Die Zukunft von Ammoniak als alternativer Kraftstoff
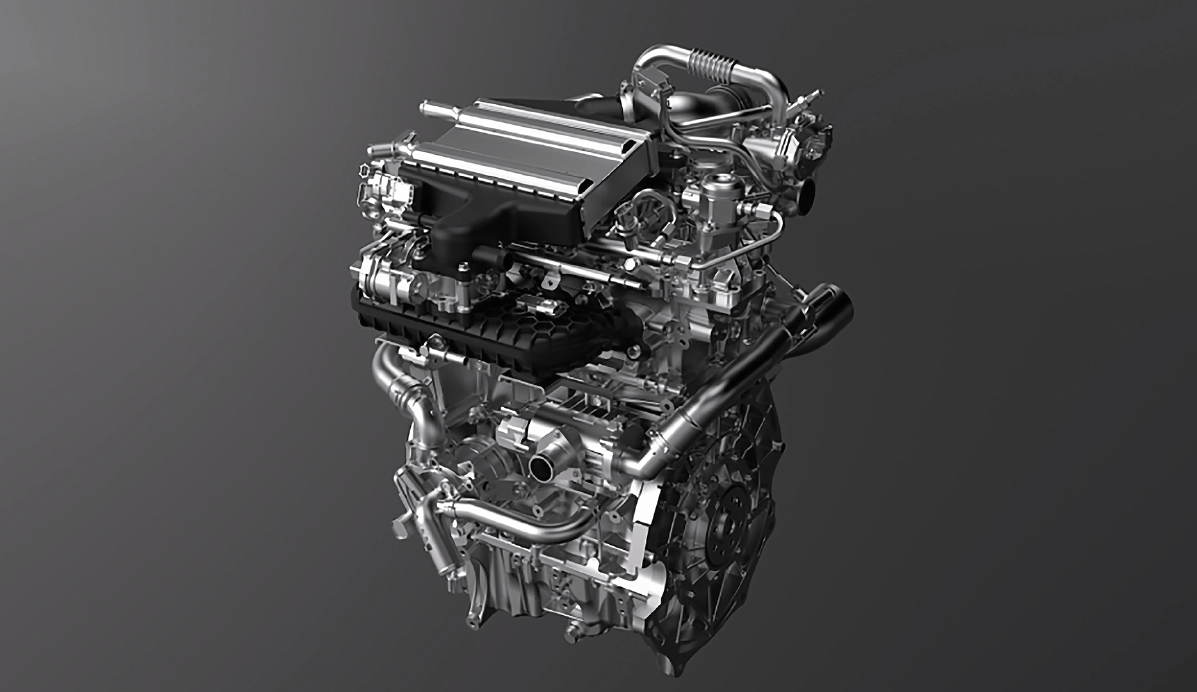
Einer der größten chemischen Prozesse des 20. Jahrhunderts. - das ist die Synthese von Ammoniak. Die treibende Kraft hinter der Entwicklung dieses Verfahrens war die Notwendigkeit, die wachsende Weltbevölkerung mit Nahrungsmitteln zu versorgen. Die einzige Quelle stickstoffhaltiger Mineraldünger zu Beginn des 20. Jahrhunderts. waren die Ammoniumnitratreserven in Chile. Diese Reserven erschöpften sich rasch und es schien, als ob sich die Vorhersage des englischen Priesters und Wissenschaftlers Thomas Malthus bewahrheiten könnte, der glaubte, dass der wissenschaftliche und technologische Fortschritt die begrenzten natürlichen Ressourcen nicht ausgleichen könne. Zu Beginn des 20. Jahrhunderts. Die größte Herausforderung für Wissenschaftler auf der ganzen Welt ist das Problem der chemischen Stickstofffixierung. Eine natürliche Möglichkeit, dieses Problem zu lösen, bestand darin, atmosphärischen Stickstoff in Form von synthetischem Ammoniak zu binden. Das Verdienst für die Entwicklung eines industriellen Verfahrens zur Herstellung von Ammoniak aus Stickstoff und Wasserstoff gebührt zwei deutschen Wissenschaftlern – Fritz Haber und Carl Bosch. F. Haber entwickelte als erster ein Verfahren zur Herstellung von Ammoniak unter Laborbedingungen und K. Bosch schuf die technischen Grundlagen des industriellen Prozesses. Beide wurden Nobelpreisträger: F. Haber im Jahr 2019 und K. Bosch im Jahr 1931. Mehr als 100 Jahre sind vergangen und alle Ammoniaksynthesereaktoren der Welt werden gemäß den von Carl Bosch entwickelten technologischen Lösungen gebaut. Derzeit beträgt die weltweite Ammoniakproduktion 200 Millionen Tonnen pro Jahr. Dadurch ist es möglich, große Agrarproduzenten (China, Indien, USA, Russland) mit Stickstoffdünger zu versorgen. Die jährliche Wachstumsrate der Ammoniakproduktion lag in den letzten Jahren nicht über 1,5 %. Dies deutet auf Stabilität auf dem Ammoniakmarkt hin. Haupteinsatzgebiet von Ammoniak ist bislang die Herstellung von Mineraldünger und Industriesprengstoffen. In jüngster Zeit hat sich ein neuer Bereich der Verwendung von Ammoniak als Kraftstoff rasch entwickelt. Ammoniak enthält einen großen Anteil Wasserstoff und setzt bei der Verbrennung kein Kohlendioxid frei, was es zu einem sauberen und umweltfreundlichen Brennstoff macht. Ammoniak lässt sich viel einfacher lagern und transportieren als Wasserstoff. Schließlich ist Ammoniak ein energiereicher Kraftstoff, dessen Heizwert nur dreimal niedriger ist als der von Benzin oder Dieselkraftstoff.
Eine Analyse der Verwendungsmöglichkeiten von Ammoniak als Kraftstoff sollte mit einer Untersuchung seiner Energieeigenschaften im Vergleich zu herkömmlichen Kraftstoffarten – Benzin, Dieselkraftstoff (DF) und Erdgas (Tabelle 1) – beginnen.

Mehrere energetische und thermodynamische Eigenschaften von Ammoniak ähneln stark denen herkömmlicher Brennstoffe. Vor allem sind es die Temperatur und der Druck der Kondensation, die die Lagerung von Ammoniak und herkömmlichen Brennstoffen (außer Erdgas) in flüssigem Zustand ermöglichen. Alle Brennstoffe, einschließlich Ammoniak, haben ähnliche Werte für die maximale (adiabatische) Verbrennungstemperatur – von 1800 bis 2030 °C. Einige physikalische Eigenschaften von NH3 schränken jedoch seine Verwendung in Motoren ein. Daher ist der Wert der volumetrischen Energiedichte von NH3 im Vergleich zu herkömmlichen Kohlenwasserstoffbrennstoffen deutlich niedriger (Tabelle 1). Dies bedeutet, dass sich das Volumen des Brennstoffs (oder der Lagertanks), das zur Erzeugung der gleichen Energiemenge mit NH3 erforderlich ist, um das 2,5- bis 3-fache erhöht. Darüber hinaus hat NH3 im Vergleich zu herkömmlichen Kraftstoffen eine viel höhere Selbstentzündungstemperatur. Für den Betrieb eines Dieselmotors mit Ammoniak sind daher deutlich höhere Verdichtungsverhältnisse – mindestens 35:1 – erforderlich als beim Betrieb mit Dieselkraftstoff (von 14:1 bis 22:1) [1]. Dies stellt erhöhte Anforderungen an die Festigkeit und Korrosionsbeständigkeit der im Motorenbau verwendeten Werkstoffe. Die geringere Flammenausbreitungsgeschwindigkeit bei der Verbrennung von Ammoniak kann zu einer Instabilität des Verbrennungsprozesses führen.
In den Jahren 2019–2020 gaben die größten Hersteller von Dieselmotoren, MAN Energy Solutions (Deutschland) und Wärtsilä (Finnland), den Beginn der Entwicklung von Zwei- und Viertakt-Dieselmotoren auf Ammoniakbasis bekannt [2]. Die größte Aufmerksamkeit wird der Verwendung von Ammoniak als Ersatz für Motorkraftstoff im Seetransportsektor gewidmet. Das norwegische Unternehmen Yara hat den Bau des weltweit ersten emissionsfreien Seeschiffs angekündigt, das mit reinem Ammoniak betrieben wird und keine Kohlenwasserstoffbrennstoffe (Heizöl oder Dieselkraftstoff) verwendet. Es ist geplant, dieses Schiff bereits ab 2026 für den Seetransport von Düngemitteln auf der Route Norwegen-Deutschland einzusetzen.
Um das Problem der unzureichenden Verbrennungseffizienz von Ammoniak in Dieselmotoren zu lösen, wird es derzeit mit einer kleinen Menge normalen Dieselkraftstoffs (dem sogenannten „Pilotkraftstoff“) vermischt, der in das Kraftstoffsystem eingespritzt wird und die Verbrennung von Ammoniak einleitet [1]. Bereits 1977 durchgeführte Versuche zeigten, dass Ammoniak von den vier Hauptkraftstoffen Methanol, Ethanol, Methan und Ammoniak für den Betrieb in einem Dieselmotor selbst in einer Dual-Fuel-Ausführung am wenigsten geeignet ist [3]. Neben erheblichen Emissionen an unvollständig oxidiertem NH3 (bis zu 0,5 Vol.-%) führte sein Einsatz im Vergleich zu anderen Kraftstoffen zu der längsten Zündverzögerung sowie der geringsten Leistungsabgabe und Effizienz (Tabelle 2).

Nach dem Start der Kampagne zur Reduzierung der CO2-Emissionen wurde jedoch die grundsätzliche Anwendbarkeit des Dual-Fuel-Schemas Ammoniak + Diesel für Mehrzylinder-Turbodieselmotoren nachgewiesen. Hierzu waren nur geringfügige Änderungen am Kraftstoffeinlasssystem erforderlich, um die Ammoniak-Zuleitung unterzubringen, während das Kohlenwasserstoff-Kraftstoffeinspritzsystem unverändert blieb [4]. Ein stabiler Motorbetrieb war möglich, indem bis zu 95 % (nach Energie) des Dieselkraftstoffs durch NH3 ersetzt wurden, und mit einem Ammoniakgehalt von 40–60 % im Kraftstoff wurden erhebliche Kraftstoffeinsparungen (höchste Betriebseffizienz) erzielt. Bei NH3-Gehalten unter 60 % konnte eine deutliche Reduzierung der NOx-Emissionen beobachtet werden, die die Autoren auf eine Verringerung der Flammentemperatur zurückführten. Dies führte jedoch zu einer Verringerung der Vollständigkeit der Verbrennung von Dieselkraftstoff, was sich in einem Anstieg der Kohlenwasserstoffemissionen äußerte. Später durchgeführte detailliertere Untersuchungen [5] zeigten, dass bei einem Ammoniakgehalt über 60 % die Verzögerung der Kraftstoffzündung zunahm. Gleichzeitig kann bei einem Anstieg des Dieselkraftstoffanteils über 60 % bei konstanter Motorleistung die Zusammensetzung des Ammoniak-Luft-Gemisches im Motor die Explosionsgrenzen erreichen und ein Absinken der Verbrennungstemperatur verringert die Effizienz der Kraftstoffverbrennung insgesamt. Ein weiteres wichtiges Problem, das bei der Verwendung von Ammoniak in Dual-Fuel-Systemen gelöst werden muss, betrifft das System zur Zufuhr des Ammoniaks zur Brennkammer. So kann Ammoniak in das Einlassventil eingespritzt werden (dadurch entsteht ein homogenes Gemisch aus Kraftstoff und Luft) oder in flüssiger Form direkt in den Zylinder geleitet werden. Letztere Option ist vorzuziehen, da sie die Dosierung von Ammoniak direkt aus Lagertanks in flüssiger Form (bei einem Druck von etwa 17 atm) ohne vorherige Verdampfung ermöglicht. Durch die Dosierung der Flüssigkeit kann der Druck in der Brennkammer deutlich erhöht werden. Aufgrund des hohen Sättigungsdampfdrucks und der starken Abhängigkeit des Sättigungsdampfdrucks von der Temperatur ist Ammoniak jedoch durch sofortiges Sieden und Verdampfen gekennzeichnet, wenn der Druck sinkt. Dieser Effekt ist besonders ausgeprägt in den Ansaugdüsen und verändert die Muster der Bildung von Gas-Luft-Gemischen erheblich, was in einigen Fällen zu einer schlechten Vermischung von Kraftstoff mit Luft und einem tieferen Eindringen von Flüssigkeit in den Motor bis hin zur Benetzung der Wände führt [6]. Außerdem führt bei der Flüssigkeitseinspritzung ein starker Temperaturabfall während der Ammoniakverdampfung zu einer deutlichen Reduzierung der Flammenstabilität. Um diesen negativen Effekt zu verringern, werden eine Vorwärmung und Verwirbelung des der Brennkammer zugeführten Luftstroms vorgeschlagen. Generell sind in diesem Bereich weitere Forschungsarbeiten erforderlich, um die Besonderheiten der Entstehungsprozesse von Ammoniak-Luft-Gemischen und deren Verbrennung in Verbrennungsmotoren zu verstehen und optimale Kraftstoffversorgungsarten zu entwickeln.
Bei MAN Energy Solutions basiert das Ammoniak-Dosiersystem auf ähnlichen Systemen, die zuvor für Flüssiggase und Methanol entwickelt wurden. Es wurde angekündigt, dass bei erfolgreichem Abschluss der Pilottests im Jahr 2023 der erste mit Ammoniak betriebene Zweitaktmotor im Jahr 2024 auf einem Industrieschiff installiert werden soll [7]. Ende 2023 gab die Wärtsilä Corporation bekannt, dass sie den ersten industriellen Viertaktmotor auf den Markt gebracht habe, der mit einem Gemisch aus Diesel und Ammoniak betrieben wird [8], und Anfang 2024, dass sie über ein Ammoniakversorgungssystem verfüge, das sowohl mit flüssigen als auch mit gasförmigen Ausgangsstoffen betrieben werden könne [9]. Sie sollen 2025 auf mittelgroßen LNG-Tankern installiert werden, die speziell zu diesem Zweck auf den Hyundai Mipo-Werften in Südkorea für EXMAR LPG gebaut werden.
Auch die Möglichkeit der Verwendung von Ammoniak im Kraftverkehr wird aktiv untersucht. Diese Arbeiten werden in zwei Richtungen durchgeführt. Erstens wird Ammoniak als Energieträger für Brennstoffzellen verwendet, die den Elektromotor eines Autos antreiben. Eine weitere Verwendungsmöglichkeit für Ammoniak besteht in der Verwendung als direkter Ersatz für Benzin oder Dieselkraftstoff in Verbrennungsmotoren. Der erste derartige Motor wurde bereits im Jahr 2023 von der Allianz aus GAC (China) und Toyota (Japan) demonstriert [10]. Der Hauptanwendungsbereich von Ammoniak im Kraftverkehr sind jedoch Technologien, die auf der Nutzung von Ammoniak-Brennstoffzellen als Energiequelle basieren. Erstens handelt es sich um eine effizientere Methode zur Energiegewinnung aus Ammoniak, die sich durch geringere NH3- und Stickoxidemissionen sowie eine geringere Lärmentwicklung auszeichnet [2]. Brennstoffzellen selbst benötigen deutlich weniger Platz als Verbrennungsmotoren. Am vielversprechendsten sind Protonenaustauschmembran-Brennstoffzellen (PEMFC) und Festoxidbrennstoffzellen (SOFC) [11]. Prototypen von PEMFC (jedoch ohne Verwendung von Ammoniak als H2-Quelle) werden bereits im Bodentransport eingesetzt. Die für ihren Betrieb erforderlichen Zusatzgeräte (Kühlsysteme, Belüftung, Kraftstoffversorgung usw.) sind in etwa dieselben wie bei einem herkömmlichen Motor. Das Hauptproblem bei der Umstellung auf Ammoniak in PEMFC-Brennstoffzellen besteht darin, dass die Reinheit des H2 nicht unter > 99,5 % liegen darf und keinerlei Spuren von NH3 vorhanden sein dürfen. SOFC-Brennstoffzellen können Ammoniak ohne vorherige Zersetzung und H2-Emission als Brennstoff verwenden, wodurch höhere Leistungswerte pro Gewichtseinheit Brennstoff erreicht werden können. Allerdings benötigen SOFC-Brennstoffzellen ein Energiespeichersystem, um langsame Prozesse während Übergangsbedingungen auszugleichen und sie während des Anlaufs mit Energie zu versorgen. Die Verwendung von Ammoniak als Energieträger ist nicht auf den Transport beschränkt. Derzeit wird intensiv daran geforscht, Kohlenwasserstoffbrennstoffe in Gasturbinen durch Ammoniak zu ersetzen. Um den CO2-Fußabdruck in der Wärmekrafttechnik zu reduzieren, wird ein Verfahren zur verträglichen Verbrennung von Kohle und Ammoniak entwickelt.
Die meisten Veröffentlichungen zum Brennstoff- und Energieverbrauch von Ammoniak haben in erster Linie werblichen Charakter und beschränken sich bestenfalls auf die Bewertung der Reduzierung der Kohlendioxidemissionen. Experimentelle Daten zum Gehalt anderer Verbindungen in den Abgasen von Verbrennungsmotoren werden im Allgemeinen nicht bereitgestellt. Allerdings können bei der Verbrennung von Ammoniak neben umweltfreundlichem Stickstoff auch verschiedene Formen von Stickoxiden (NO, NO2, N2O) entstehen:
2NH3 + 3/2O2 = N2+ 3H2O + 634 kJ/mol (1)2NH3 + 2O2 = N2O + 3H2O + 552 kJ/mol (2)2NH3 + 5/2O2 = 2NO + 3H2O + 453 kJ/mol (3)
2NO + O2 = 2NO2–113 kJ/mol (4)
Ihr Gehalt in Verbrennungsprodukten kann 0,28 Vol.-% erreichen. Darüber hinaus beträgt die Restkonzentration von Ammoniak im Abgas aufgrund der geringen Verbrennungseffizienz selbst unter optimalen Verbrennungsbedingungen 0,1–0,3 Vol.-%. [12]. NH3 verursacht bereits in geringen Konzentrationen in der Luft (0,0005–0,005 Vol.-%) Reizungen der Augen und Atemwege, bei einem Gehalt von ~1 Vol.-% sogar Reizungen der Augen und Atemwege. der sofortige Tod tritt ein. Stickoxidemissionen tragen zur Bildung von Photosmog und saurem Regen sowie zur Zersetzung der Ozonschicht bei. Eine Konzentration von NO2, das bei Raumtemperatur aus NO gebildet wird, von mehr als 0,02 Vol.-%. gilt als tödlich. Eine erhöhte Effizienz der NH3-Verbrennung und eine Reduzierung der NO- und NO2-Emissionen werden durch die Vorwärmung des Kraftstoffs sowie durch eine zusätzliche Erhöhung des Drucks in der Brennkammer erreicht (letzterer ist bereits höher als beim Arbeiten mit Dieselkraftstoff). Eine gute Alternative zu unsicheren und teuren Druck- oder Temperaturerhöhungen kann der Einsatz industrieller Technologie zur Reduzierung der Stickoxidemissionen sein, die auf der selektiven katalytischen Reduktion mit Ammoniak (SCR NH3) zu Stickstoff und Wasser basiert und auf den folgenden Reaktionen beruht:
6NO + 4NH3 → 5 N2 + 6H2O + 1095 kJ/mol (5)4NO + 4NH3 + O2 → 4N2 + 6H2O + 1629 kJ/mol (6)6NO2 + 8NH3 → 7N2 + 12H2O + 2737 kJ/mol (7)
2NO2 + 4NH3 + O2 → 3 N2 + 6H2O + 1335 kJ/mol (8)
In den letzten Jahren wurde diese katalytische Technologie für den Güter- und Seetransport adaptiert, wobei Produkte auf Basis hochsiedender Erdölfraktionen mit einem relativ hohen Gehalt an stickstoffhaltigen Verbindungen als Kraftstoff verwendet werden [13]. Die hohe korrosive Aktivität von Ammoniak stellt besondere Anforderungen an die Werkstoffe für Motoren und Kraftstoffversorgungssysteme sowie an dessen Reinheit. Daher dürfen in Kraftstoffsystemen, Behältern zu deren Lagerung und Versorgungsleitungen keine Legierungen mit Kupfer und Nickel verwendet werden, deren Gehalt an Nickel über 6 % liegt. Für Dichtungen und Isolierungen in solchen Systemen ist ausschließlich Teflon geeignet. Aufgrund der beschleunigten Spannungsrisskorrosion von Stahl, insbesondere bei erhöhten Temperaturen, in Gegenwart von Feuchtigkeit und Luft, sollte ihr maximaler Ammoniakgehalt 0,1 Gew.-% nicht überschreiten. und mehrere Millionstel. Um die erforderliche Reinheit des Kraftstoffs sicherzustellen, sind daher spezielle Technologien erforderlich.
Welche Probleme lassen sich bei der Umstellung des Verkehrs auf Ammoniakkraftstoff feststellen? Dies sind vor allem: a) Korrosionsprobleme, wenn Motorelemente mit Ammoniak in Berührung kommen; b) hohe Toxizität von Ammoniak; c) relativ geringe spezifische Energiekapazität von Ammoniak als Brennstoff; d) Bildung von Stickoxiden aus Ammoniak bei dessen Verbrennung. Es lohnt sich, die technischen und wirtschaftlichen Aussichten von Ammoniak als Kraftstoff zu betrachten. Der geringere Heizwert von Ammoniak im Vergleich zu Dieselkraftstoff wird durch seine niedrigen Kosten in Russland fast ausgeglichen. Dies bedeutet, dass Ammoniak als Kraftstoff bereits heute preislich konkurrenzfähig ist. Bei bestehenden Verfahren zur Synthese von Ammoniak aus Erdgas entsteht zwangsläufig Kohlendioxid – etwa 2,5 Tonnen CO2 pro 1 Tonne Ammoniak. Die Entsorgung von konzentriertem CO2 vor Ort ist wesentlich günstiger und technologisch einfacher als die Lösung dieses Problems für ein einzelnes mit Kohlenwasserstoffen betriebenes Fahrzeug. Somit eröffnet die Verwendung von Ammoniak in technologischen Prozessen Möglichkeiten zur Schaffung eines Transports ohne CO2-Fußabdruck. Die kommerzielle Nutzung von Ammoniak in dieser Kapazität wird voraussichtlich in den Jahren 2035–2037 beginnen. Bis 2050 wird der Seeverkehr voraussichtlich überwiegend mit Flüssigerdgas (65–70 %) und Ammoniak (20–25 %) betrieben. Der Anteil an schwefelarmem Heizöl wird lediglich 10 % betragen. Dies wird dazu führen, dass die weltweite Ammoniakproduktion bis 2050 verdoppelt werden muss – auf 400 Millionen Tonnen pro Jahr.
Der Einsatz von Ammoniak in der Schifffahrt und im Straßenverkehr wird zwangsläufig der Entwicklung von Verbrennungsmotoren neue Impulse verleihen. Ammoniakmotoren können sich stark von Benzin- oder Dieselmotoren unterscheiden. Möglicherweise ist Ammoniak kein Monokraftstoff und erfordert die Einführung spezieller Additive (ähnlich wie Oktanzahl-erhöhende Additive). Die Notwendigkeit, die Ammoniakproduktionskapazität zu erhöhen, fördert die Entwicklung neuer Technologien für die Ammoniaksynthese. Dies wird zu einer Intensivierung der wissenschaftlichen Forschung im Bereich der katalytischen Prozesse im Zusammenhang mit der Ammoniaksynthese und der industriellen Nutzung der Ergebnisse dieser Arbeiten führen.
Die Arbeiten wurden mit finanzieller Unterstützung des Ministeriums für Wissenschaft und Hochschulbildung der Russischen Föderation im Rahmen des staatlichen Auftrags des Instituts für Katalyse SB RAS (Projekt FWUR-2024-37) durchgeführt.
energypolicy