (NO, NO2, N2O) oluşabilir:
2NH3 + 3/2O2 = N2+ 3H2O + 634 kJ/mol (1)2NH3 + 2O2 = N2O + 3H2O + 552 kJ/mol (2)2NH3 + 5/2O2 = 2NO + 3H2O + 453 kJ/mol (3)
2NO + O2 = 2NO2–113 kJ/mol (4)
Yanma ürünlerindeki oranları hacimce %0,28'e kadar çıkabilmektedir. Ayrıca amonyağın yanma veriminin düşük olması nedeniyle, optimum yanma koşulları altında bile egzoz gazlarındaki kalıntı konsantrasyonu hacimce %0,1-0,3 arasındadır. [12]. Havadaki düşük konsantrasyonlarda bile (%0,0005-0,005 hacim) NH3 gözlerde ve solunum yollarında tahrişe neden olur ve hacimce yaklaşık %1 oranındaki bir içerikte anında ölüm gerçekleşir. Azot oksit emisyonları fotokimyasal sis ve asit yağmurlarının oluşumuna ve ozon tabakasının parçalanmasına neden olur. Oda sıcaklığında NO'dan oluşan NO2 konsantrasyonu hacimce %0,02'den fazladır. öldürücü olduğu düşünülüyor. Yakıtın önceden ısıtılması ve ayrıca yanma odasındaki basıncın (ikincisi dizel yakıtla çalışmaya göre daha yüksektir) ayrıca artırılmasıyla, NH3 yanmasının verimi artırılır ve NO ve NO2 emisyonları azaltılır. Basınç veya sıcaklıktaki güvenli olmayan ve pahalı artışlara iyi bir alternatif, azot oksit emisyonlarını azaltmak için, amonyak (SCR NH3) ile azot ve suya seçici katalitik indirgeme temelinde aşağıdaki reaksiyonlara dayanan endüstriyel teknolojinin kullanılması olabilir:
6NO + 4NH3 → 5 N2 + 6H2O + 1095 kJ/mol (5)4NO + 4NH3 + O2 → 4N2 + 6H2O + 1629 kJ/mol (6)6NO2 + 8NH3 → 7N2 + 12H2O + 2737 kJ/mol (7)
2NO2 + 4NH3 + O2 → 3 N2 + 6H2O + 1335 kJ/mol (8)
Son yıllarda bu katalitik teknoloji, yüksek kaynama noktalı petrol fraksiyonlarına dayalı ürünlerin, nispeten yüksek oranda azot içeren bileşiklere sahip olarak yakıt olarak kullanıldığı kargo ve deniz taşımacılığına uyarlanmıştır [13]. Amonyağın yüksek korozif aktivitesi, motorlar ve yakıt besleme sistemleri için kullanılan malzemeler ve saflığı konusunda özel talepler doğurur. Bu nedenle, bakır ve nikel içeriği %6'nın üzerinde olan herhangi bir alaşım, yakıt sistemlerinde, depolama tanklarında ve besleme hatlarında kullanılamaz. Bu sistemlerde conta ve izolasyon olarak sadece Teflon uygundur. Çeliklerin özellikle yüksek sıcaklıklarda, nem ve havanın varlığında, stres korozyon çatlamasının hızlanması nedeniyle, amonyak içeriklerinin ağırlıkça maksimum %0,1'i geçmemesi gerekir. ve birkaç milyonuncu. Bu nedenle gerekli yakıt saflığının sağlanması için özel teknolojilere ihtiyaç duyulmaktadır.
Taşımacılığın amonyak yakıtına geçişinde hangi sorunlar tespit edilebilir? Bunlar öncelikle şunlardır: a) Motor elemanlarının amonyakla teması sonucu oluşan korozyon sorunları; b) Amonyağın yüksek toksisitesi; c) amonyağın yakıt olarak nispeten düşük özgül enerji kapasitesi; d) Amonyağın yanması sırasında azot oksitlerinin oluşması. Amonyağın motor yakıtı olarak teknik ve ekonomik beklentilerine dikkat etmek gerekir. Amonyağın ısıl değerinin dizel yakıtına göre düşük olması, Rusya'da maliyetinin düşük olmasıyla neredeyse telafi ediliyor. Bu, amonyağın yakıt olarak maliyet açısından zaten rekabetçi olduğu anlamına geliyor. Doğal gazdan amonyak sentezleme proseslerinde kaçınılmaz olarak karbondioksit oluşur; 1 ton amonyak başına yaklaşık 2,5 ton CO2. Yoğunlaştırılmış CO2'nin yerinde bertarafı, bu sorunu tek bir hidrokarbon yakıtlı araç için çözmekten önemli ölçüde daha ucuz ve teknolojik olarak daha basittir. Bu sayede amonyağın teknolojik süreçlerde kullanımı, karbon ayak izi bırakmayan bir taşımacılık yaratma imkânı yaratıyor. Amonyağın bu amaçla ticari kullanımının 2035-2037 yılları arasında başlaması öngörülüyor. 2050 yılına gelindiğinde deniz taşımacılığında ağırlıklı olarak sıvılaştırılmış doğal gaz (%65-70) ve amonyak (%20-25) kullanılması bekleniyor. Düşük kükürtlü yakıt yağının payı ise sadece yüzde 10 olacak. Bu durum, 2050 yılına kadar küresel amonyak üretiminin iki katına, yani yılda 400 milyon tona çıkarılması ihtiyacını doğuracaktır.
Amonyağın deniz ve otomotiv taşımacılığında kullanılması kaçınılmaz olarak içten yanmalı motorların gelişimine ivme kazandıracaktır. Amonyaklı motorlar benzinli veya dizel motorlardan oldukça farklı olabilir. Belki de amonyak tek yakıt olmayacak ve özel katkı maddelerinin (oktan artırıcı katkı maddelerine benzer) kullanılması gerekecektir. Amonyak üretim kapasitesinin artırılması ihtiyacı, amonyak sentezine yönelik yeni teknolojilerin geliştirilmesine ivme kazandırıyor. Bu durum, amonyak sentezi ile ilişkili katalitik prosesler alanında bilimsel araştırmaların artmasına ve bu çalışmalardan elde edilen sonuçların endüstriyel olarak geliştirilmesine yol açacaktır.
Çalışma, Rusya Federasyonu Bilim ve Yüksek Öğrenim Bakanlığı'nın mali desteğiyle, SB RAS Kataliz Enstitüsü'nün devlet tahsisi (proje FWUR-2024-37) kapsamında yürütülmüştür.
energypolicy